Powder metallurgy and sintering are related but not the same. Powder metallurgy is a broader manufacturing process that involves creating metal parts from powdered materials, while sintering is a specific step within that process. Powder metallurgy includes steps like powder mixing, compaction, and sintering, where sintering is the thermal treatment that bonds the metal particles together without melting them. Sintering imparts strength, density, and structural integrity to the compacted powder, making it a critical step in powder metallurgy. However, powder metallurgy encompasses more than just sintering, as it involves the entire process of transforming powdered metal into a finished product.
Key Points Explained:
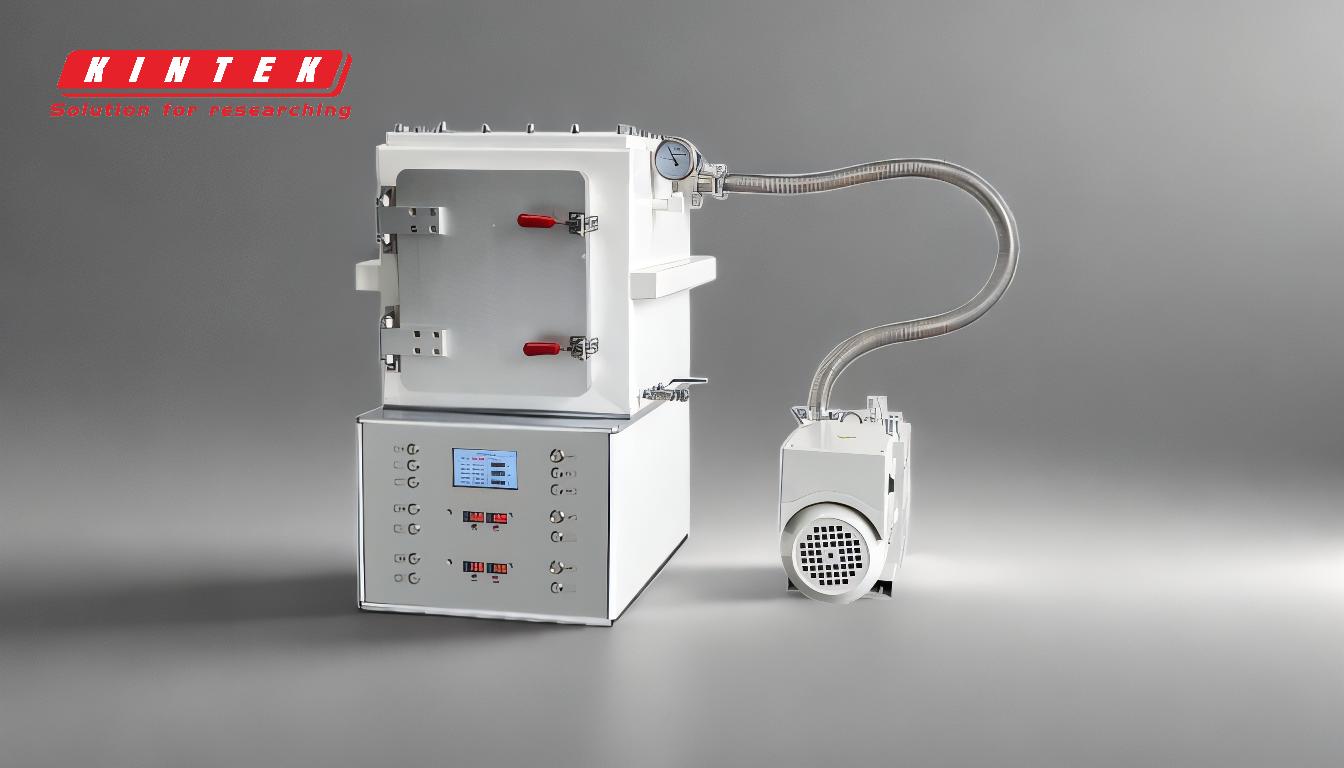
-
Definition of Powder Metallurgy:
- Powder metallurgy is a manufacturing process that involves producing metal parts from powdered materials. It includes several stages such as powder production, mixing, compaction, and sintering. The process is widely used for creating complex shapes with high precision and minimal waste.
-
Definition of Sintering:
- Sintering is a thermal process used in powder metallurgy where compacted metal powders are heated to a temperature just below their melting point. This heating causes the particles to bond together, resulting in a solid, dense, and strong component. Sintering is essential for imparting structural integrity to the compacted powder.
-
Relationship Between Powder Metallurgy and Sintering:
- Sintering is a critical step within the powder metallurgy process. While powder metallurgy encompasses the entire process of creating metal parts from powders, sintering specifically refers to the heat treatment that bonds the particles together. Without sintering, the compacted powder would lack the necessary strength and density for practical use.
-
Purpose of Sintering in Powder Metallurgy:
- The primary purpose of sintering is to fuse the metal particles together, enhancing the mechanical properties of the final product. It increases the density, strength, and durability of the compacted powder, making it suitable for use as a functional component. Sintering also helps in achieving the desired shape and dimensions of the part.
-
Temperature and Conditions for Sintering:
- Sintering is carried out at temperatures slightly below the melting point of the metal powder. This ensures that the particles bond together without completely melting, preserving the material's properties. The controlled heating environment prevents defects and ensures uniform bonding throughout the part.
-
Applications of Powder Metallurgy and Sintering:
- Powder metallurgy, including sintering, is used in various industries to produce components such as gears, bearings, filters, and structural parts. The process is valued for its ability to create complex shapes with high precision and minimal material waste. Sintering, in particular, is crucial for ensuring the final product meets the required mechanical and structural standards.
In summary, while sintering is a vital part of the powder metallurgy process, powder metallurgy itself is a broader term that includes multiple steps leading to the creation of metal parts. Sintering specifically refers to the thermal treatment that bonds the metal particles, giving the final product its strength and integrity.
Summary Table:
Aspect | Powder Metallurgy | Sintering |
---|---|---|
Definition | A manufacturing process creating metal parts from powdered materials. | A thermal process bonding metal particles without melting. |
Scope | Includes steps like powder mixing, compaction, and sintering. | A specific step within powder metallurgy. |
Purpose | Transforms powdered metal into a finished product. | Fuses metal particles to enhance strength, density, and structural integrity. |
Key Applications | Gears, bearings, filters, and structural parts. | Critical for achieving final product properties in powder metallurgy. |
Temperature | N/A | Slightly below the melting point of the metal powder. |
Want to learn more about powder metallurgy and sintering? Contact our experts today for tailored solutions!