To determine the optimal filling level for a ball mill, it's essential to balance productivity and milling efficiency. Overfilling can lead to inefficiencies, such as collisions between rising and falling balls, while underfilling may reduce grinding capacity. Based on the references, the recommended filling level is around 50% of the mill's volume with grinding media, with a maximum limit of 55% to account for wear. This ensures sufficient voids (20% of the cylinder volume) for effective grinding. However, some sources suggest a lower limit of 30–35% to avoid excessive collisions. Ultimately, the ideal filling level depends on the specific application and operational goals.
Key Points Explained:
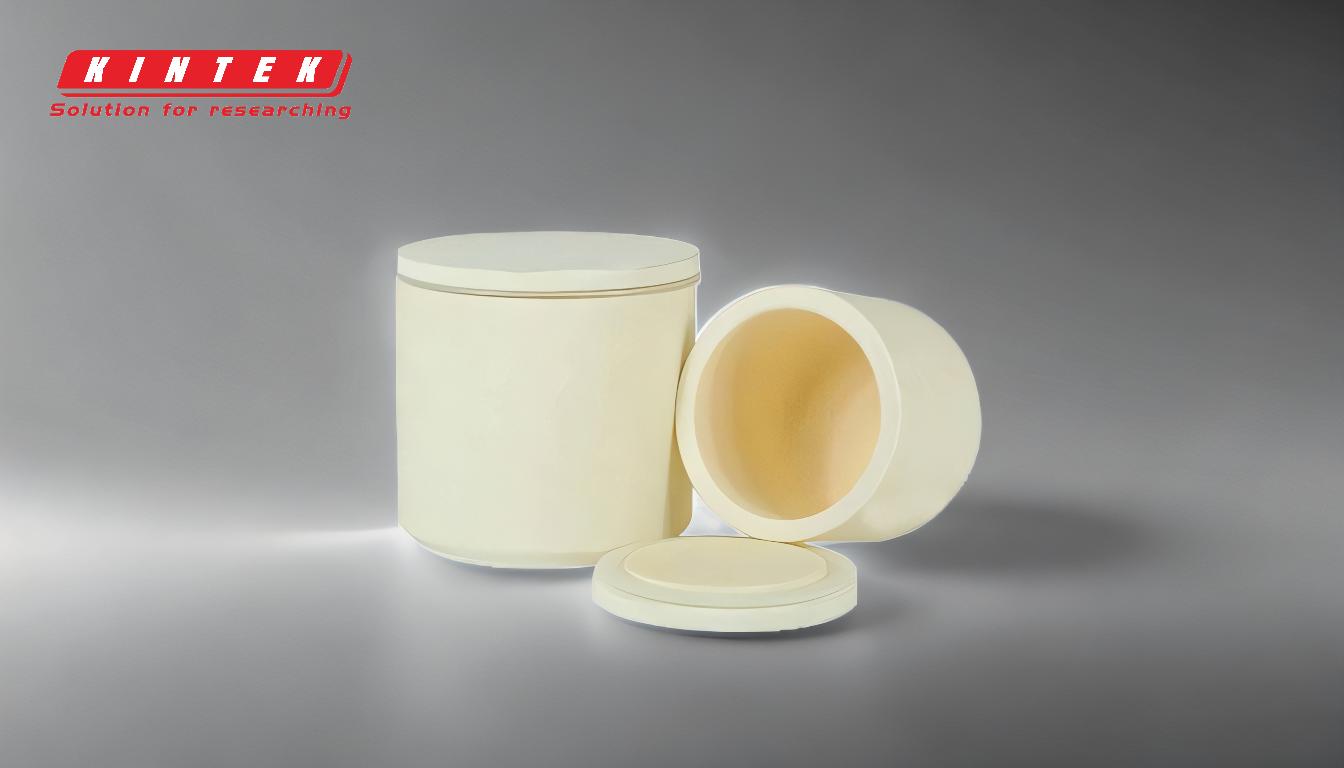
-
Optimal Filling Level: 50% of Mill Volume
- The mill should be filled half full with grinding media to achieve the best results.
- This level creates voids equal to 20% of the cylinder volume, which are essential for effective grinding.
-
Upper Limit: 55% to Compensate for Wear
- Some operators choose to fill the mill slightly above 50% (up to 55%) to account for wear and tear on the grinding media.
- This slight increase ensures consistent performance over time without significantly impacting efficiency.
-
Avoid Overfilling: Maximum 30–35% for Efficiency
- Overfilling the mill (beyond 30–35% of its volume) can lead to inefficiencies.
- Excessive filling causes rising balls to collide with falling ones, reducing the overall milling efficiency.
-
Impact of Voids on Grinding
- The voids created by the grinding media (20% of the cylinder volume) are crucial for the grinding process.
- These voids allow the balls to move freely and effectively grind the material.
-
Application-Specific Considerations
- The ideal filling level may vary depending on the specific application, material being ground, and operational goals.
- Operators should consider factors such as the type of grinding media, mill size, and desired output when determining the optimal filling level.
-
Balancing Productivity and Efficiency
- While higher filling levels may increase productivity, they can also reduce efficiency due to increased collisions.
- Striking the right balance between filling level and operational efficiency is key to achieving optimal results.
By adhering to these guidelines, operators can ensure that their ball mills operate at peak efficiency, maximizing productivity while minimizing wear and inefficiencies.
Summary Table:
Key Aspect | Recommendation |
---|---|
Optimal Filling Level | 50% of mill volume with grinding media |
Upper Limit (Wear Compensation) | Up to 55% to account for wear and maintain performance |
Avoid Overfilling | Maximum 30–35% to prevent inefficiencies and excessive collisions |
Voids for Effective Grinding | 20% of cylinder volume is essential for free movement and grinding efficiency |
Application-Specific Factors | Adjust filling level based on material, mill size, and operational goals |
Balancing Productivity | Higher filling levels may boost output but reduce efficiency due to collisions |
Optimize your ball mill performance today—contact our experts for personalized guidance!