RF plasma, particularly in the context of RF sputtering, offers several significant advantages over traditional DC sputtering methods. These benefits include the ability to work with insulating materials, reduced charge buildup and arcing, higher plasma efficiency at lower pressures, and improved film quality and uniformity. RF sputtering also minimizes target erosion and avoids issues like the disappearing anode effect. These advantages make RF sputtering a preferred choice for applications requiring high-quality thin films, especially with insulating or semiconductor materials.
Key Points Explained:
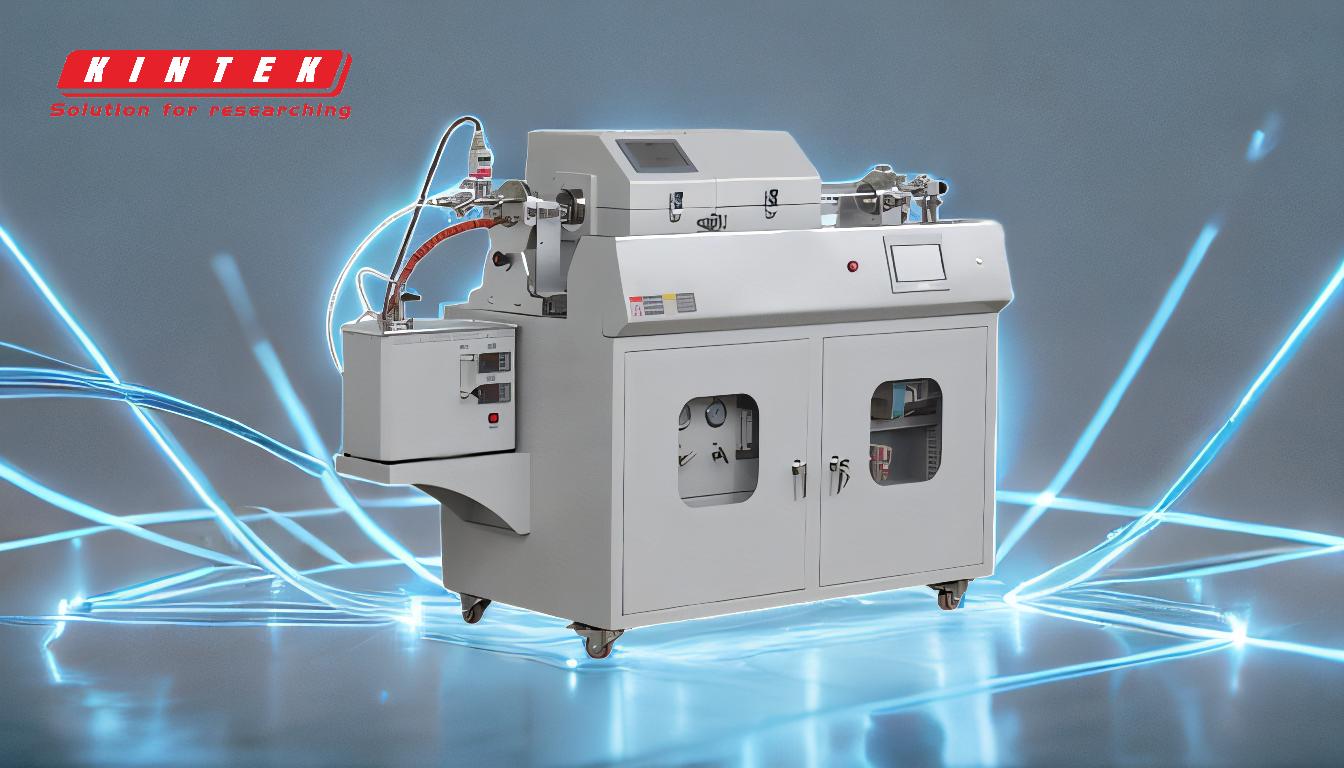
-
Ability to Sputter Insulating Materials:
- RF sputtering can effectively deposit insulating materials such as aluminum oxide or boron nitride, which are challenging to sputter using DC methods. The alternating electrical field in RF sputtering prevents charge buildup on the target surface, enabling the use of insulating targets without the risk of arcing or plasma instability.
-
Reduced Charge Buildup and Arcing:
- The oscillating nature of the RF field (typically at 13.56 MHz) ensures that charge buildup on the cathode or target surface is eliminated. This reduces the likelihood of arcing, which can damage the target and degrade film quality. As a result, RF sputtering produces more uniform and higher-quality thin films.
-
Operation at Lower Pressures:
- RF sputtering operates at significantly lower pressures (1-15 mTorr) compared to DC sputtering (around 100 mTorr). Lower pressure reduces collisions between target material particles and gas ions, creating a more direct pathway for particles to reach the substrate. This improves deposition efficiency and film quality.
-
Higher Plasma Efficiency:
- RF sputtering generates higher plasma currents at lower pressures, increasing the mean free path of target atoms and reducing collisions. This results in a more efficient sputtering process, with sputtering rates approximately 10 times higher than DC sputtering at the same chamber pressure.
-
Minimized Target Erosion:
- RF sputtering reduces "Race Track Erosion," a common issue in DC sputtering where the target erodes unevenly, forming a racetrack pattern. The larger surface area of the target involved in RF sputtering leads to more uniform erosion, extending the target's lifetime and improving process stability.
-
Improved Film Quality and Uniformity:
- RF sputtering produces films with better quality, step coverage, and microstructure compared to DC sputtering. The process is more stable, with fewer defects and improved uniformity, making it suitable for applications requiring precise thin-film deposition.
-
No Disappearing Anode Effect:
- Unlike DC sputtering, RF sputtering does not suffer from the disappearing anode effect, where the anode becomes coated with insulating material and loses its effectiveness. This ensures consistent performance and reduces the need for frequent maintenance.
-
Versatility in Material Deposition:
- RF sputtering can deposit a wide variety of materials, including insulators, metals, alloys, and composites. This versatility makes it suitable for diverse applications, from semiconductor manufacturing to optical coatings.
-
Lower Substrate Heating:
- The substrate heats up less during RF sputtering compared to DC sputtering, which is beneficial for temperature-sensitive materials. This allows for the deposition of high-quality films without compromising the integrity of the substrate.
-
Advancements in RF Diode Sputtering:
- Recent developments in RF diode sputtering technology have further enhanced the advantages of RF sputtering. This method eliminates the need for magnetic confinement, provides optimum coating uniformity, and ensures very flat target erosion with no racetrack formation or target poisoning.
In summary, RF plasma sputtering offers numerous advantages, including the ability to handle insulating materials, reduced arcing and charge buildup, operation at lower pressures, higher efficiency, and improved film quality. These benefits make RF sputtering a superior choice for applications requiring precise and high-quality thin-film deposition.
Summary Table:
Advantage | Description |
---|---|
Sputter Insulating Materials | Enables deposition of insulators like aluminum oxide without arcing. |
Reduced Charge Buildup and Arcing | Eliminates charge buildup, reducing arcing and improving film uniformity. |
Operation at Lower Pressures | Operates at 1-15 mTorr, improving deposition efficiency and film quality. |
Higher Plasma Efficiency | Generates higher plasma currents, increasing sputtering rates. |
Minimized Target Erosion | Reduces uneven erosion, extending target lifespan. |
Improved Film Quality and Uniformity | Produces films with better microstructure and fewer defects. |
No Disappearing Anode Effect | Ensures consistent performance without anode coating issues. |
Versatility in Material Deposition | Deposits insulators, metals, alloys, and composites for diverse applications. |
Lower Substrate Heating | Reduces substrate heating, ideal for temperature-sensitive materials. |
Advancements in RF Diode Sputtering | Enhances coating uniformity and eliminates racetrack formation. |
Ready to elevate your thin-film deposition process? Contact us today to learn how RF sputtering can benefit your applications!