Sputtering is a Physical Vapor Deposition (PVD) technique, not a Chemical Vapor Deposition (CVD) process. PVD involves the physical transfer of material from a solid source to a substrate in a vacuum environment, typically through processes like evaporation or sputtering. In contrast, CVD relies on chemical reactions between gaseous precursors to form a solid coating on the substrate. Sputtering specifically involves bombarding a target material with high-energy ions to eject atoms, which then deposit onto a substrate. This process is entirely physical, as it does not involve chemical reactions, making it distinct from CVD.
Key Points Explained:
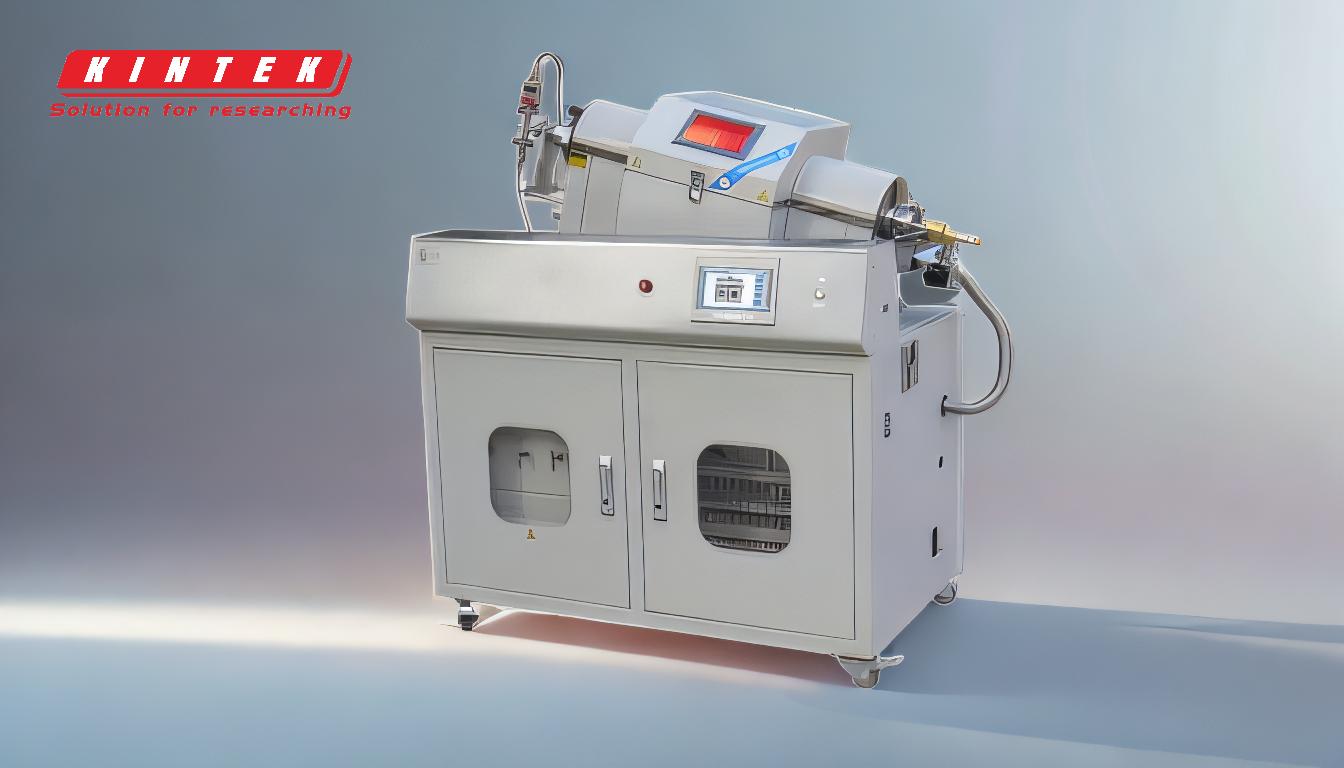
-
Definition of PVD and CVD:
- PVD (Physical Vapor Deposition): A process where material is physically transferred from a solid source to a substrate in a vacuum environment. Techniques include evaporation and sputtering.
- CVD (Chemical Vapor Deposition): A process where chemical reactions between gaseous precursors form a solid coating on a substrate. Heat or plasma drives the reaction.
-
Sputtering as a PVD Technique:
- Sputtering is a PVD method where a target material is bombarded with high-energy ions (usually from a plasma discharge) to eject atoms. These atoms then deposit onto a substrate to form a thin film.
- The process is entirely physical, involving no chemical reactions, which distinguishes it from CVD.
-
How Sputtering Works:
- A vacuum chamber is used to create a low-pressure environment.
- A plasma discharge is generated, and ions from the plasma bombard the target material.
- Atoms are ejected from the target and travel to the substrate, where they condense to form a thin film.
- This process is controlled by magnetic fields to direct the plasma and optimize deposition.
-
Key Differences Between PVD and CVD:
- Material Source: PVD uses solid materials (e.g., metals, alloys), while CVD uses gaseous precursors.
- Process Mechanism: PVD relies on physical processes like sputtering or evaporation, while CVD involves chemical reactions.
- Deposition Environment: Both processes occur in vacuum or low-pressure environments, but CVD often requires higher temperatures to drive chemical reactions.
-
Advantages of Sputtering (PVD):
- High-quality, uniform coatings with excellent adhesion.
- Ability to deposit a wide range of materials, including metals, alloys, and ceramics.
- Suitable for temperature-sensitive substrates, as it typically operates at lower temperatures compared to CVD.
-
Applications of Sputtering:
- Used in industries like semiconductors, optics, and decorative coatings.
- Common in manufacturing thin films for microelectronics, solar panels, and anti-reflective coatings.
-
Why Sputtering is Not CVD:
- Sputtering does not involve chemical reactions between precursors.
- It relies on physical bombardment and deposition, making it a subset of PVD.
In conclusion, sputtering is a PVD technique because it involves the physical transfer of material without chemical reactions, distinguishing it from CVD. This makes it ideal for applications requiring precise, high-quality thin films.
Summary Table:
Aspect | PVD (Sputtering) | CVD |
---|---|---|
Material Source | Solid materials (e.g., metals, alloys) | Gaseous precursors |
Process Mechanism | Physical processes (e.g., sputtering, evaporation) | Chemical reactions between gases |
Deposition Environment | Vacuum or low-pressure environment | Vacuum or low-pressure, often with higher temperatures |
Key Advantage | High-quality, uniform coatings with excellent adhesion | Suitable for complex chemical compositions |
Applications | Semiconductors, optics, decorative coatings, solar panels, anti-reflective coatings | Microelectronics, wear-resistant coatings, and specialized applications |
Need help choosing the right deposition technique for your project? Contact our experts today for personalized advice!