Atomic Layer Deposition (ALD) is a highly precise thin-film deposition technique that offers several advantages, making it a preferred choice in various industries, including semiconductors, energy storage, and biomedical applications. ALD's unique self-limiting surface reactions enable atomic-level control over film thickness and composition, resulting in highly uniform and conformal coatings even on complex geometries. This method also allows for excellent reproducibility and scalability, making it suitable for both research and industrial applications. Additionally, ALD can deposit a wide range of materials, including oxides, nitrides, and metals, with exceptional purity and density. Its low-temperature processing capability further expands its applicability to temperature-sensitive substrates.
Key Points Explained:
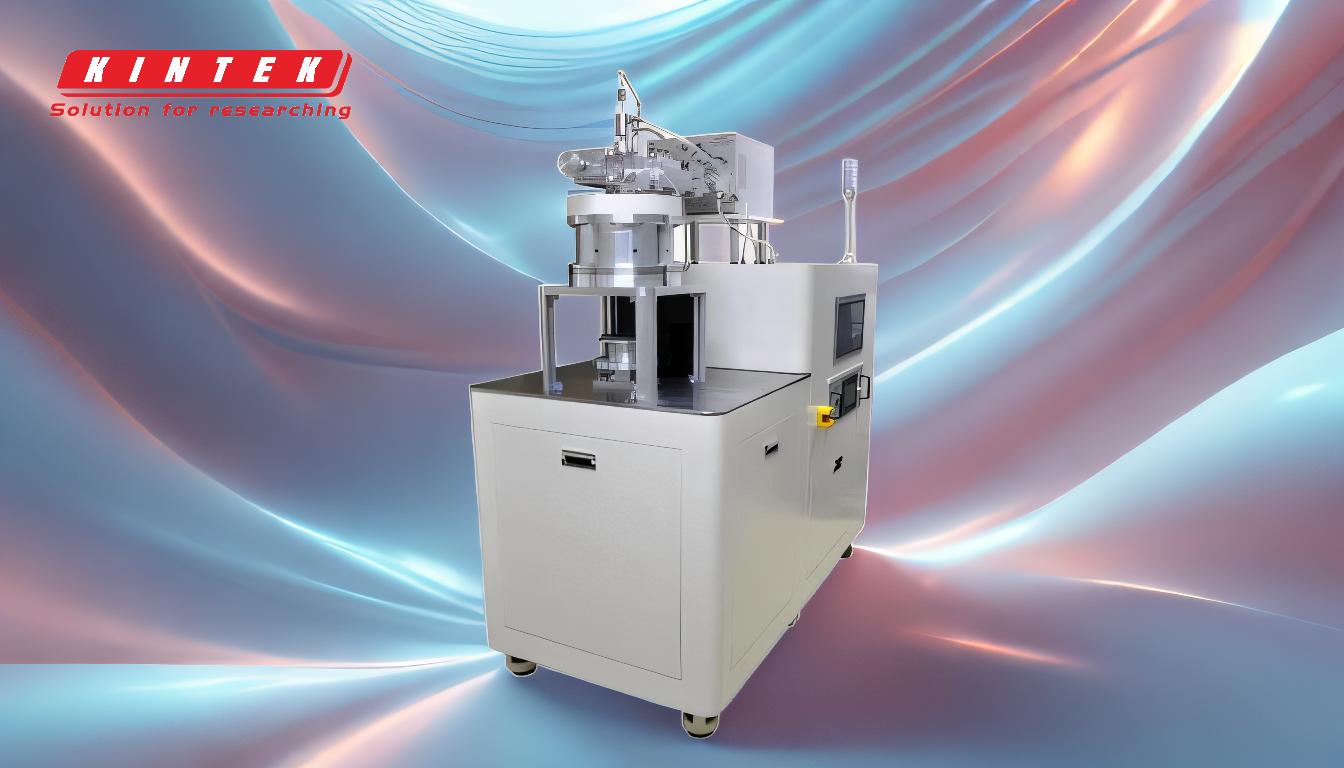
-
Atomic-Level Precision and Uniformity:
- ALD operates through sequential, self-limiting surface reactions, ensuring atomic-level control over film thickness. This precision allows for the deposition of ultra-thin films with thicknesses in the nanometer range.
- The uniformity of ALD coatings is exceptional, even on substrates with complex geometries, such as high-aspect-ratio structures or 3D surfaces. This makes ALD ideal for applications like semiconductor manufacturing, where consistent film properties are critical.
-
Conformal Coatings:
- One of the standout advantages of ALD is its ability to produce conformal coatings. Unlike other deposition techniques, ALD can evenly coat all surfaces, including trenches, pores, and other intricate features, without shadowing effects.
- This capability is particularly valuable in applications such as microelectromechanical systems (MEMS) and advanced battery technologies, where uniform coatings are essential for performance and reliability.
-
Material Versatility:
- ALD can deposit a wide variety of materials, including oxides (e.g., Al₂O₃, TiO₂), nitrides (e.g., TiN, SiN), and metals (e.g., Pt, Ru). This versatility enables the creation of multifunctional thin films tailored to specific applications.
- The ability to combine different materials in multilayer structures further enhances the functionality of ALD coatings, making them suitable for advanced electronic devices, protective barriers, and catalytic surfaces.
-
Low-Temperature Processing:
- ALD can be performed at relatively low temperatures, often below 300°C, which is advantageous for temperature-sensitive substrates such as polymers, biological materials, or flexible electronics.
- This low-temperature capability expands the range of applications for ALD, including biomedical devices and flexible displays, where traditional high-temperature processes would be detrimental.
-
Excellent Reproducibility and Scalability:
- The self-limiting nature of ALD reactions ensures high reproducibility, as each cycle deposits a consistent amount of material. This reliability is crucial for industrial applications where process consistency is paramount.
- ALD is also scalable, with processes that can be adapted for both small-scale research and large-scale production. This scalability makes it a viable option for industries ranging from nanotechnology to energy storage.
-
High Purity and Density of Deposited Films:
- ALD films are known for their high purity and density, resulting from the precise control over precursor delivery and reaction conditions. This leads to films with minimal defects and excellent barrier properties.
- These characteristics are particularly important in applications such as moisture barriers for organic electronics or protective coatings for corrosion resistance.
-
Environmental and Safety Benefits:
- ALD processes often use less hazardous precursors compared to other deposition techniques, reducing environmental and safety risks. Additionally, the controlled nature of ALD minimizes waste, making it a more sustainable option.
In summary, ALD's advantages—atomic-level precision, conformal coatings, material versatility, low-temperature processing, reproducibility, scalability, and high film quality—make it a powerful tool for advancing technology across multiple fields. Its ability to meet the demands of both cutting-edge research and industrial production ensures its continued relevance and adoption in the future.
Summary Table:
Advantage | Description |
---|---|
Atomic-Level Precision | Ensures ultra-thin, nanometer-range films with exceptional uniformity. |
Conformal Coatings | Evenly coats complex geometries, including trenches and pores. |
Material Versatility | Deposits oxides, nitrides, and metals for multifunctional applications. |
Low-Temperature Processing | Suitable for temperature-sensitive substrates like polymers and biomaterials. |
Reproducibility and Scalability | Consistent results for both research and industrial-scale production. |
High Purity and Density | Produces defect-free films with excellent barrier properties. |
Environmental and Safety Benefits | Uses less hazardous precursors and minimizes waste. |
Ready to leverage ALD for your next project? Contact our experts today to learn more!