Pyrolysis can be costly, but the overall expense depends on several factors, including the type of pyrolysis reactor, the scale of operation, feedstock availability, and energy efficiency. Pyrolysis reactors are designed to operate as closed systems, relying on external heat sources to thermally decompose organic materials in the absence of oxygen. While the initial investment in equipment like a pyrolysis reactor can be high, the operational costs can vary based on energy consumption, maintenance, and the quality of the end products. The economic viability of pyrolysis often hinges on optimizing these factors to balance costs with potential revenue from byproducts like bio-oil, syngas, and biochar.
Key Points Explained:
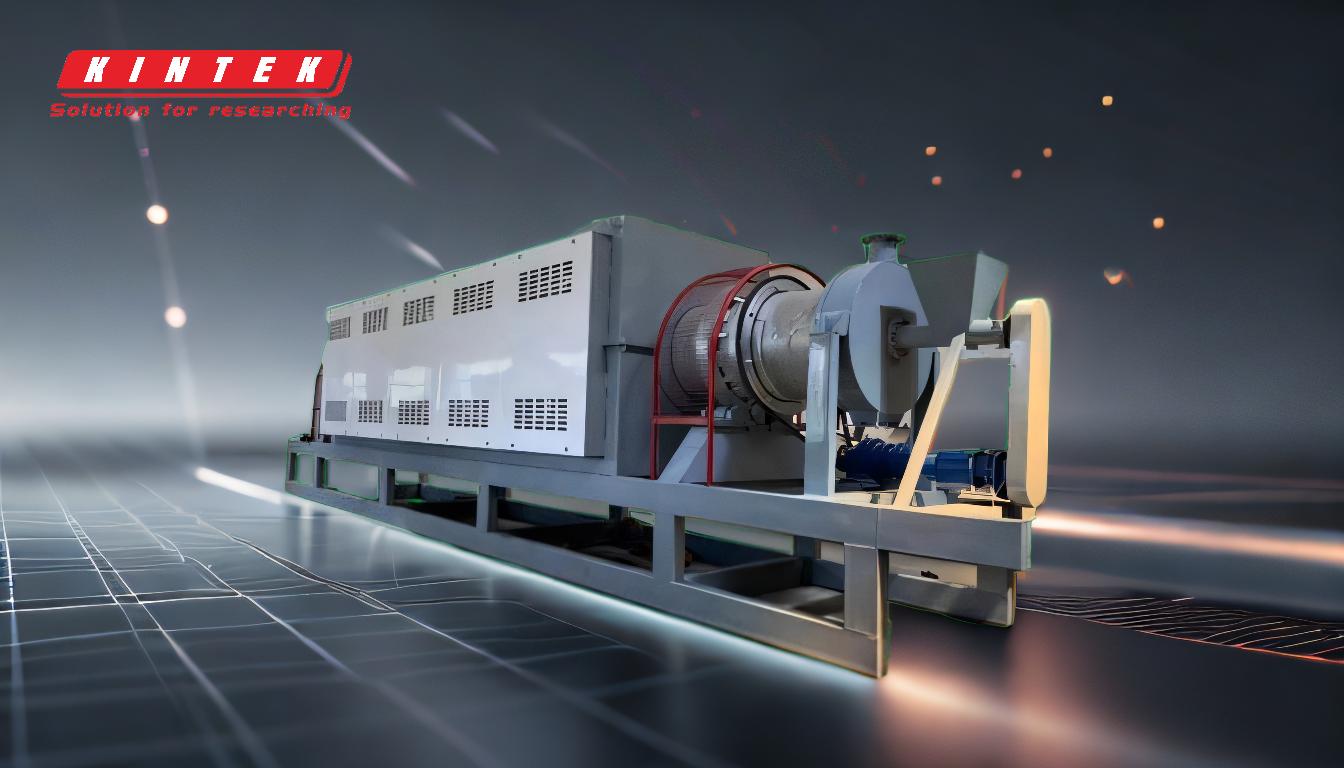
-
Dependence on External Heat Supply:
- Pyrolysis reactors require an external heat source to maintain the high temperatures needed for thermal decomposition. This heat is often supplied through electricity, natural gas, or other fuels, which can contribute significantly to operational costs. The choice of heat source and its efficiency directly impacts the overall cost of the process.
-
Closed System Operation:
- Pyrolysis reactors operate as closed systems to ensure an oxygen-free environment, which is critical for preventing combustion and achieving the desired chemical reactions. This design minimizes emissions but may require advanced engineering and materials, increasing both initial and maintenance costs.
-
Thermodynamic Principles:
- The process relies on thermodynamic principles to break down complex organic molecules into simpler compounds like bio-oil, syngas, and biochar. Optimizing these reactions for maximum yield and energy efficiency is essential to reduce costs and improve profitability.
-
Initial Investment:
- The cost of purchasing and installing a pyrolysis reactor can be substantial, especially for large-scale operations. Factors such as reactor size, material quality, and technological complexity influence the upfront investment.
-
Operational Costs:
- Beyond the initial investment, ongoing expenses include energy consumption, labor, maintenance, and feedstock procurement. Efficiently managing these costs is crucial for the long-term economic sustainability of pyrolysis projects.
-
Feedstock Availability and Cost:
- The type and availability of feedstock significantly affect the cost of pyrolysis. Using waste materials or agricultural residues can reduce feedstock costs, while specialized or high-quality feedstocks may increase expenses.
-
Byproduct Revenue:
- The economic viability of pyrolysis often depends on the market value of its byproducts. High-quality bio-oil, syngas, and biochar can generate revenue, offsetting operational costs and improving overall profitability.
-
Scale of Operation:
- Larger-scale pyrolysis plants may benefit from economies of scale, reducing per-unit costs. However, scaling up also requires more significant capital investment and operational expertise.
-
Energy Efficiency:
- Improving the energy efficiency of pyrolysis reactors can lower operational costs. Innovations in reactor design, heat recovery systems, and process optimization play a critical role in achieving this goal.
-
Environmental and Regulatory Considerations:
- Compliance with environmental regulations may add to the cost of pyrolysis operations. However, the process's ability to convert waste into valuable products can also provide environmental benefits and potential incentives.
By carefully considering these factors, stakeholders can assess whether pyrolysis is a cost-effective solution for their specific needs and explore strategies to optimize the process for better economic outcomes.
Summary Table:
Factor | Impact on Cost |
---|---|
External Heat Supply | High energy consumption increases operational costs. |
Closed System Operation | Advanced engineering and materials raise initial and maintenance costs. |
Initial Investment | High upfront costs for reactor purchase and installation. |
Operational Costs | Includes energy, labor, maintenance, and feedstock procurement. |
Feedstock Availability | Waste materials reduce costs; specialized feedstocks increase expenses. |
Byproduct Revenue | High-quality bio-oil, syngas, and biochar can offset costs. |
Scale of Operation | Larger scales reduce per-unit costs but require higher capital investment. |
Energy Efficiency | Improved efficiency lowers operational costs. |
Environmental Compliance | Regulatory compliance may add costs but offers environmental benefits. |
Want to optimize your pyrolysis process for cost-efficiency? Contact our experts today for tailored solutions!