Silicon carbide (SiC) is a highly durable and hard material, making it challenging to machine compared to softer materials like metals or plastics. Its exceptional hardness, which is close to that of diamond, and its brittleness make conventional machining methods difficult. However, with advanced techniques such as diamond grinding, laser machining, or electrical discharge machining (EDM), it is possible to achieve precise results. The choice of machining method depends on the desired precision, surface finish, and application requirements. While silicon carbide is not easy to machine, its unique properties, such as high thermal conductivity, chemical resistance, and mechanical strength, make it invaluable in demanding applications like aerospace, electronics, and industrial manufacturing.
Key Points Explained:
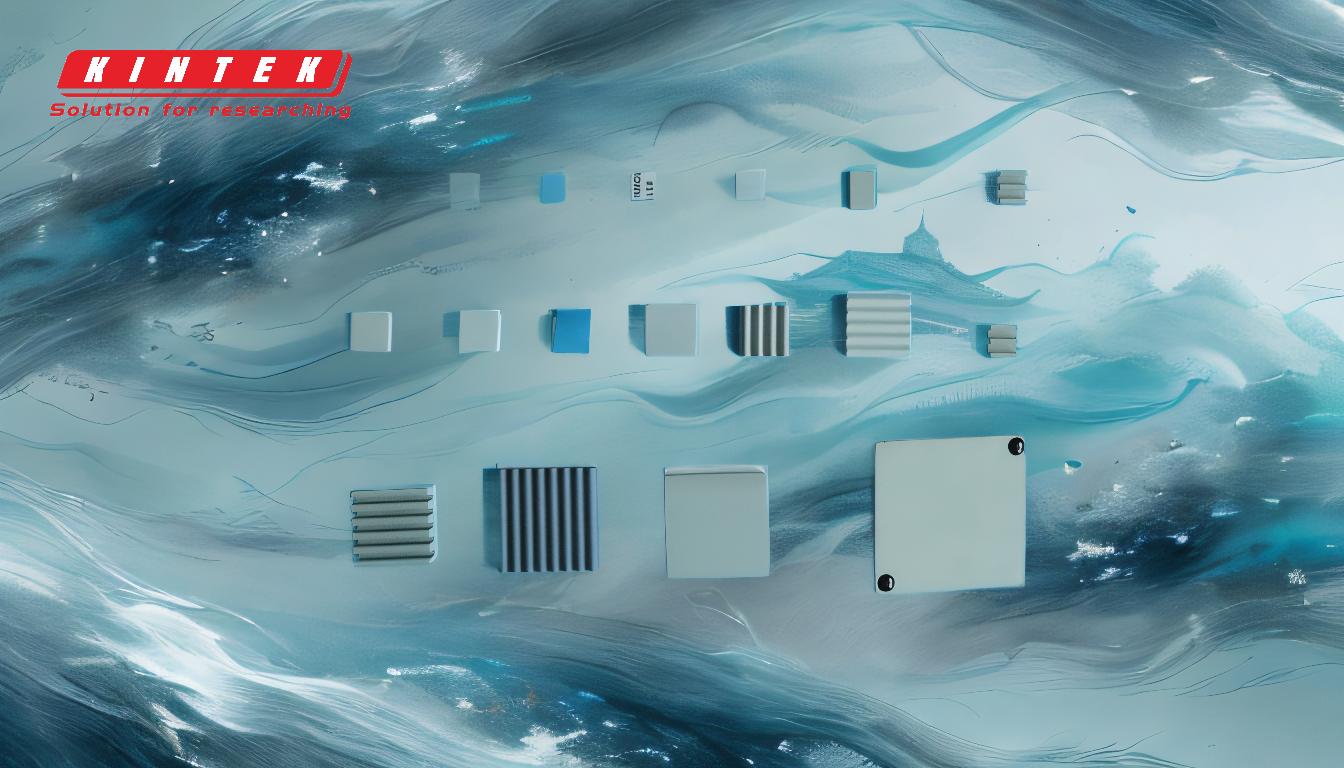
-
Exceptional Hardness and Brittleness:
- Silicon carbide ceramic is one of the hardest materials known, with a hardness close to that of diamond. This makes it resistant to wear and abrasion but also challenging to machine using conventional tools.
- Its brittleness further complicates machining, as it can crack or chip under stress if not handled properly.
-
Challenges in Conventional Machining:
- Traditional machining methods like turning, milling, or drilling are ineffective for silicon carbide due to its hardness. Standard cutting tools wear out quickly and fail to produce precise results.
- The material's brittleness also limits the use of high-speed machining, as it can lead to fractures or surface defects.
-
Advanced Machining Techniques:
- Diamond Grinding: Diamond tools are often used for grinding silicon carbide because diamond is one of the few materials harder than SiC. This method allows for precise shaping and finishing.
- Laser Machining: Lasers can be used to cut or engrave silicon carbide with high precision, minimizing the risk of cracking or chipping.
- Electrical Discharge Machining (EDM): EDM is effective for machining complex shapes in silicon carbide, as it uses electrical discharges to remove material without direct contact.
-
Surface Finish and Precision:
- Achieving a smooth surface finish on silicon carbide requires specialized techniques and tools. Diamond grinding and polishing are commonly used to achieve the desired surface quality.
- Precision machining is critical for applications like semiconductor manufacturing, where even minor imperfections can affect performance.
-
Applications and Trade-offs:
- Despite the challenges, silicon carbide is widely used in industries such as aerospace, electronics, and automotive due to its exceptional properties, including high thermal conductivity, chemical resistance, and mechanical strength.
- The difficulty in machining is often outweighed by the material's performance benefits in high-temperature, high-stress, or corrosive environments.
-
Cost Considerations:
- Machining silicon carbide is expensive due to the need for specialized tools and techniques. However, the long-term benefits, such as reduced wear and extended component life, often justify the higher initial costs.
In conclusion, while silicon carbide is not easy to machine, its unique properties make it indispensable for demanding applications. Advanced machining techniques and careful handling are required to overcome its challenges and fully leverage its benefits.
Summary Table:
Aspect | Details |
---|---|
Hardness | Close to diamond, making it resistant to wear but difficult to machine. |
Brittleness | Prone to cracking or chipping under stress. |
Challenges | Conventional tools wear out quickly; high-speed machining risks fractures. |
Advanced Techniques | Diamond grinding, laser machining, and EDM for precision and minimal damage. |
Applications | Aerospace, electronics, automotive, and industrial manufacturing. |
Cost | Expensive due to specialized tools, but long-term benefits justify costs. |
Need help machining silicon carbide? Contact our experts today for tailored solutions!