Gold coating for SEM (Scanning Electron Microscopy) is a critical step in sample preparation to ensure proper conductivity and prevent charging effects. The thickness of the gold coating typically ranges from 5 to 20 nanometers (nm), depending on the sample type, the resolution required, and the specific SEM instrument being used. A thinner coating (5-10 nm) is preferred for high-resolution imaging to minimize interference with fine surface details, while a thicker coating (10-20 nm) may be used for less conductive or rough samples to ensure adequate conductivity. The coating process is usually performed using a sputter coater, which deposits a uniform layer of gold onto the sample surface.
Key Points Explained:
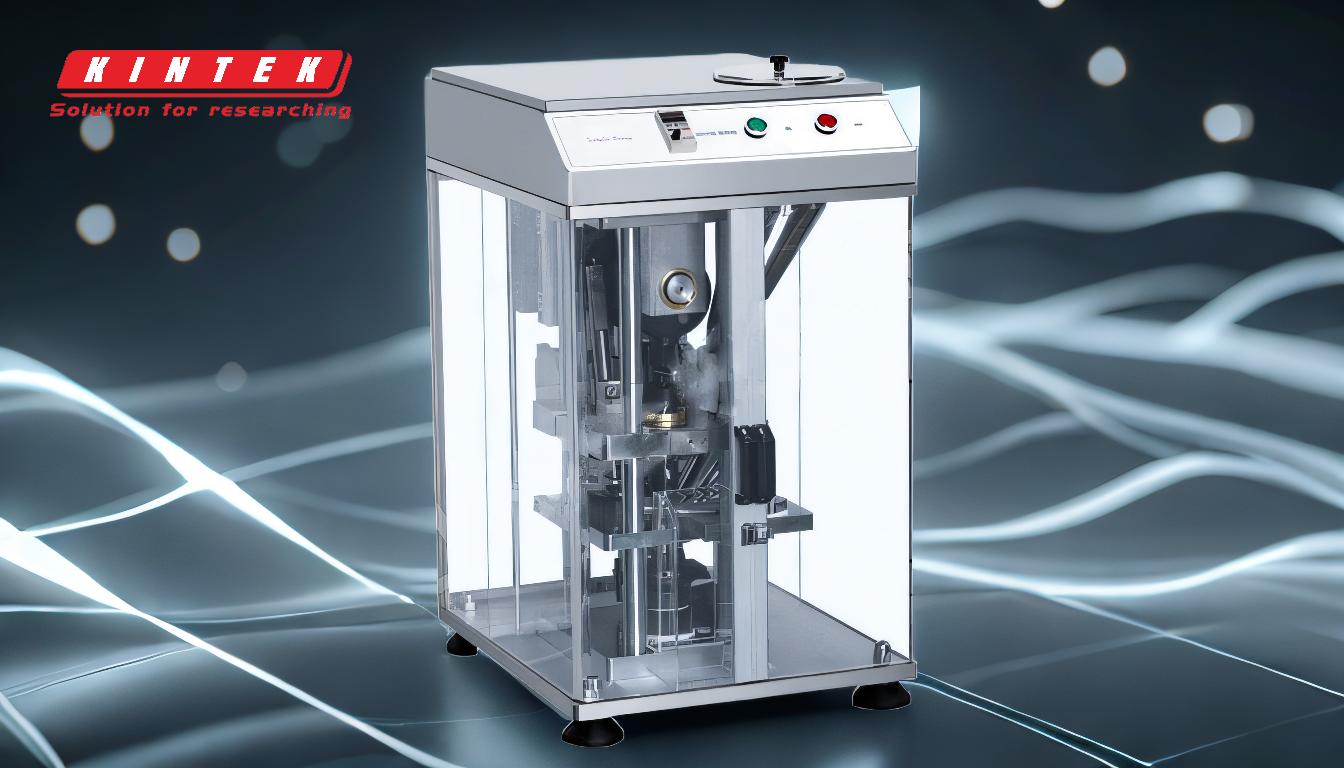
-
Purpose of Gold Coating in SEM:
- Gold coating is applied to non-conductive or poorly conductive samples to make them electrically conductive. This prevents charging effects, which can distort the SEM images.
- It also enhances secondary electron emission, improving image quality and contrast.
-
Typical Thickness Range:
- The gold coating thickness for SEM typically ranges from 5 to 20 nanometers (nm).
- 5-10 nm: Used for high-resolution imaging where fine surface details need to be preserved.
- 10-20 nm: Suitable for less conductive or rough samples to ensure sufficient conductivity.
-
Factors Influencing Coating Thickness:
- Sample Conductivity: Non-conductive samples require thicker coatings to ensure conductivity.
- Surface Roughness: Rough surfaces may need thicker coatings to cover irregularities.
- Resolution Requirements: High-resolution imaging demands thinner coatings to avoid obscuring fine details.
- SEM Instrument Specifications: Different SEM instruments may have specific requirements for coating thickness.
-
Coating Process:
- Gold coating is typically applied using a sputter coater, which uses a plasma to deposit a thin, uniform layer of gold onto the sample surface.
- The process is controlled to achieve the desired thickness, ensuring even coverage across the sample.
-
Advantages of Gold Coating:
- Conductivity: Prevents charging effects and ensures stable imaging.
- Enhanced Imaging: Improves secondary electron emission, leading to better image quality.
- Durability: Gold is resistant to oxidation, making it suitable for long-term sample storage.
-
Alternatives to Gold Coating:
- Other conductive materials like platinum, palladium, or carbon can be used depending on the application.
- Carbon coating is often used for energy-dispersive X-ray spectroscopy (EDS) analysis, as it does not interfere with elemental detection.
-
Practical Considerations:
- Over-coating can obscure fine details, while under-coating may lead to charging effects.
- The optimal thickness should be determined experimentally based on the sample and imaging requirements.
By carefully controlling the gold coating thickness, SEM users can achieve high-quality images while preserving the integrity of the sample surface.
Summary Table:
Aspect | Details |
---|---|
Purpose | Ensures conductivity, prevents charging, and enhances image quality. |
Thickness Range | 5-20 nm (5-10 nm for high-res imaging, 10-20 nm for less conductive samples). |
Factors to Consider | Sample conductivity, surface roughness, resolution, and SEM specifications. |
Coating Process | Applied via sputter coater for uniform, controlled thickness. |
Advantages | Prevents charging, improves imaging, and offers durability. |
Alternatives | Platinum, palladium, or carbon coatings for specific applications. |
Need help determining the right gold coating thickness for your SEM samples? Contact our experts today!