Magnetron sputtering is a highly versatile and efficient thin film deposition technique widely used across various industries due to its numerous advantages. It enables the deposition of high-quality, uniform films with excellent adhesion, density, and purity. The process is environmentally friendly, operates at low temperatures, and is suitable for a wide range of materials, including high melting point metals and dielectrics. Additionally, it offers scalability, automation potential, and precise control over the deposition process, making it ideal for applications in microelectronics, wear resistance, corrosion resistance, and functional coatings.
Key Points Explained:
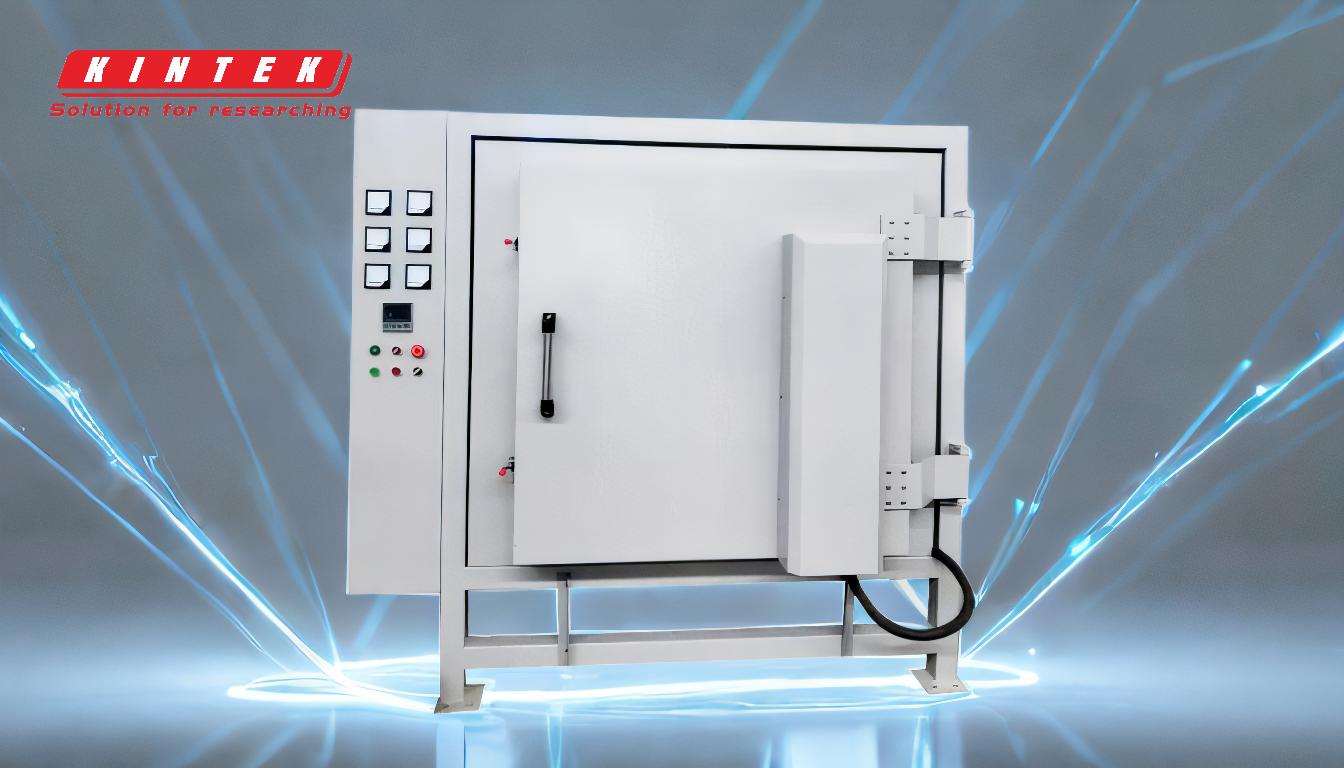
-
Versatility in Material Deposition
- Magnetron sputtering can deposit a wide range of materials, including metals, alloys, dielectrics, and compounds.
- It is particularly effective for high melting point materials that are challenging to evaporate.
- The process allows for reactive deposition, enabling the creation of compounds like nitrides and oxides by introducing reactive gases into the plasma.
-
High-Quality Films
- Films produced by magnetron sputtering exhibit high purity, density, and uniformity.
- The composition of the sputtered films closely matches that of the source material, ensuring consistency.
- The films have strong adhesion to substrates, making them durable and long-lasting.
-
Low-Temperature Process
- The technique operates at relatively low temperatures, making it suitable for heat-sensitive substrates such as polymers, textiles, and certain glasses.
- Minimal radiant heat is generated, reducing the risk of thermal damage to the substrate.
-
High Deposition Rates
- Magnetron sputtering offers fast deposition rates, especially for metals, which enhances productivity.
- The process is scalable and can be automated, making it efficient for large-scale production.
-
Uniformity and Coverage
- The process provides excellent uniformity over large-area substrates, ensuring consistent film properties.
- It offers thorough material coverage, even on complex geometries, due to the controlled sputtering environment.
-
Environmental Friendliness
- Magnetron sputtering is a clean process with minimal environmental impact.
- It operates under vacuum conditions, reducing the risk of contamination and eliminating the need for harmful chemicals.
-
Compatibility with Various Substrates
- The technique can deposit films on a wide range of substrates, including metals, glasses, ceramics, and heat-sensitive materials.
- It is suitable for both conductive and non-conductive materials, with RF magnetron sputtering enabling the deposition of dielectric films.
-
Precision and Control
- Magnetron sputtering allows for precise control over film thickness, composition, and properties.
- The process is highly reproducible, making it ideal for applications requiring tight tolerances, such as microelectronics and semiconductor manufacturing.
-
Scalability and Industrialization
- The technique is easily scalable for industrial applications, with the ability to produce large quantities of films at a low cost.
- Automation options further enhance its suitability for high-volume production environments.
-
Minimal Maintenance
- Magnetron sputtering systems are maintenance-free and designed for long-term operation.
- They are compatible with ultrahigh vacuum applications, ensuring reliability and consistency in demanding environments.
In summary, magnetron sputtering stands out as a superior thin film deposition technique due to its versatility, efficiency, and ability to produce high-quality films. Its low-temperature operation, environmental friendliness, and compatibility with a wide range of materials and substrates make it a preferred choice for industries ranging from microelectronics to functional coatings.
Summary Table:
Key Feature | Description |
---|---|
Versatility | Deposits metals, alloys, dielectrics, and compounds, including high melting point materials. |
High-Quality Films | Produces films with high purity, density, uniformity, and strong adhesion. |
Low-Temperature Process | Suitable for heat-sensitive substrates like polymers and textiles. |
High Deposition Rates | Fast deposition rates, especially for metals, enhancing productivity. |
Uniformity and Coverage | Ensures consistent film properties and thorough coverage on complex geometries. |
Environmental Friendliness | Clean process with minimal environmental impact, operating under vacuum. |
Substrate Compatibility | Works with metals, glasses, ceramics, and heat-sensitive materials. |
Precision and Control | Offers precise control over film thickness, composition, and properties. |
Scalability | Easily scalable for industrial applications, with automation potential. |
Minimal Maintenance | Maintenance-free systems designed for long-term operation. |
Ready to enhance your thin film deposition process? Contact our experts today to learn more about magnetron sputtering solutions!