The process of making zirconia teeth involves several stages, each contributing to the final product's strength, durability, and aesthetic appeal. From the initial powder form to the fully sintered restoration, the entire process typically takes 5-7 days, depending on the complexity of the case, the equipment used, and the workflow of the dental lab. The stages include preparing zirconia powder, compacting it into a "green state," pre-sintering to create "bisque state" blocks, milling the restoration, and finally performing full sintering. Each step is crucial to ensure the final product meets the required standards for dental restorations.
Key Points Explained:
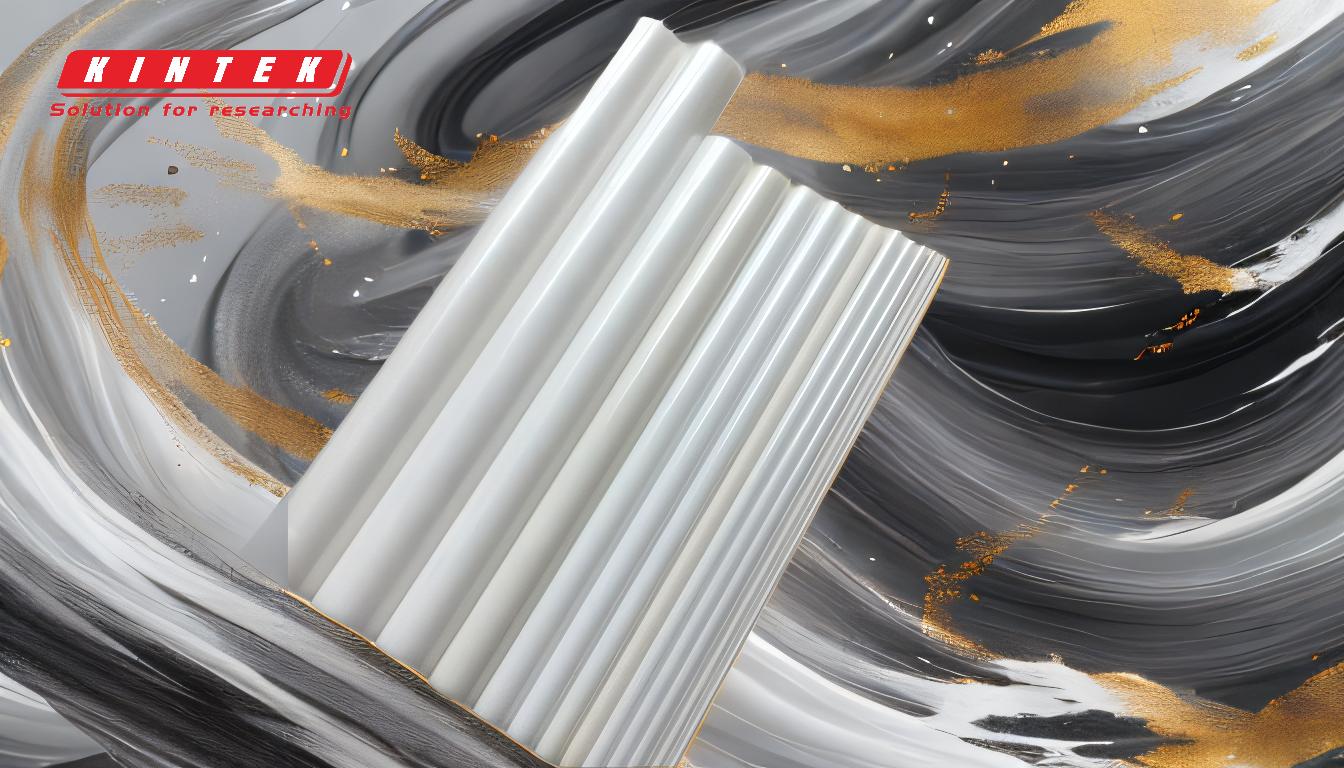
-
Zirconia Preparation (1-2 Days)
- Zirconia starts as a fine powder, which is mixed with binders and pigments to achieve the desired shade and strength.
- The powder is then compacted into a "green state" using high-pressure techniques. This stage is critical for ensuring uniformity and reducing porosity.
- The green state zirconia is soft and malleable, making it easier to shape and mill in later stages.
-
Pre-Sintering (1 Day)
- The green state zirconia is pre-sintered at a lower temperature (around 1,000°C) to create "bisque state" blocks.
- Pre-sintering removes the binders and partially densifies the material, making it strong enough to be milled without breaking.
- This stage also ensures the zirconia retains its shape and dimensional stability during milling.
-
Milling (1-2 Days)
- The bisque state zirconia is milled using CAD/CAM technology to create the precise shape of the dental restoration.
- Milling time depends on the complexity of the design, the number of units, and the type of milling machine used.
- High-precision milling ensures minimal material waste and accurate fit for the patient.
-
Full Sintering (1-2 Days)
- After milling, the zirconia restoration undergoes full sintering at high temperatures (1,400-1,500°C) to achieve its final strength, density, and hardness.
- Full sintering shrinks the zirconia by approximately 20-25%, so the design must account for this shrinkage during milling.
- This stage is critical for ensuring the restoration's durability and resistance to wear.
-
Finishing and Polishing (1 Day)
- Once sintered, the zirconia restoration is polished and glazed to achieve a natural, lifelike appearance.
- Additional staining or layering may be applied to match the patient's tooth color perfectly.
- Final quality checks ensure the restoration meets all clinical and aesthetic requirements.
By following these stages, dental labs can produce high-quality zirconia teeth that are both functional and aesthetically pleasing. The total time of 5-7 days ensures each step is performed meticulously, resulting in a durable and precise dental restoration.
Summary Table:
Stage | Duration | Key Details |
---|---|---|
Zirconia Preparation | 1-2 Days | Mixing powder with binders, compacting into "green state" for uniformity. |
Pre-Sintering | 1 Day | Heating at 1,000°C to create "bisque state" blocks for milling. |
Milling | 1-2 Days | CAD/CAM milling for precise restoration shapes, minimizing waste. |
Full Sintering | 1-2 Days | High-temperature sintering (1,400-1,500°C) for final strength and density. |
Finishing and Polishing | 1 Day | Polishing, glazing, and staining for a natural, lifelike appearance. |
Interested in high-quality zirconia teeth for your dental lab? Contact us today to learn more!