Measuring coating thickness is a critical process in various industries, ensuring the quality, durability, and performance of coated materials. The most common method for measuring nonmagnetic coatings on ferrous substrates is through magnetic film gauges, also known as paint depth gauges. These devices operate using either magnetic pull-off or magnetic/electromagnetic induction principles. Additionally, factors such as insulation thickness are influenced by operating temperatures and hot zone size, which must be considered in specific applications. Below, we’ll explore the key principles, methods, and considerations for measuring coating thickness.
Key Points Explained:
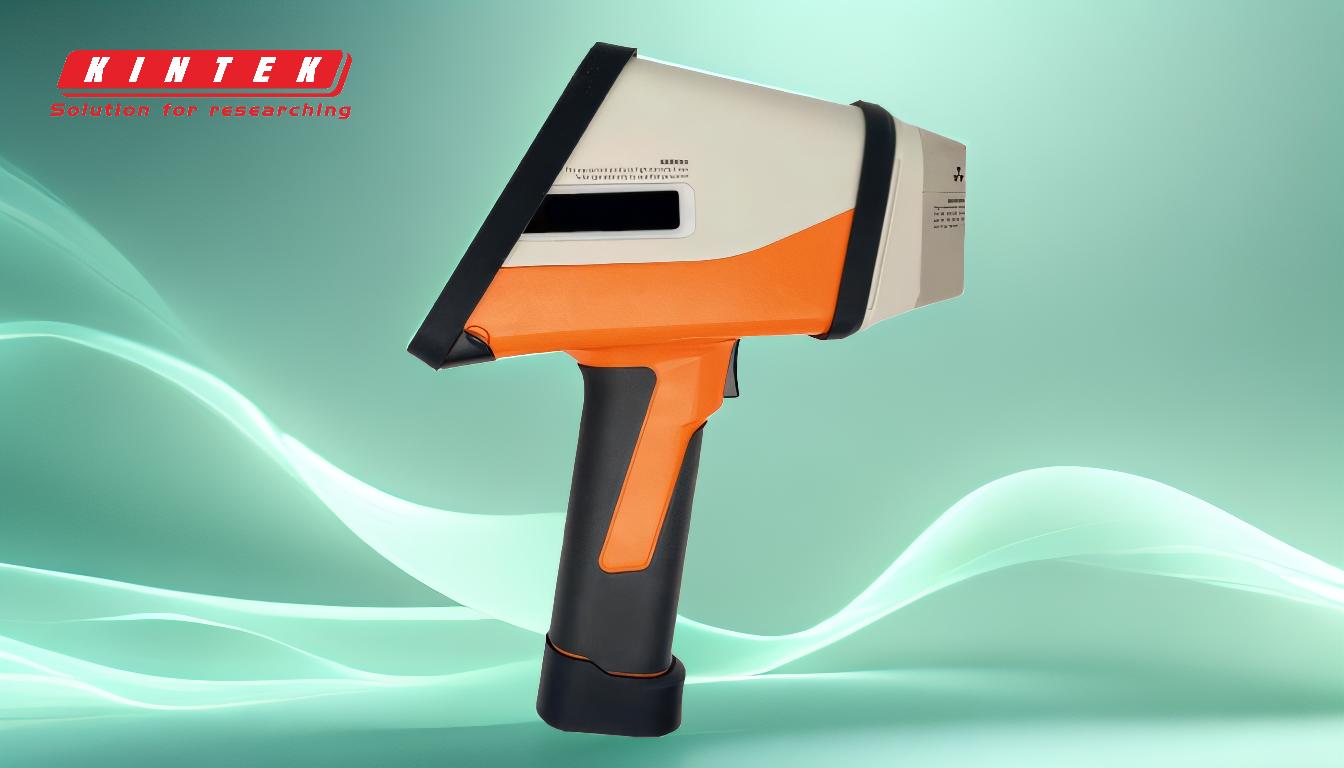
-
Magnetic Film Gauges for Coating Thickness Measurement
- Magnetic film gauges, or paint depth gauges, are widely used to measure the thickness of nonmagnetic coatings on ferrous substrates like steel and iron.
- These devices are non-destructive, meaning they do not damage the coating or substrate during measurement.
- Two primary principles are used:
- Magnetic Pull-Off: This method measures the force required to pull a magnet away from the coated surface. The force correlates with the thickness of the nonmagnetic coating.
- Magnetic/Electromagnetic Induction: This technique uses electromagnetic fields to measure the distance between the sensor and the ferrous substrate, providing an accurate coating thickness reading.
-
Applications of Magnetic Film Gauges
- These gauges are commonly used in industries such as automotive, construction, and manufacturing, where coatings like paint, powder coatings, or galvanized layers are applied to steel or iron.
- They are ideal for quality control, ensuring that coatings meet specified thickness requirements for performance and durability.
-
Factors Influencing Coating Thickness Measurement
- Substrate Material: Magnetic film gauges are specifically designed for ferrous substrates. For non-ferrous materials, other methods like eddy current testing are used.
- Coating Type: The method is suitable for nonmagnetic coatings. Magnetic coatings require alternative measurement techniques.
- Surface Roughness: Irregular surfaces can affect measurement accuracy, so smooth and uniform surfaces are preferred.
-
Insulation Thickness Considerations
- Insulation thickness is another critical parameter, especially in high-temperature applications.
- The thickness is determined based on:
- Maximum Operating Temperatures: Higher temperatures may require thicker insulation to prevent heat loss or damage.
- Hot Zone Size: Larger hot zones may necessitate adjustments in insulation thickness to maintain uniform temperature distribution.
-
Alternative Methods for Coating Thickness Measurement
- While magnetic film gauges are ideal for ferrous substrates, other methods include:
- Eddy Current Testing: Used for non-conductive coatings on non-ferrous metals.
- Ultrasonic Testing: Measures thickness by analyzing sound waves reflected from the substrate.
- Micrometer Measurements: A mechanical method for measuring thick coatings, though it is less precise for thin layers.
- While magnetic film gauges are ideal for ferrous substrates, other methods include:
-
Importance of Accurate Coating Thickness Measurement
- Ensures compliance with industry standards and specifications.
- Prevents issues like under-coating (leading to corrosion) or over-coating (resulting in material waste and increased costs).
- Enhances the longevity and performance of coated materials.
By understanding the principles and methods of coating thickness measurement, industries can ensure the quality and reliability of their coated products. Magnetic film gauges are particularly valuable for their non-destructive nature and accuracy, making them a preferred choice for ferrous substrates. Additionally, considering factors like insulation thickness and operating conditions further refines the measurement process, ensuring optimal performance in various applications.
Summary Table:
Aspect | Details |
---|---|
Primary Method | Magnetic film gauges (paint depth gauges) |
Operating Principles | Magnetic pull-off or magnetic/electromagnetic induction |
Applications | Automotive, construction, manufacturing (ferrous substrates) |
Key Factors | Substrate material, coating type, surface roughness |
Alternative Methods | Eddy current testing, ultrasonic testing, micrometer measurements |
Importance | Ensures compliance, prevents under/over-coating, enhances durability |
Need help measuring coating thickness accurately? Contact our experts today for tailored solutions!