Sputtering is not a form of Chemical Vapor Deposition (CVD). While both sputtering and CVD are used for thin film deposition, they operate on fundamentally different principles. Sputtering is a Physical Vapor Deposition (PVD) technique that relies on physical processes, such as the ejection of atoms from a target material due to bombardment by high-energy ions. In contrast, CVD involves chemical reactions in the gas phase to deposit thin films on a substrate. This distinction is critical because it affects the types of materials that can be deposited, the quality of the films, and the specific applications for which each method is suited. Below, we explore the key differences and characteristics of sputtering and CVD to clarify why sputtering is not considered a CVD process.
Key Points Explained:
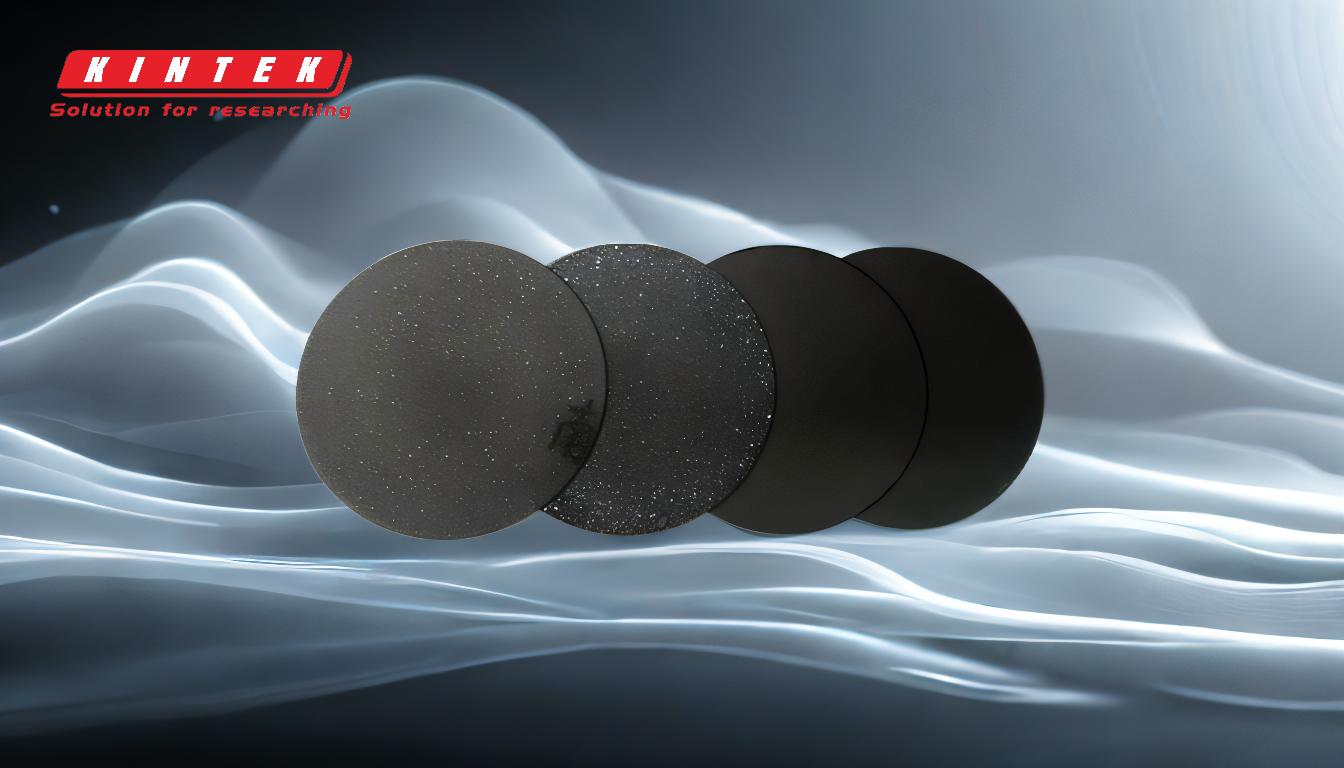
-
Fundamental Mechanism:
- Sputtering (PVD): Sputtering is a physical process where high-energy ions (usually argon) bombard a target material, causing atoms to be ejected from the target and deposited onto a substrate. This process does not involve chemical reactions; it is purely a physical transfer of material.
- CVD: CVD relies on chemical reactions in the gas phase. Precursor gases are introduced into a reactor, where they undergo thermal decomposition or react with other gases to form a solid film on the substrate. This chemical transformation is a defining feature of CVD.
-
Material Source:
- Sputtering: The material for deposition comes from a solid target. The target is physically sputtered, and the ejected atoms travel to the substrate.
- CVD: The material for deposition originates from gaseous precursors. These precursors react chemically to form the desired film on the substrate.
-
Deposition Environment:
- Sputtering: Typically performed in a vacuum environment to ensure that the sputtered atoms travel unimpeded to the substrate.
- CVD: Can be performed at atmospheric pressure, low pressure, or in a vacuum, depending on the specific type of CVD process (e.g., APCVD, LPCVD, PECVD).
-
Film Characteristics:
- Sputtering: Produces films with excellent adhesion and uniformity. It is particularly useful for depositing metals, alloys, and some compounds. However, it may struggle with conformal coverage on complex geometries.
- CVD: Known for producing high-purity, dense films with excellent conformality, making it ideal for coating complex-shaped surfaces. CVD is also capable of depositing a wide range of materials, including metals, ceramics, and semiconductors.
-
Temperature Requirements:
- Sputtering: Generally operates at lower temperatures compared to CVD, making it suitable for temperature-sensitive substrates.
- CVD: Often requires high temperatures (e.g., 850-1100°C) to drive the chemical reactions, although plasma-enhanced CVD (PECVD) and other variants can reduce the temperature requirements.
-
Applications:
- Sputtering: Commonly used in applications such as semiconductor manufacturing, optical coatings, and decorative coatings.
- CVD: Widely used in the production of semiconductor devices, protective coatings, and advanced materials like graphene and carbon nanotubes.
-
Equipment and Process Complexity:
- Sputtering: Equipment is relatively simple, with a focus on maintaining a vacuum and controlling the ion bombardment process.
- CVD: Equipment is more complex due to the need to handle reactive gases, control chemical reactions, and often manage higher temperatures.
-
Material Versatility:
- Sputtering: Limited by the availability of suitable target materials and the physical properties of the sputtered atoms.
- CVD: Offers greater versatility in terms of the types of materials that can be deposited, including multi-component alloys and complex compounds.
In summary, sputtering and CVD are distinct thin film deposition techniques with different mechanisms, material sources, and applications. Sputtering is a PVD process that relies on physical atom transfer, while CVD is a chemical process involving gas-phase reactions. Understanding these differences is crucial for selecting the appropriate method for specific applications in industries such as electronics, optics, and materials science.
Summary Table:
Aspect | Sputtering (PVD) | CVD |
---|---|---|
Fundamental Mechanism | Physical process: atoms ejected from a target by ion bombardment | Chemical process: gas-phase reactions form a solid film |
Material Source | Solid target | Gaseous precursors |
Deposition Environment | Vacuum environment | Atmospheric, low pressure, or vacuum |
Film Characteristics | Excellent adhesion, uniformity; struggles with complex geometries | High purity, dense films; excellent conformality |
Temperature | Lower temperatures, suitable for sensitive substrates | High temperatures (850-1100°C); PECVD reduces temperature |
Applications | Semiconductor manufacturing, optical coatings, decorative coatings | Semiconductor devices, protective coatings, graphene, carbon nanotubes |
Equipment Complexity | Relatively simple; focuses on vacuum and ion bombardment | More complex; handles reactive gases, chemical reactions, and high temperatures |
Material Versatility | Limited by target material availability | Greater versatility; deposits multi-component alloys and complex compounds |
Need help choosing the right thin film deposition method? Contact our experts today!