PVD (Physical Vapor Deposition) coatings are generally safe once applied, as the particles are firmly bonded to the substrate and do not become airborne. However, during the application process, inhaling the particles can be harmful, necessitating proper safety measures such as ventilation and protective equipment. Once the coating is applied, it is chemically inert, durable, and poses no risk of toxicity or inhalation. PVD coatings are widely used in industries like automotive, aerospace, and medical due to their high hardness, wear resistance, and corrosion resistance. Additionally, many PVD coatings are food-safe, making them suitable for applications in the cutlery and kitchen equipment industries.
Key Points Explained:
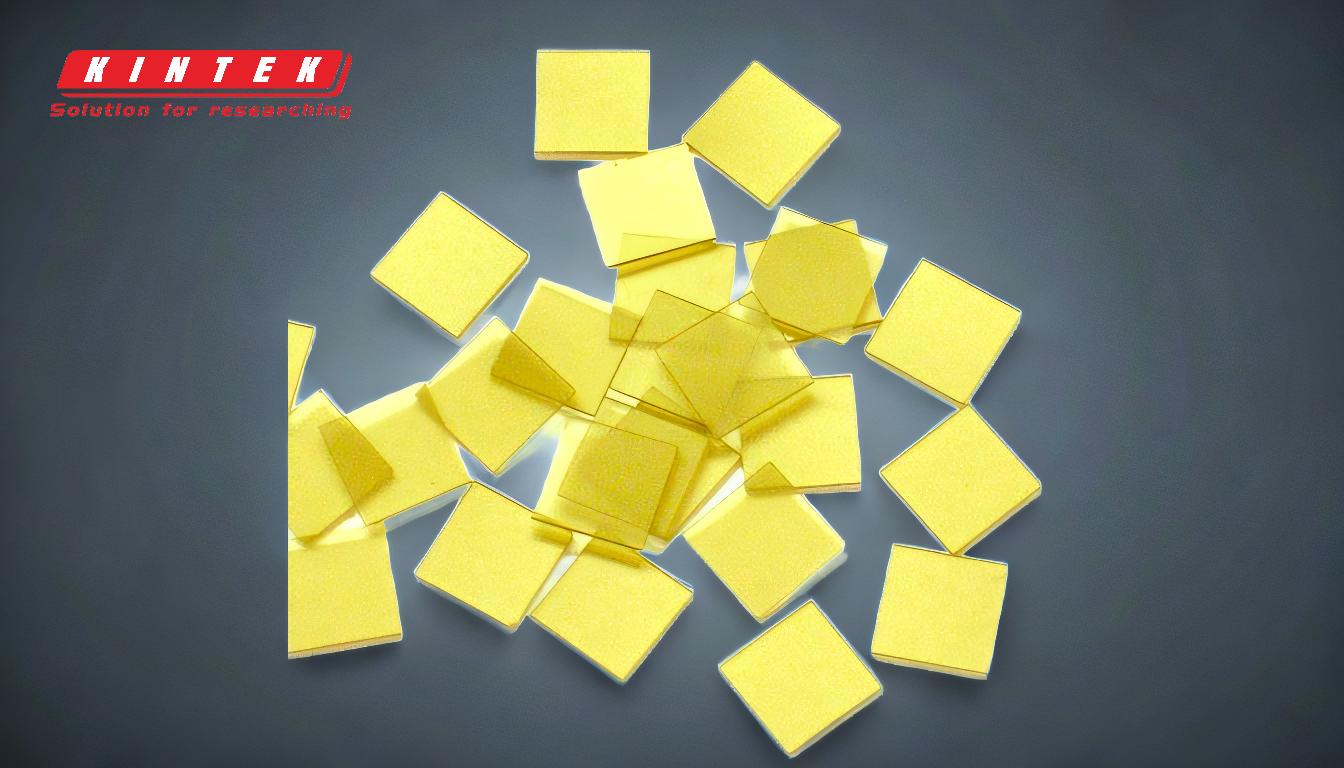
-
Safety of PVD Coatings Once Applied:
- PVD coatings are non-toxic and safe once applied because the particles are firmly bonded to the substrate and do not become airborne.
- The coatings are chemically and biologically inert, meaning they do not react with other substances or pose health risks in their final form.
- This makes them suitable for use in sensitive industries such as medical devices and food processing equipment.
-
Potential Hazards During Application:
- During the PVD coating process, particles can become airborne, and inhaling them can be harmful.
- Proper safety precautions, such as adequate ventilation, protective equipment (e.g., masks, gloves), and controlled environments, are essential to minimize exposure to these particles.
- Once the coating process is complete, the risk of exposure is eliminated.
-
Properties That Make PVD Coatings Safe:
- PVD coatings are extremely thin, typically ranging from 0.5 to 5 microns, and are firmly adhered to the substrate, making them difficult to remove.
- Their thinness and strong adhesion ensure that they do not flake or release particles, which contributes to their safety in various applications.
- The coatings replicate the original finish of materials with minimal effort, maintaining their integrity over time.
-
Industries and Applications Where PVD Coatings Are Used:
- PVD coatings are widely used in industries such as automotive, aerospace, and medical due to their high hardness, wear resistance, and corrosion resistance.
- In the food industry, PVD coatings are considered food-safe and are used in cutlery and commercial kitchen equipment because of their durability and inert properties.
- Their ability to enhance the aesthetic appearance of products also makes them popular in decorative applications.
-
Key Properties of PVD Coatings:
- High Hardness: PVD coatings are known for their exceptional hardness, which improves wear resistance and extends the lifespan of coated components.
- Corrosion and Oxidation Resistance: These coatings provide excellent protection against environmental factors, making them ideal for use in harsh conditions.
- Low Friction: The reduced friction properties of PVD coatings make them suitable for applications where smooth operation is critical.
- Aesthetic Appeal: PVD coatings can enhance the visual appearance of products, offering a variety of finishes and colors.
-
Food Safety and PVD Coatings:
- Many PVD coatings are food-safe, as they adhere strongly to their substrate and do not react with food or beverages.
- This makes them ideal for use in kitchen equipment, cutlery, and other food-related applications where durability and safety are paramount.
- The wear-resistant properties of PVD coatings ensure that they maintain their integrity even under frequent use and cleaning.
In conclusion, PVD coatings are safe and non-toxic once applied, but precautions must be taken during the application process to avoid exposure to airborne particles. Their exceptional properties, including hardness, wear resistance, and corrosion resistance, make them valuable across various industries, including those requiring food-safe materials.
Summary Table:
Aspect | Details |
---|---|
Safety Once Applied | Non-toxic, chemically inert, and firmly bonded to the substrate. |
Hazards During Application | Airborne particles can be harmful; requires ventilation and protective gear. |
Key Properties | High hardness, wear resistance, corrosion resistance, and low friction. |
Industries | Automotive, aerospace, medical, and food processing. |
Food Safety | Food-safe, durable, and non-reactive with food or beverages. |
Interested in PVD coatings for your industry? Contact us today to learn more!