Sputtering-based thin film deposition is a widely used Physical Vapor Deposition (PVD) technique that offers numerous advantages in various industrial and scientific applications. It enables the creation of highly precise, uniform, and durable thin films with superior properties such as smoothness, corrosion resistance, and high-temperature tolerance. Sputtering techniques, including RF, DC magnetron, ion beam, and reactive sputtering, provide flexibility in material selection, allowing for the deposition of a wide range of target materials, including those with low melting points and poor electrical conductivity. Additionally, sputtering is an environmentally friendly process that enhances component performance, extends tool life, and provides resistance to wear, erosion, and oxidation. Hybrid techniques, such as combining arc deposition with sputtering, further improve deposition rates and enable the creation of hard, nanoscale, and multilayer coatings.
Key Points Explained:
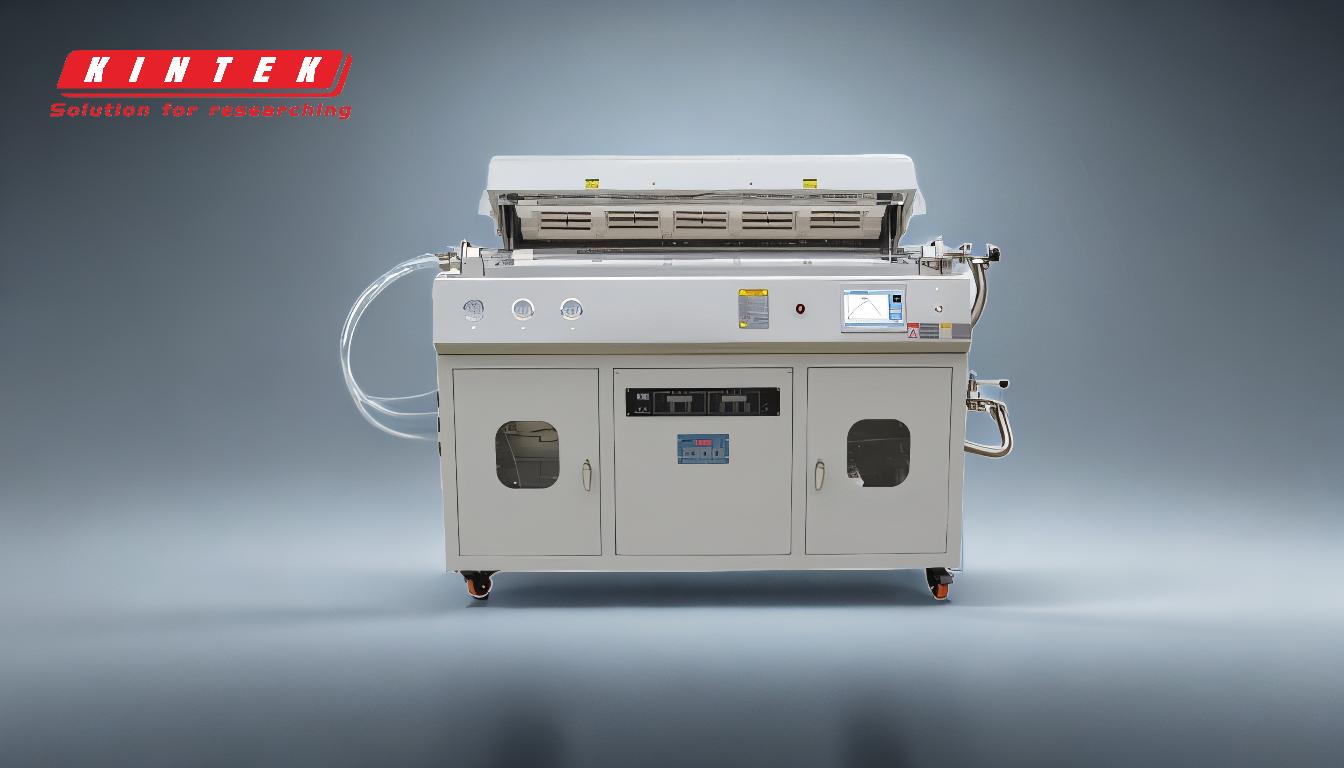
-
Versatility in Material Deposition:
- Sputtering allows for the deposition of a wide range of materials, including metals, alloys, ceramics, and compounds.
- It is particularly advantageous for materials with low melting points or poor electrical conductivity, which are challenging to deposit using other techniques.
- This versatility makes sputtering suitable for diverse applications, from microelectronics to decorative coatings.
-
High-Quality Thin Films:
- Sputtering produces thin films with excellent smoothness, uniformity, and adhesion.
- The technique enables precise control over film thickness and composition, ensuring consistent and high-quality coatings.
- These properties are critical for advanced applications such as semiconductors, optical coatings, and protective layers.
-
Enhanced Film Properties:
- Thin films deposited via sputtering exhibit superior mechanical, thermal, and chemical properties, including hardness, corrosion resistance, and high-temperature tolerance.
- These enhanced properties improve the performance and durability of components, making sputtering ideal for demanding environments.
-
Environmentally Friendly Process:
- Sputtering is a clean and eco-friendly deposition method, as it does not involve harmful chemicals or produce significant waste.
- This aligns with modern sustainability goals and reduces the environmental impact of manufacturing processes.
-
High Deposition Rates and Efficiency:
- Techniques like magnetron sputtering offer high deposition rates, making the process efficient and cost-effective.
- The ability to deposit films quickly without compromising quality is particularly beneficial for large-scale production.
-
Advanced Hybrid Techniques:
- Combining sputtering with other methods, such as arc deposition, enhances deposition rates and ion density.
- Hybrid techniques enable the creation of hard, nanoscale, and multilayer coatings, expanding the range of applications and improving performance.
-
Precision and Control:
- Sputtering provides exceptional control over the deposition process, allowing for the creation of highly precise and uniform thin films.
- This precision is essential for applications in microelectronics, optics, and nanotechnology, where even minor variations can significantly impact performance.
-
Applications in Advanced Technologies:
- Sputtering is widely used in the production of advanced thin-film devices, including semiconductors, solar cells, and optical coatings.
- Its ability to deposit high-quality films with tailored properties makes it indispensable in cutting-edge industries.
In summary, sputtering-based thin film deposition offers a combination of versatility, precision, and superior film properties, making it a preferred choice for a wide range of industrial and scientific applications. Its environmentally friendly nature and compatibility with advanced hybrid techniques further enhance its appeal, ensuring its continued relevance in modern manufacturing and technology development.
Summary Table:
Advantage | Description |
---|---|
Versatility in Material Deposition | Deposits metals, alloys, ceramics, and compounds, even with low melting points. |
High-Quality Thin Films | Produces smooth, uniform, and durable films with precise thickness control. |
Enhanced Film Properties | Offers superior hardness, corrosion resistance, and high-temperature tolerance. |
Environmentally Friendly | Clean process with minimal waste, aligning with sustainability goals. |
High Deposition Rates | Efficient and cost-effective, ideal for large-scale production. |
Advanced Hybrid Techniques | Combines sputtering with other methods for nanoscale and multilayer coatings. |
Precision and Control | Ensures highly uniform and precise thin films for critical applications. |
Applications in Advanced Tech | Used in semiconductors, solar cells, and optical coatings. |
Unlock the potential of sputtering-based thin film deposition for your projects—contact our experts today!