Three-plate molds offer several advantages over two-plate molds in injection molding, particularly in terms of flexibility, efficiency, and cost-effectiveness. They allow for central gating, multiple gates feeding a single part, or multiple gates feeding multiple parts, which can enhance part quality and reduce waste. Additionally, three-plate molds often eliminate the need for expensive hot runner systems, making them a more economical choice for certain applications. These molds also provide better control over the injection process, enabling more complex part designs and improved production efficiency.
Key Points Explained:
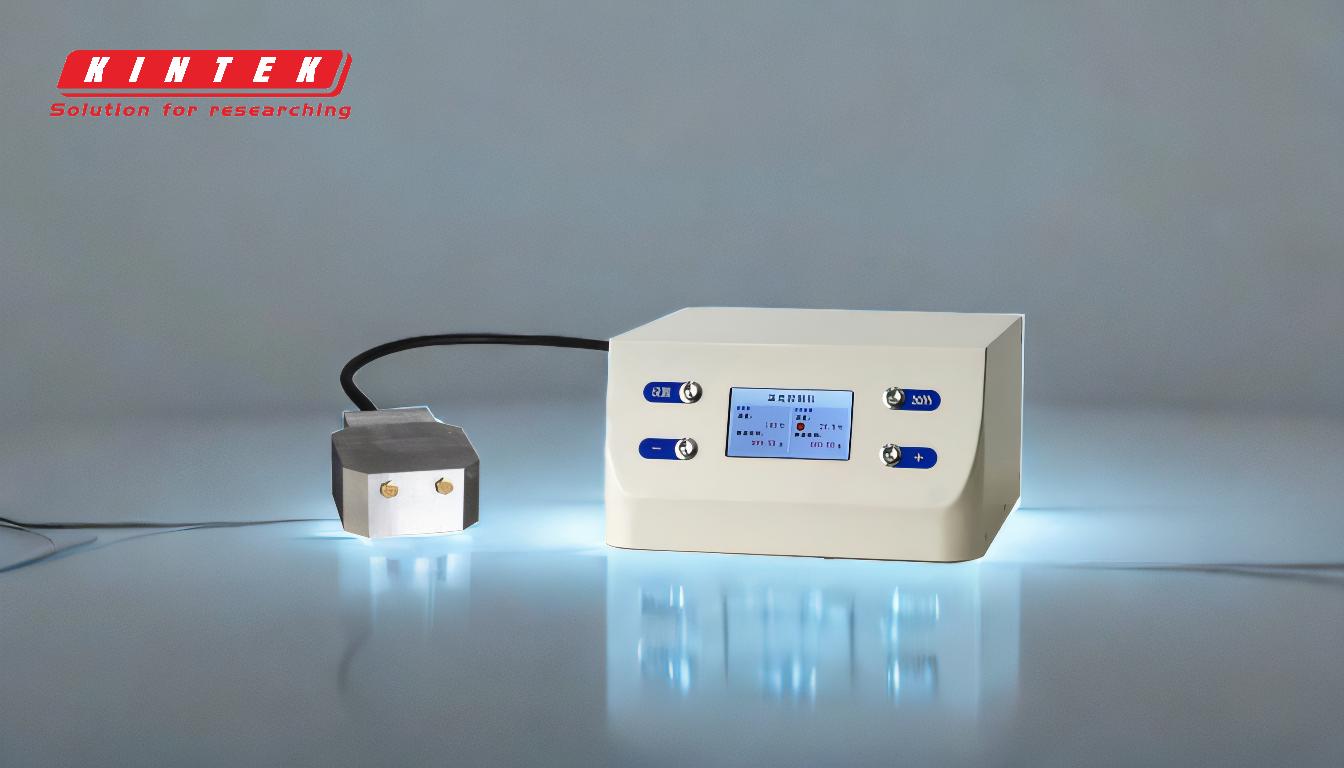
-
Central Gating:
- Explanation: Three-plate molds allow for central gating, where the gate is located at the center of the part. This ensures a more balanced flow of molten plastic, reducing the risk of warping or other defects.
- Advantage: Central gating can improve the overall quality of the molded part by ensuring uniform filling and cooling.
-
Multiple Gates Feeding a Single Part:
- Explanation: In some cases, multiple gates can be used to feed a single part. This is particularly useful for large or complex parts that require a more controlled flow of material.
- Advantage: Using multiple gates can help in achieving a more uniform distribution of material, reducing the likelihood of defects such as sink marks or voids.
-
Multiple Gates Feeding Multiple Parts:
- Explanation: Three-plate molds can also be designed to have multiple gates feeding multiple parts simultaneously. This is beneficial in high-volume production where efficiency is crucial.
- Advantage: This setup can significantly increase production rates and reduce cycle times, making it ideal for mass production.
-
Elimination of Hot Runner Systems:
- Explanation: Three-plate molds often eliminate the need for hot runner systems, which are typically used to maintain the molten state of the plastic in the runners.
- Advantage: By eliminating the need for hot runner systems, three-plate molds can reduce the overall cost of the mold and simplify the injection molding process.
-
Improved Control Over Injection Process:
- Explanation: The design of three-plate molds allows for better control over the injection process, including the timing and pressure of the injection.
- Advantage: Improved control can lead to higher precision in part dimensions and better surface finish, which is critical for high-quality parts.
-
Enhanced Flexibility in Part Design:
- Explanation: Three-plate molds offer greater flexibility in part design, allowing for more complex geometries and intricate details.
- Advantage: This flexibility can enable the production of more sophisticated parts that may not be feasible with two-plate molds.
-
Reduced Material Waste:
- Explanation: The ability to use multiple gates and central gating can lead to more efficient use of material, reducing waste.
- Advantage: Reduced material waste not only lowers production costs but also contributes to more sustainable manufacturing practices.
In summary, three-plate molds provide several significant advantages over two-plate molds, including improved part quality, increased production efficiency, cost savings, and greater design flexibility. These benefits make three-plate molds an attractive option for many injection molding applications.
Summary Table:
Advantage | Explanation | Benefit |
---|---|---|
Central Gating | Gate located at the center ensures balanced flow of molten plastic. | Reduces warping and defects, improves part quality. |
Multiple Gates Feeding a Single Part | Multiple gates control material flow for large or complex parts. | Uniform material distribution, fewer defects like sink marks or voids. |
Multiple Gates Feeding Multiple Parts | Simultaneous feeding of multiple parts for high-volume production. | Increases production rates, reduces cycle times. |
Elimination of Hot Runner Systems | No need for expensive hot runner systems. | Reduces mold costs and simplifies the process. |
Improved Control Over Injection | Better timing and pressure control during injection. | Higher precision in dimensions and better surface finish. |
Enhanced Flexibility in Part Design | Supports complex geometries and intricate details. | Enables production of sophisticated parts. |
Reduced Material Waste | Efficient material use through multiple gates and central gating. | Lowers production costs and promotes sustainability. |
Ready to enhance your injection molding process with three-plate molds? Contact us today to learn more!