Welding is a critical process in various industries, enabling the fabrication and repair of metal structures and components. It is widely used in industries such as construction, manufacturing, automotive, aerospace, shipbuilding, and HVAC systems. Welding ensures the durability, strength, and integrity of metal products, making it indispensable in modern industrial applications. Below, we explore the key applications of welding in detail.
Key Points Explained:
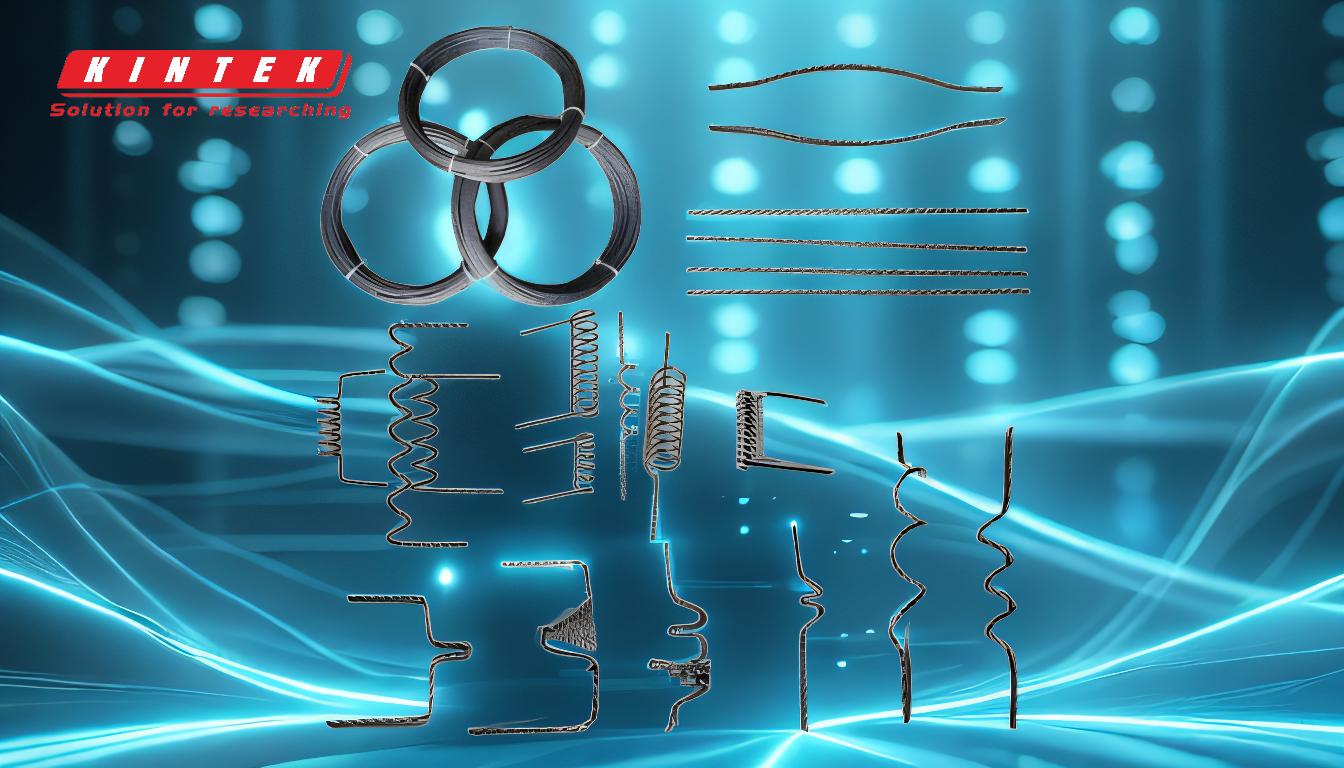
-
Metal Furniture Manufacturing
- Welding is extensively used in the production of metal furniture, including office desks, file cabinets, and shelving units.
- It provides structural integrity and durability to furniture pieces, ensuring they can withstand daily use.
- Welding allows for the creation of complex designs and seamless joints, enhancing both functionality and aesthetics.
-
Heating, Ventilation, and Air Conditioning (HVAC) Systems
- HVAC units are typically constructed using welding processes to assemble metal components like ducts, frames, and heat exchangers.
- Welding ensures airtight and leak-proof connections, which are critical for the efficient operation of HVAC systems.
- The durability of welded joints is essential for withstanding temperature fluctuations and mechanical stress.
-
Shipbuilding
- Welding has been the primary construction method in shipbuilding since the Industrial Age.
- It is used to join large metal plates and structural components, forming the hull and other parts of ships.
- Welding ensures the watertight integrity and structural strength required for maritime vessels to endure harsh marine environments.
-
Construction Industry
- Welding is fundamental in constructing steel frameworks for buildings, bridges, and other infrastructure.
- It provides the strength and stability needed to support heavy loads and withstand environmental stresses.
- Welding is also used in the installation of pipelines, reinforcing bars, and other structural elements.
-
Automotive Industry
- Welding is used extensively in the manufacturing of vehicles, including cars, trucks, and motorcycles.
- It is employed to assemble body panels, chassis, and engine components, ensuring safety and performance.
- Advanced welding techniques, such as robotic welding, are used to achieve precision and consistency in mass production.
-
Aerospace Industry
- Welding plays a crucial role in the fabrication of aircraft and spacecraft components.
- It is used to join lightweight materials like aluminum and titanium, which are essential for achieving high strength-to-weight ratios.
- Welding ensures the structural integrity and reliability of aerospace components under extreme conditions.
-
Energy Sector
- Welding is used in the construction and maintenance of power plants, including nuclear, thermal, and renewable energy facilities.
- It is essential for assembling pipelines, pressure vessels, and turbines, which require high precision and durability.
- Welding also plays a role in the installation of solar panels and wind turbines, contributing to sustainable energy solutions.
-
Repair and Maintenance
- Welding is widely used for repairing damaged or worn-out metal components in various industries.
- It extends the lifespan of equipment and structures, reducing the need for costly replacements.
- Techniques like welding overlays and cladding are used to restore and enhance the performance of critical parts.
-
Art and Sculpture
- Welding is employed by artists and sculptors to create intricate metal artworks and sculptures.
- It allows for the fusion of different metals and the creation of unique designs, showcasing the versatility of welding beyond industrial applications.
-
Custom Fabrication
- Welding is used in custom fabrication to create specialized metal components and structures tailored to specific needs.
- It enables the production of prototypes, one-off designs, and bespoke solutions for various industries.
By understanding these applications, equipment and consumable purchasers can make informed decisions about the types of welding tools, materials, and technologies required for their specific industrial needs. Welding remains a cornerstone of modern manufacturing and construction, driving innovation and efficiency across sectors.
Summary Table:
Industry | Key Applications |
---|---|
Metal Furniture | Production of durable, complex designs for office desks, cabinets, and shelving. |
HVAC Systems | Assembly of airtight ducts, frames, and heat exchangers for efficient operation. |
Shipbuilding | Joining metal plates for hulls, ensuring watertight integrity and structural strength. |
Construction | Building steel frameworks, bridges, and pipelines for strength and stability. |
Automotive | Assembling body panels, chassis, and engine components for safety and performance. |
Aerospace | Fabricating lightweight, high-strength components for aircraft and spacecraft. |
Energy Sector | Constructing pipelines, turbines, and renewable energy installations. |
Repair & Maintenance | Extending equipment lifespan through welding overlays and cladding. |
Art & Sculpture | Creating intricate metal artworks and sculptures. |
Custom Fabrication | Producing specialized components and bespoke solutions for unique needs. |
Ready to enhance your welding capabilities? Contact our experts today for tailored solutions!