The cost of a production mold, particularly a press mold, varies significantly depending on factors such as material, complexity, size, and production volume. Typically, molds for simple parts can range from a few thousand dollars, while highly complex molds for large-scale production can cost tens or even hundreds of thousands of dollars. Key factors influencing cost include mold design, material selection, machining precision, and post-processing requirements. Understanding these variables is crucial for budgeting and ensuring the mold meets production needs.
Key Points Explained:
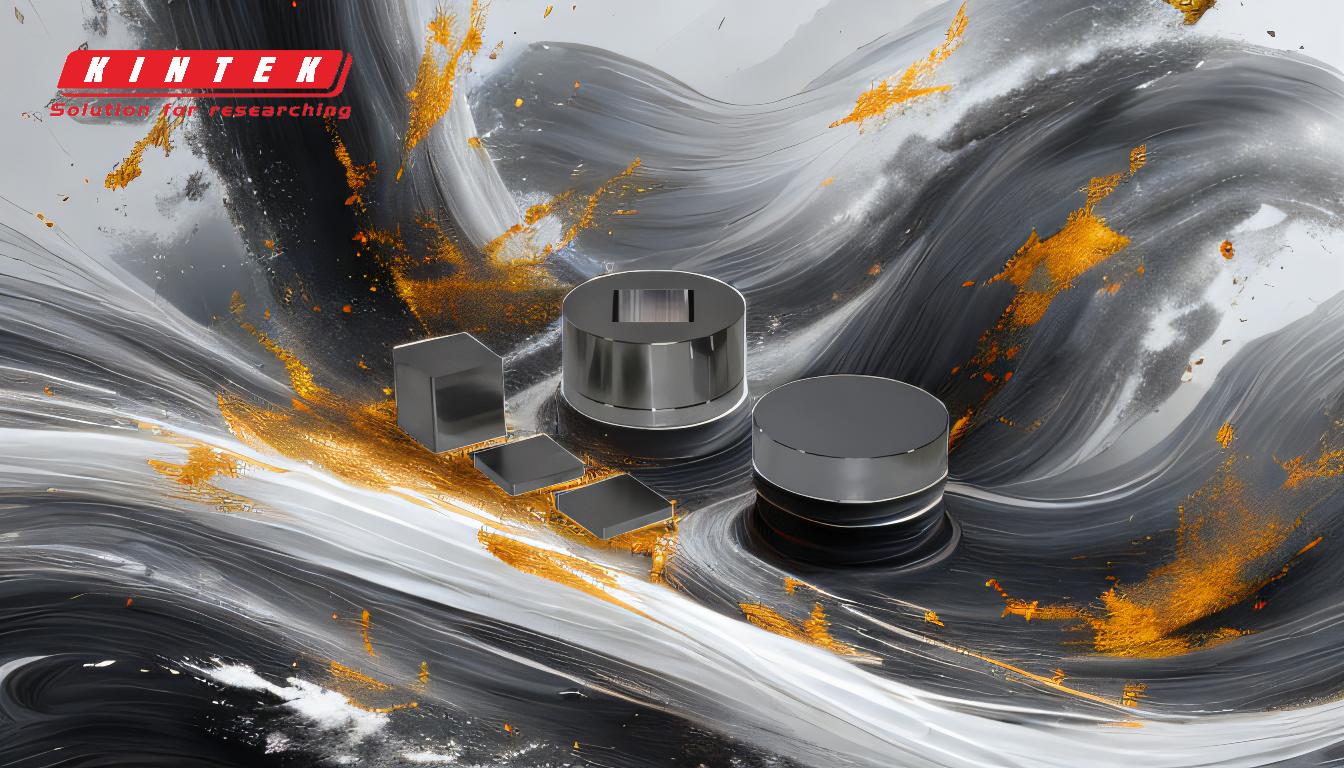
-
Factors Influencing Mold Cost
- Complexity of Design: The more intricate the mold design, the higher the cost due to increased machining time and precision requirements.
- Material Selection: Materials like steel or aluminum impact cost. Steel molds are more durable but expensive, while aluminum molds are cheaper but less durable.
- Size and Weight: Larger molds require more material and specialized equipment, driving up costs.
- Production Volume: High-volume production molds are built to withstand wear and tear, increasing upfront costs but reducing long-term expenses.
- Surface Finish and Tolerances: Molds requiring high surface finishes or tight tolerances demand advanced machining techniques, adding to the cost.
-
Types of Press Molds
- Single-Cavity Molds: Cost-effective for low-volume production but less efficient for high-volume needs.
- Multi-Cavity Molds: Allow for multiple parts to be produced simultaneously, increasing efficiency but at a higher initial cost.
- Family Molds: Produce different parts in one mold, reducing tooling costs but requiring precise design to avoid defects.
-
Cost Breakdown
- Design and Engineering: Includes CAD modeling, simulations, and prototyping, typically accounting for 10-20% of the total cost.
- Machining and Fabrication: The bulk of the cost, covering CNC machining, EDM, and other processes.
- Post-Processing: Includes heat treatment, polishing, and coating, which add to the final cost.
- Maintenance and Repairs: Regular maintenance ensures longevity, but repairs can add unexpected costs over time.
-
Cost Ranges
- Simple Molds: $2,000–$10,000 for basic designs and low-volume production.
- Medium-Complexity Molds: $10,000–$50,000 for molds with moderate complexity and medium production volumes.
- High-Complexity Molds: $50,000–$200,000+ for large, intricate molds designed for high-volume production.
-
Cost-Saving Strategies
- Optimize Design: Simplify mold geometry to reduce machining time and material usage.
- Material Selection: Choose materials based on production needs to balance cost and durability.
- Standardize Components: Use standard mold bases and components to reduce custom machining costs.
- Partner with Experienced Manufacturers: Experienced manufacturers can provide cost-effective solutions and avoid costly mistakes.
-
Long-Term Considerations
- Durability vs. Cost: Investing in a high-quality mold may have a higher upfront cost but can save money in the long run by reducing maintenance and replacement needs.
- Scalability: Consider future production needs to avoid redesigning or replacing molds as demand grows.
By understanding these factors and working closely with manufacturers, you can make informed decisions about press mold costs and ensure your production process is both efficient and cost-effective.
Summary Table:
Factor | Impact on Cost |
---|---|
Complexity of Design | Intricate designs increase machining time and precision requirements, raising costs. |
Material Selection | Steel molds are durable but expensive; aluminum molds are cheaper but less durable. |
Size and Weight | Larger molds require more material and specialized equipment, increasing costs. |
Production Volume | High-volume molds have higher upfront costs but lower long-term expenses. |
Surface Finish | High surface finishes or tight tolerances demand advanced techniques, adding cost. |
Cost Ranges | Simple: $2,000–$10,000; Medium: $10,000–$50,000; High: $50,000–$200,000+. |
Need help estimating your mold costs? Contact our experts today for a tailored solution!