Yes, there is flux specifically designed for aluminum. Flux is used in aluminum welding, brazing, and soldering to remove oxides, improve wetting, and ensure a strong bond. Aluminum forms a stable oxide layer quickly when exposed to air, which can hinder the joining process. Fluxes for aluminum are formulated to break down this oxide layer and prevent re-oxidation during the heating process. They come in various forms, such as paste, liquid, or powder, and are tailored for specific applications like gas welding, furnace brazing, or torch brazing. Choosing the right flux depends on the method of joining, the type of aluminum alloy, and the desired outcome.
Key Points Explained:
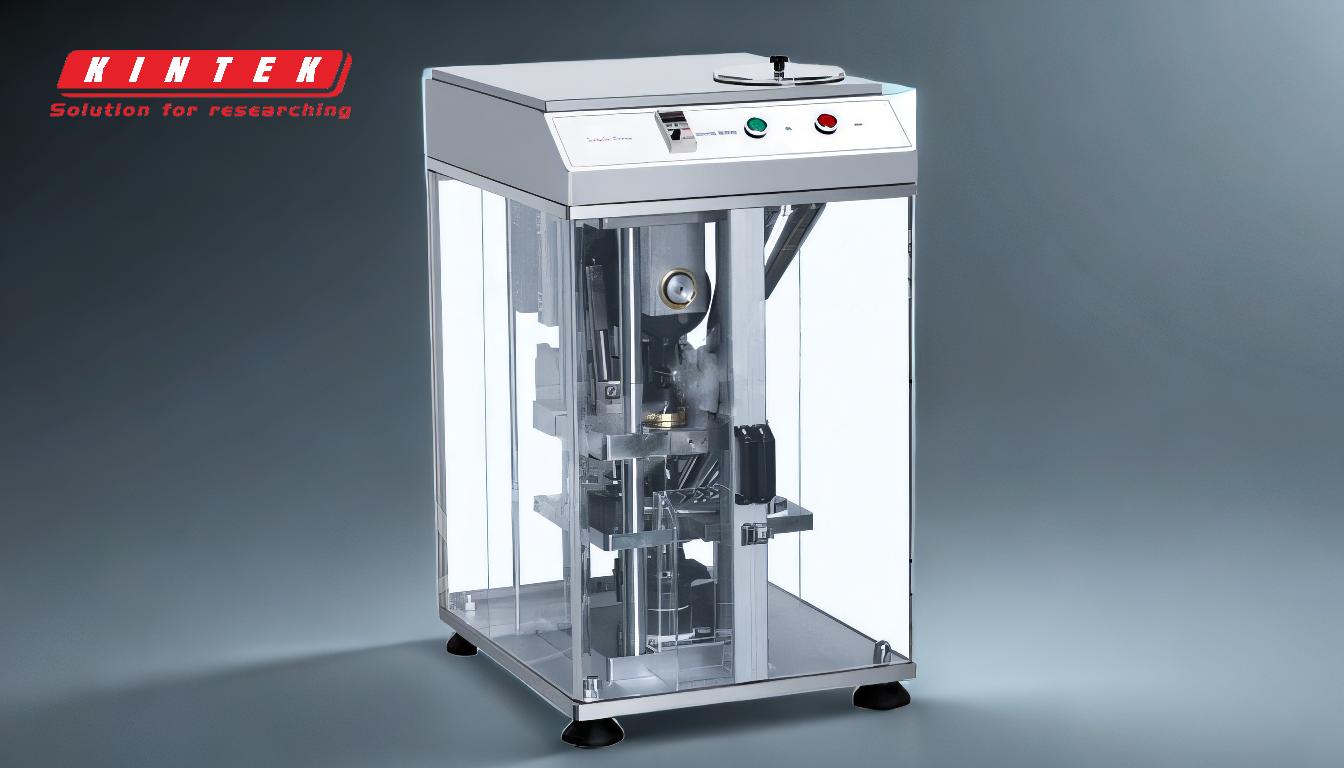
-
Purpose of Flux in Aluminum Joining:
- Aluminum naturally forms a thin, stable oxide layer when exposed to air. This layer can prevent proper bonding during welding, brazing, or soldering.
- Flux is used to dissolve or break down this oxide layer, allowing the filler metal to wet and bond with the base metal effectively.
- It also helps prevent re-oxidation during the heating process, ensuring a clean and strong joint.
-
Types of Flux for Aluminum:
- Paste Flux: Commonly used for torch brazing and welding. It is easy to apply and provides good coverage.
- Liquid Flux: Often used in dip brazing or furnace brazing. It can be applied by brushing or spraying.
- Powder Flux: Suitable for furnace brazing or when mixed with filler metals. It is often used in controlled environments.
- Each type is formulated for specific applications and methods, ensuring optimal performance.
-
Flux Composition:
- Aluminum fluxes typically contain chlorides and fluorides, which are effective in breaking down the oxide layer.
- Some fluxes also include additives to improve wetting and flow of the filler metal.
- The composition must be carefully selected to avoid corrosion or contamination of the aluminum surface after the joining process.
-
Application Methods:
- Torch Brazing/Welding: Flux is applied directly to the joint area before heating. It is often used with a filler rod coated with flux.
- Furnace Brazing: Flux is applied as a powder or liquid, and the parts are heated in a controlled environment. This method is ideal for complex or large-scale production.
- Dip Brazing: Parts are submerged in a bath of molten flux, ensuring complete coverage and oxide removal.
-
Considerations for Choosing Flux:
- Alloy Type: Different aluminum alloys may require specific flux formulations to achieve the best results.
- Joining Method: The flux must be compatible with the heating method (e.g., torch, furnace, or induction).
- Post-Joining Cleanup: Some fluxes leave residues that must be removed to prevent corrosion. Water-soluble fluxes are easier to clean.
-
Safety and Handling:
- Fluxes for aluminum often contain corrosive chemicals. Proper handling, including the use of gloves and eye protection, is essential.
- Ventilation is important when using fluxes, as some may release fumes during heating.
- Residues should be cleaned thoroughly after the joining process to avoid long-term damage to the aluminum.
-
Common Brands and Products:
- There are several reputable brands that produce aluminum fluxes, such as Harris, Lucas-Milhaupt, and Handy & Harman.
- Products are often labeled for specific applications, such as "aluminum brazing flux" or "aluminum welding flux," making it easier to choose the right one.
By understanding the role of flux in aluminum joining and selecting the appropriate type and application method, you can achieve strong, durable, and clean joints in your aluminum projects.
Summary Table:
Aspect | Details |
---|---|
Purpose | Removes oxides, improves wetting, and ensures strong bonds. |
Types | Paste, liquid, and powder fluxes. |
Composition | Chlorides, fluorides, and additives for better wetting and flow. |
Application Methods | Torch brazing, furnace brazing, and dip brazing. |
Key Considerations | Alloy type, joining method, and post-joining cleanup. |
Safety | Use gloves, eye protection, and ensure proper ventilation. |
Common Brands | Harris, Lucas-Milhaupt, and Handy & Harman. |
Need help selecting the right flux for your aluminum project? Contact our experts today!