Pyrolysis plants are highly efficient systems designed to convert organic materials into valuable products like bio-oil, syngas, and biochar. Their efficiency is influenced by factors such as feedstock composition, moisture content, particle size, reactor design, and operational parameters like temperature, pressure, and residence time. Pyrolysis plants are versatile, capable of handling various feedstocks, including wood, rubber, and plastic, and are environmentally friendly due to advanced pollution control systems. While the efficiency of pyrolysis varies depending on the process and feedstock, it remains a competitive and sustainable alternative to traditional methods, especially when combined with carbon capture technologies.
Key Points Explained:
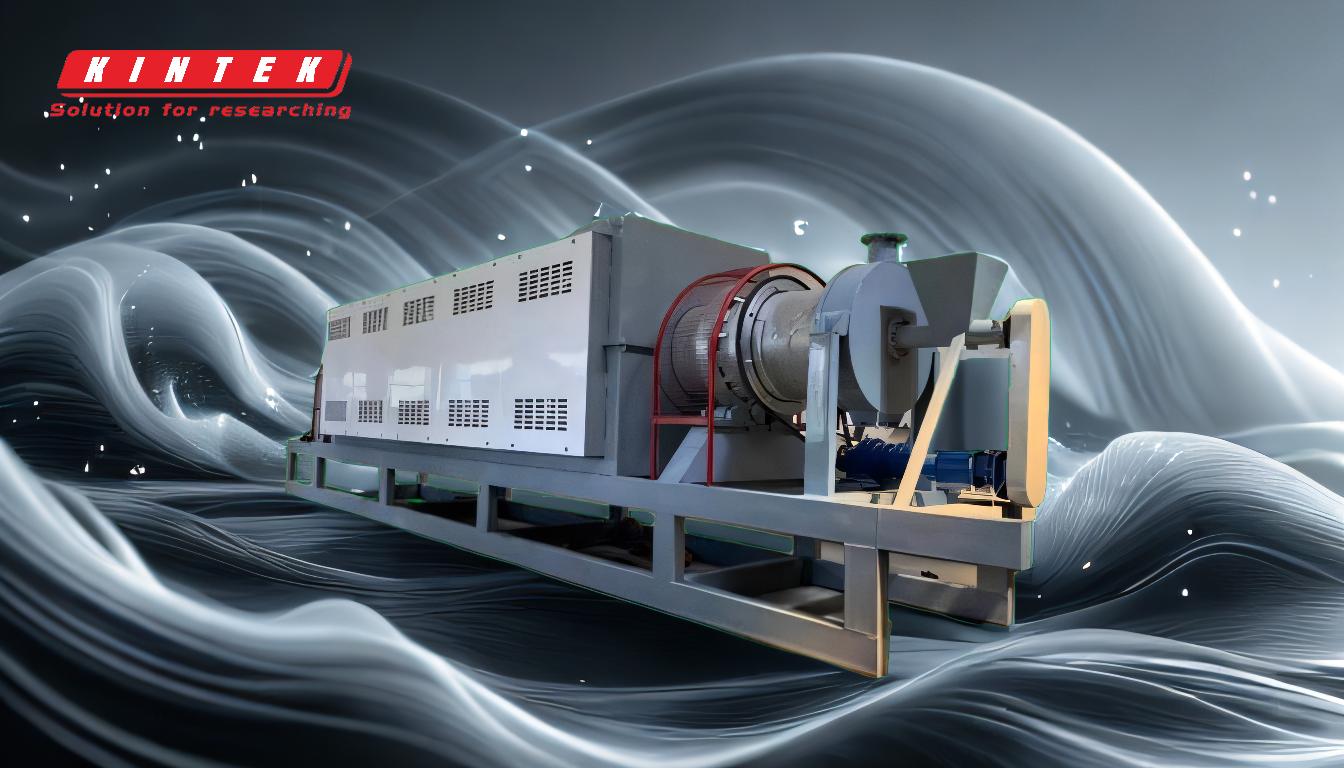
-
Factors Influencing Pyrolysis Efficiency
- Feedstock Composition: The type and composition of the feedstock significantly impact the efficiency of a pyrolysis plant. Organic materials with high cellulose and lignin content, such as wood, yield higher amounts of bio-oil and syngas.
- Moisture Content: Optimal moisture content is around 10%. Higher moisture levels produce excessive water, reducing energy efficiency, while lower levels may lead to dust formation instead of oil.
- Particle Size: Smaller particle sizes (up to 2 mm) ensure rapid heat transfer, improving the overall efficiency of the pyrolysis process.
-
Reactor Design and Configuration
- Reactor Types: Pyrolysis plants typically include a reactor, condenser, and energy module. Some designs combine the reactor and energy module to reduce energy losses, though this requires advanced temperature control and high-quality materials.
- Batch vs. Continuous Processes: Batch processes use retorts, while continuous processes are more efficient for large-scale operations. The choice depends on the scale and desired outputs.
-
Operational Parameters
- Temperature and Pressure: Optimal temperature and pressure settings are critical for maximizing the yield of desired products. For example, higher temperatures favor gas production, while moderate temperatures are better for bio-oil.
- Residence Time: The time the feedstock spends in the reactor affects the extent of degradation and conversion. Proper control ensures efficient heat transfer and product formation.
-
Environmental and Economic Benefits
- Pollution Control: Pyrolysis plants are equipped with de-dusting systems and hydroseals to minimize emissions, making them environmentally friendly.
- Economic Viability: The low production cost and high profitability of pyrolysis plants make them an attractive investment. The produced oil is of high quality and can be sold directly or further refined.
-
Comparison with Other Technologies
- Steam Methane Reforming (SMR): While SMR is more efficient (75%) than methane pyrolysis (58%), the efficiency gap narrows when carbon capture and sequestration are added to SMR (60% vs. 58%). This makes methane pyrolysis a competitive alternative, especially for carbon-neutral goals.
-
Applications and Feedstocks
- Wood Feedstock: Pyrolysis plants for wood processing can be customized based on scale, desired outputs, and available resources. Consulting with experts ensures the selection of the most suitable design.
- Rubber Feedstock: Rubber pyrolysis plants feature advanced condensing units with large heat transfer areas, improving cooling efficiency and product output. The closed design ensures safety and environmental protection.
-
Energy Efficiency and Maintenance
- Rotary Running: This feature ensures efficient heating and energy savings, making the process more sustainable.
- Maintenance: Proper operation and maintenance are crucial for optimal performance and safety, ensuring the longevity and efficiency of the pyrolysis plant.
In conclusion, pyrolysis plants are efficient, versatile, and environmentally friendly systems that offer significant economic and environmental benefits. Their efficiency depends on careful design, feedstock selection, and operational control, making them a sustainable choice for waste-to-energy conversion.
Summary Table:
Key Factors | Details |
---|---|
Feedstock Composition | High cellulose/lignin content (e.g., wood) yields more bio-oil and syngas. |
Moisture Content | Optimal at ~10%; higher levels reduce energy efficiency. |
Particle Size | Smaller particles (<2 mm) improve heat transfer and efficiency. |
Reactor Design | Batch vs. continuous processes; advanced designs reduce energy losses. |
Temperature & Pressure | Optimal settings maximize product yield (e.g., bio-oil or syngas). |
Residence Time | Proper control ensures efficient heat transfer and product formation. |
Environmental Benefits | Advanced pollution control systems minimize emissions. |
Economic Viability | Low production costs and high profitability make it a sustainable choice. |
Ready to enhance your waste-to-energy efficiency? Contact us today to find the perfect pyrolysis solution for your needs!