Three-plate molds offer several significant advantages in injection molding, particularly in terms of flexibility, efficiency, and cost-effectiveness. These molds are designed with three plates that separate during the ejection process, allowing for more complex part designs and improved gating options. Key benefits include central gating, the ability to use multiple gates for single or multiple parts, and the potential to eliminate the need for costly hot runner systems. These features make three-plate molds a versatile and economical choice for many manufacturing scenarios.
Key Points Explained:
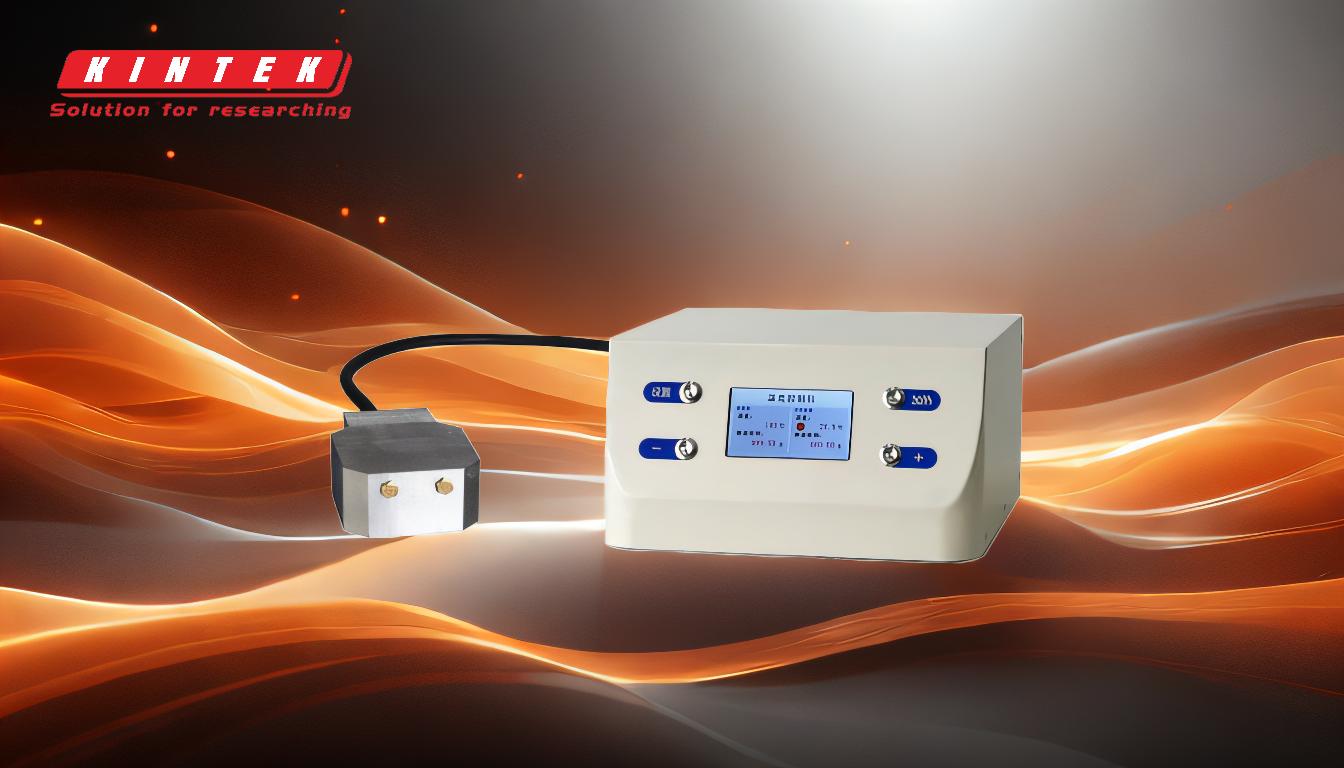
-
Central Gating:
- Explanation: Central gating refers to the placement of the gate at the center of the part. This is particularly beneficial for symmetrical parts or those requiring uniform filling.
-
Advantages:
- Ensures even distribution of the molten plastic, reducing the risk of warping or uneven shrinkage.
- Simplifies the mold design by centralizing the gate, which can lead to easier maintenance and lower production costs.
-
Multiple Gates Feeding a Single Part:
- Explanation: In some cases, a single part may require multiple gates to ensure proper filling and to avoid defects such as weld lines or air traps.
-
Advantages:
- Improves the quality of the final product by ensuring complete and uniform filling of the mold.
- Allows for the production of larger or more complex parts that might be difficult to fill with a single gate.
-
Multiple Gates Feeding Multiple Parts:
- Explanation: Three-plate molds can be designed to feed multiple parts simultaneously, each with its own gate.
-
Advantages:
- Increases production efficiency by allowing multiple parts to be molded in a single cycle.
- Reduces the overall cycle time, leading to higher throughput and lower per-part costs.
-
Multiple Gates Feeding Multiple Parts and Runners:
- Explanation: This configuration allows for multiple parts to be molded along with their runners in a single cycle, which can then be separated after ejection.
-
Advantages:
- Further enhances production efficiency by combining the molding of parts and runners.
- Reduces material waste and simplifies the post-molding process, as the runners can be easily separated from the parts.
-
Elimination of Hot Runner Systems:
- Explanation: Hot runner systems are used to keep the plastic in a molten state as it travels through the runners to the mold cavities. While effective, they are also expensive and complex.
-
Advantages:
- Reduces the overall cost of the mold by eliminating the need for a hot runner system.
- Simplifies the mold design and maintenance, as there are fewer components that can fail or require servicing.
-
Flexibility in Design:
- Explanation: Three-plate molds offer greater design flexibility compared to two-plate molds, allowing for more complex part geometries and gating options.
-
Advantages:
- Enables the production of parts with intricate designs or those requiring specific gating configurations.
- Provides more options for optimizing the mold design for specific production needs, leading to better overall performance.
-
Cost-Effectiveness:
- Explanation: By eliminating the need for hot runner systems and allowing for more efficient use of materials and production cycles, three-plate molds can be more cost-effective in the long run.
-
Advantages:
- Lowers the initial investment in mold design and construction.
- Reduces ongoing production costs through improved efficiency and reduced material waste.
In summary, three-plate molds offer a range of advantages that make them an attractive option for many injection molding applications. Their ability to support central gating, multiple gates, and the elimination of hot runner systems, combined with their design flexibility and cost-effectiveness, make them a versatile and economical choice for producing high-quality plastic parts.
Summary Table:
Feature | Advantages |
---|---|
Central Gating | Ensures even distribution, reduces warping, simplifies mold design |
Multiple Gates for Single Part | Improves product quality, enables complex part production |
Multiple Gates for Multiple Parts | Increases efficiency, reduces cycle time, lowers per-part costs |
Multiple Gates with Runners | Enhances efficiency, reduces material waste, simplifies post-molding process |
Elimination of Hot Runner Systems | Reduces mold cost, simplifies design and maintenance |
Design Flexibility | Enables intricate designs, optimizes mold performance |
Cost-Effectiveness | Lowers initial investment, reduces ongoing production costs |
Ready to optimize your injection molding process? Contact us today to learn more about three-plate molds!