Sputtering is a Physical Vapor Deposition (PVD) process, not a Chemical Vapor Deposition (CVD) process. It is a dry, low-temperature method that involves the use of a plasma to dislodge atoms from a target material, which then deposit onto a substrate to form a thin film. Unlike CVD, which relies on chemical reactions to deposit material, sputtering is purely physical, involving the transfer of energy from ions to the target material to eject atoms. This makes it a versatile and widely used technique in industries requiring precise thin-film coatings.
Key Points Explained:
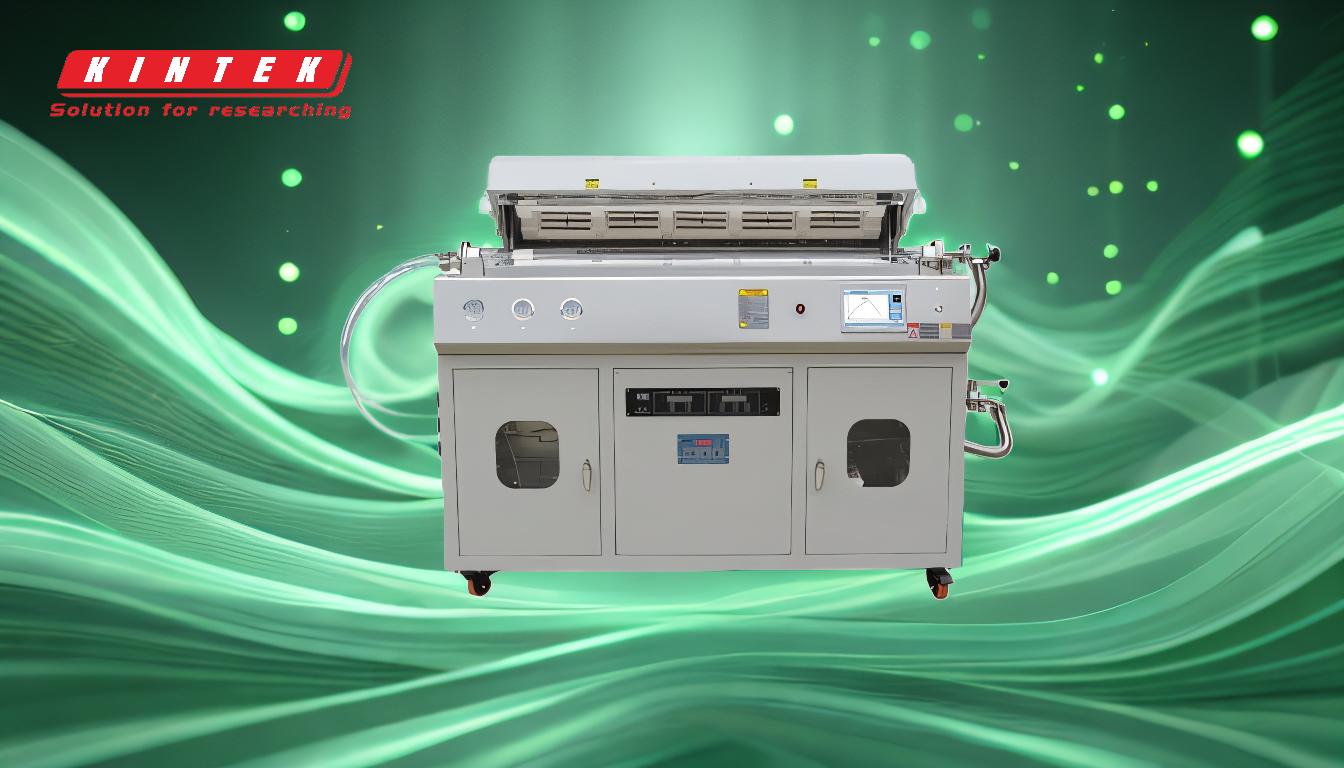
-
Definition of Sputtering:
- Sputtering is a thin-film deposition process where atoms are ejected from a solid target material due to bombardment by energetic ions, typically from a plasma. These ejected atoms then deposit onto a substrate to form a thin film.
- It is a purely physical process, relying on kinetic energy transfer rather than chemical reactions.
-
Sputtering as a PVD Process:
- Sputtering is classified under Physical Vapor Deposition (PVD) because it involves the physical transfer of material from a target to a substrate without the use of chemical reactions.
- In PVD processes, the material is vaporized in a vacuum environment and then deposited onto the substrate. Sputtering achieves this by using a plasma to dislodge atoms from the target.
-
Comparison to CVD:
- Chemical Vapor Deposition (CVD) involves chemical reactions between gaseous precursors to form a solid film on a substrate. This process typically requires higher temperatures and involves complex chemical interactions.
- In contrast, sputtering is a low-temperature process that relies on physical mechanisms, making it suitable for temperature-sensitive substrates.
-
Mechanism of Sputtering:
- A controlled gas, usually argon, is introduced into a vacuum chamber. A cathode (target material) is electrically energized to generate a plasma.
- The gas atoms become positively charged ions, which are accelerated toward the target material. Upon impact, these ions dislodge atoms from the target, creating a vapor stream.
- The dislodged atoms then travel through the vacuum chamber and deposit onto the substrate, forming a thin film.
-
Applications of Sputtering:
- Sputtering is widely used in industries such as semiconductor manufacturing, optics, and decorative coatings due to its ability to produce high-quality, uniform thin films.
- It is also used in the production of hard coatings for tools, anti-reflective coatings for glass, and conductive layers for electronic devices.
-
Advantages of Sputtering:
- Low-temperature process: Suitable for substrates that cannot withstand high temperatures.
- High precision: Allows for the deposition of very thin and uniform films.
- Versatility: Can deposit a wide range of materials, including metals, alloys, and ceramics.
-
Historical Context:
- Sputtering has been known since the 1850s and was notably used by Thomas Edison in 1904 to apply thin metal layers to wax phonograph recordings.
- Over time, the process has evolved and is now a cornerstone of modern thin-film deposition technologies.
In summary, sputtering is a PVD process that distinguishes itself from CVD by its reliance on physical mechanisms rather than chemical reactions. Its low-temperature operation, precision, and versatility make it a preferred method for many industrial applications.
Summary Table:
Aspect | Sputtering (PVD) | CVD |
---|---|---|
Process Type | Physical Vapor Deposition (PVD) | Chemical Vapor Deposition (CVD) |
Mechanism | Physical transfer of material via ion bombardment | Chemical reactions between gaseous precursors |
Temperature | Low-temperature process | High-temperature process |
Applications | Semiconductor manufacturing, optics, decorative coatings, hard coatings, electronics | High-temperature coatings, complex chemical films |
Advantages | Suitable for temperature-sensitive substrates, high precision, versatile material use | High-quality films for high-temperature applications, complex chemical interactions |
Interested in how sputtering can enhance your thin-film processes? Contact our experts today to learn more!