CVD diamond coatings are widely used across various industries due to their exceptional properties, such as high thermal conductivity, hardness, and chemical stability. The thickness of these coatings can vary depending on the application, but typical thicknesses for PACVD coatings range between 2–3 µm. CVD diamond is utilized in high-performance tools, electronics, optical components, and even biomedical applications. Its versatility makes it suitable for applications like heat sinks, cutting tools, and non-stick coatings, provided the coating process is economically viable for large substrate areas. Optical applications, such as CVD diamond domes, benefit from its scratch resistance and thermal properties, making it ideal for use in harsh environments like aerospace and defense.
Key Points Explained:
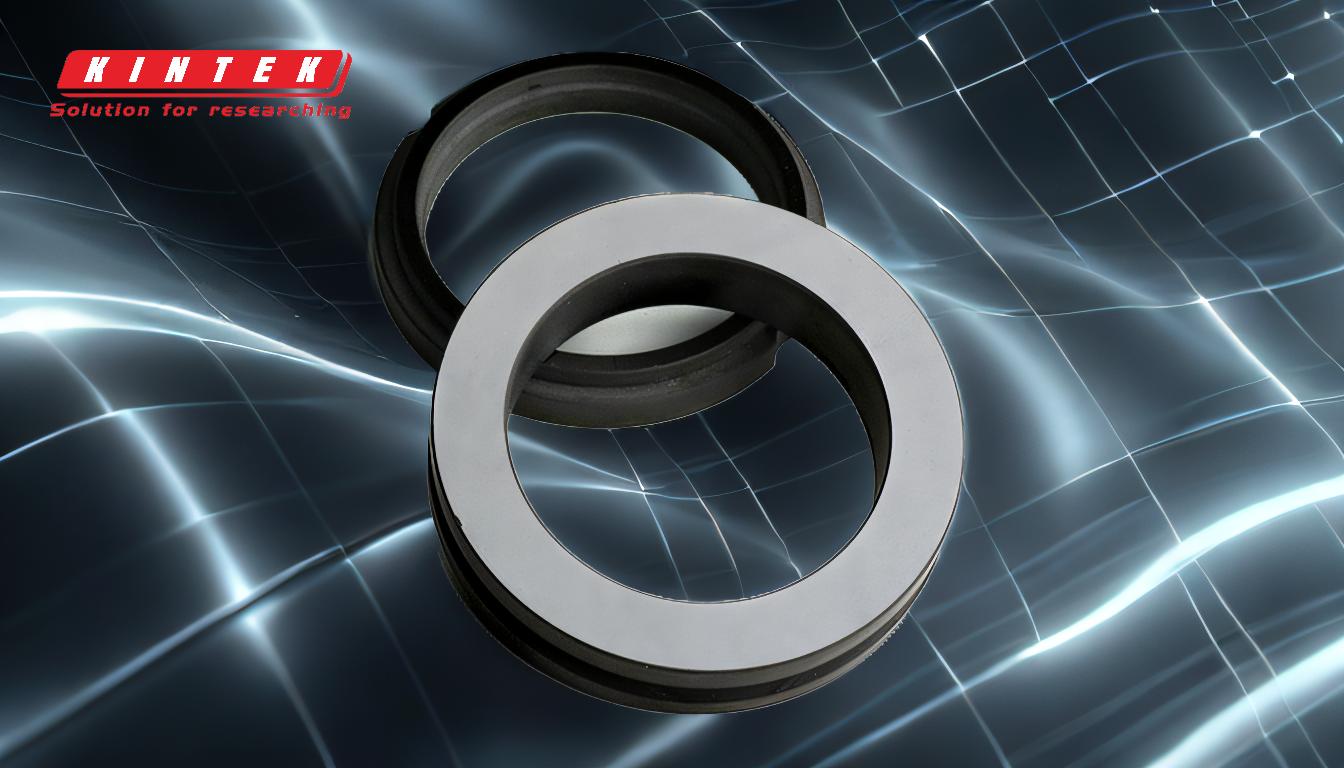
-
Typical Thickness of CVD Diamond Coatings:
- The thickness of CVD diamond coatings typically ranges from 2–3 µm for PACVD (Plasma-Assisted Chemical Vapor Deposition) coatings. This thickness is sufficient for many industrial applications, including cutting tools and heat sinks, where durability and thermal conductivity are critical.
-
Applications Influencing Thickness:
- The thickness of CVD diamond coatings is tailored to the specific application. For example:
- Cutting Tools: Thinner coatings (2–3 µm) are often used to maintain sharpness and precision.
- Optical Components: Coatings for CVD diamond domes and windows may vary in thickness depending on the required optical properties and environmental resistance.
- Heat Sinks: Thicker coatings may be used in high-power electronic devices to enhance thermal conductivity and heat dissipation.
- The thickness of CVD diamond coatings is tailored to the specific application. For example:
-
Optical Applications of CVD Diamond:
- CVD diamond is widely used in optical applications, such as windows, lenses, and domes, due to its transparency across a wide range of wavelengths (from X-ray to microwave). Its scratch resistance and thermal stability make it ideal for harsh environments, including aerospace and defense systems.
-
Thermal and Mechanical Properties:
- CVD diamond's high thermal conductivity and hardness make it suitable for applications requiring efficient heat dissipation and durability. For instance, it is used in the heat dissipation of high-power semiconductor devices and as a coating for cutting tools.
-
Economic Considerations:
- While CVD diamond coatings offer exceptional performance, their economic viability depends on the ability to coat large substrate areas efficiently. Advances in CVD technology are making it more cost-effective for applications like non-stick cookware and industrial tools.
-
Future Trends:
- The development of CVD diamond coatings is rapidly advancing, particularly in high-power electronics and thermal management applications. As technology progresses, we can expect further innovations in coating thickness optimization and large-scale production methods.
By understanding the typical thickness and application-specific requirements of CVD diamond coatings, purchasers can make informed decisions tailored to their needs, whether for industrial tools, optical components, or thermal management solutions.
Summary Table:
Application | Typical Thickness | Key Benefits |
---|---|---|
Cutting Tools | 2–3 µm | Maintains sharpness and precision for high-performance tools. |
Optical Components | Varies | Scratch resistance, thermal stability, and transparency for harsh environments. |
Heat Sinks | Thicker coatings | Enhances thermal conductivity and heat dissipation in high-power electronics. |
Need help selecting the right CVD diamond coating for your needs? Contact our experts today!