Sputtering and thermal evaporation are both widely used thin-film deposition techniques, but sputtering offers several advantages over thermal evaporation. These include better adhesion, more precise control over the deposition process, and the ability to maintain the composition of the source material. Additionally, sputtering provides a more uniform and realistic metal effect, greater color versatility, and improved compatibility with a wider range of materials. While thermal evaporation offers faster deposition rates, sputtering excels in producing high-quality, durable coatings with enhanced properties.
Key Points Explained:
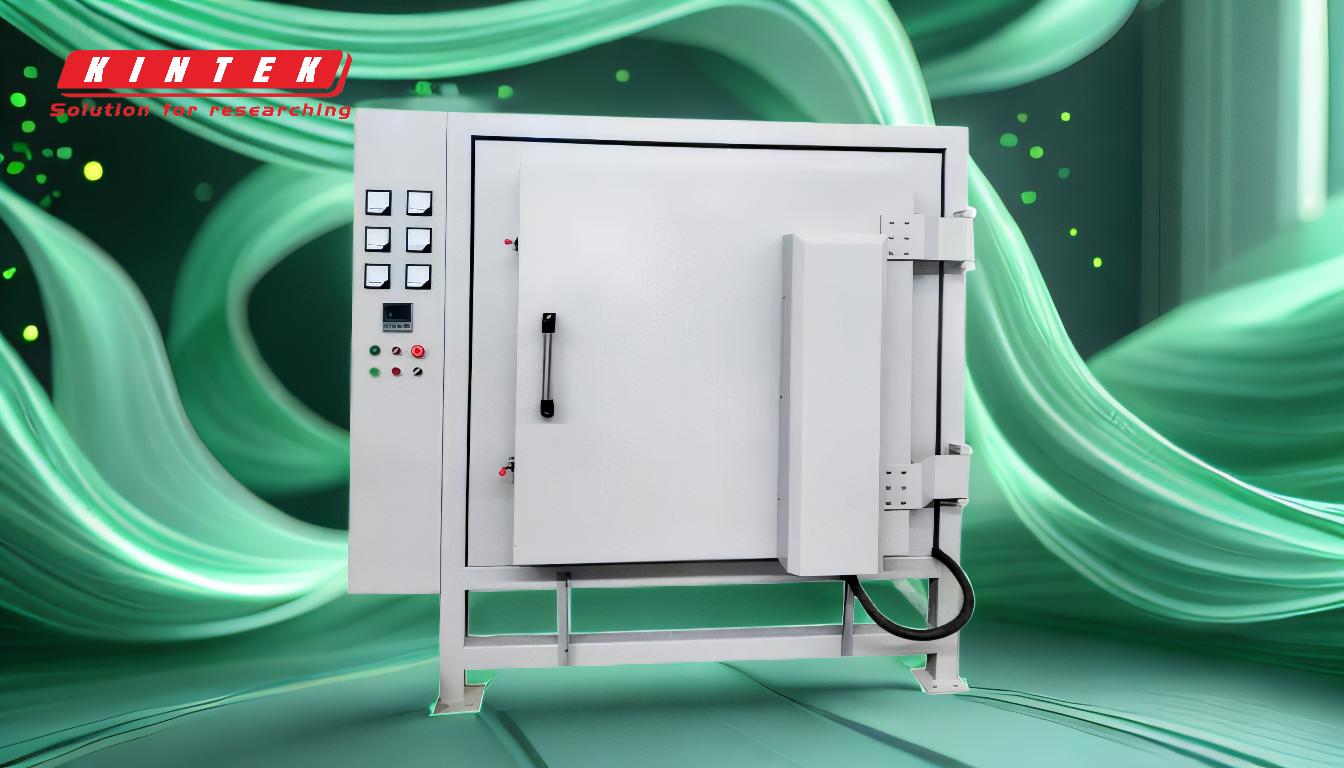
-
Better Adhesion:
- Sputtering involves energetic ions colliding with a target, which ejects atoms that bond more strongly to the substrate. This results in better adhesion compared to thermal evaporation, where the vaporized material condenses on the substrate with weaker bonding.
- Strong adhesion is critical for applications requiring durable coatings, such as in electronics, optics, and protective layers.
-
Precise Control Over Deposition:
- Sputtering allows for more control over the deposition process, including the ability to fine-tune parameters like pressure, power, and target-substrate distance. This precision ensures consistent film thickness and uniformity.
- Thermal evaporation, while faster, is less controllable and can lead to variations in film quality, especially for complex geometries or multi-layer structures.
-
Compositional Integrity:
- Sputtering maintains the composition of the source material, ensuring that the deposited film matches the target material. This is particularly important for alloys and compounds, where thermal evaporation can cause compositional changes due to differences in vapor pressures of the constituent elements.
- For example, in thermal evaporation of alloys, one element may evaporate faster than another, leading to an inconsistent final film composition.
-
Uniform and Realistic Metal Effect:
- Sputtering produces a more uniform and realistic metal effect, making it ideal for applications like decorative coatings, mirrors, and optical components.
- Thermal evaporation, while capable of producing reflective coatings, often requires additional processing (e.g., spray painting) to achieve certain colors or effects, which can compromise quality.
-
Color Versatility:
- Sputtering offers greater color versatility through modulation of the deposition process, enabling the creation of a wide range of colors without the need for additional coatings.
- In contrast, thermal evaporation is limited to the natural color of the source material (e.g., aluminum) and requires post-processing for other colors.
-
Compatibility with a Wider Range of Materials:
- Sputtering can deposit a broader range of materials, including metals, alloys, ceramics, and even insulating materials, due to its ability to handle high-melting-point materials and complex compositions.
- Thermal evaporation is less effective for materials with very high melting points or those that decompose upon heating.
-
Improved Film Quality:
- The energetic nature of sputtering results in denser, more defect-free films with better mechanical and optical properties compared to thermal evaporation.
- This makes sputtering suitable for high-performance applications, such as semiconductor devices, solar cells, and advanced optics.
-
Scalability and Reproducibility:
- Sputtering processes are highly scalable and reproducible, making them ideal for industrial applications where consistency and reliability are critical.
- Thermal evaporation, while simpler, can be less predictable and harder to scale for large-area or high-throughput production.
-
Reduced Thermal Stress on Substrates:
- Sputtering operates at lower temperatures compared to thermal evaporation, reducing the risk of thermal damage to sensitive substrates.
- This is particularly important for substrates like polymers or temperature-sensitive materials, which can degrade or deform under high heat.
-
Environmental and Safety Considerations:
- Sputtering is generally safer and more environmentally friendly, as it does not involve heating materials to extremely high temperatures, reducing the risk of hazardous emissions.
- Thermal evaporation, on the other hand, can produce harmful vapors or particles, especially when working with toxic or reactive materials.
In summary, while thermal evaporation is advantageous for its simplicity and high deposition rates, sputtering offers superior film quality, control, and versatility, making it the preferred choice for many advanced applications.
Summary Table:
Feature | Sputtering | Thermal Evaporation |
---|---|---|
Adhesion | Stronger bonding due to energetic ion collisions | Weaker bonding, less durable |
Control Over Deposition | Precise control of parameters (pressure, power, distance) | Less controllable, variable film quality |
Compositional Integrity | Maintains source material composition, ideal for alloys and compounds | Risk of compositional changes due to vapor pressure differences |
Uniformity | More uniform and realistic metal effect | Requires additional processing for uniformity |
Color Versatility | Wide range of colors achievable without coatings | Limited to source material color, requires post-processing |
Material Compatibility | Works with metals, alloys, ceramics, and insulators | Limited effectiveness for high-melting-point or heat-sensitive materials |
Film Quality | Denser, defect-free films with superior mechanical and optical properties | Less dense, more defects |
Scalability | Highly scalable and reproducible for industrial applications | Less predictable, harder to scale |
Thermal Stress | Lower temperatures reduce risk of substrate damage | Higher temperatures may damage sensitive substrates |
Environmental Safety | Safer, fewer hazardous emissions | Risk of harmful vapors or particles |
Ready to elevate your thin-film deposition process? Contact us today to learn how sputtering can meet your advanced application needs!