Diamond coatings offer a wide range of benefits due to the unique properties of diamond materials. These benefits include exceptional mechanical strength, high thermal conductivity, excellent biocompatibility, and superior optical properties. These characteristics make diamond coatings highly valuable in various industries, including electronics, biomedical applications, precision machining, and advanced sensing technologies. The ability of diamond to withstand extreme conditions and its versatility in applications ranging from wear-resistant coatings to quantum sensors highlight its importance in modern technology and research.
Key Points Explained:
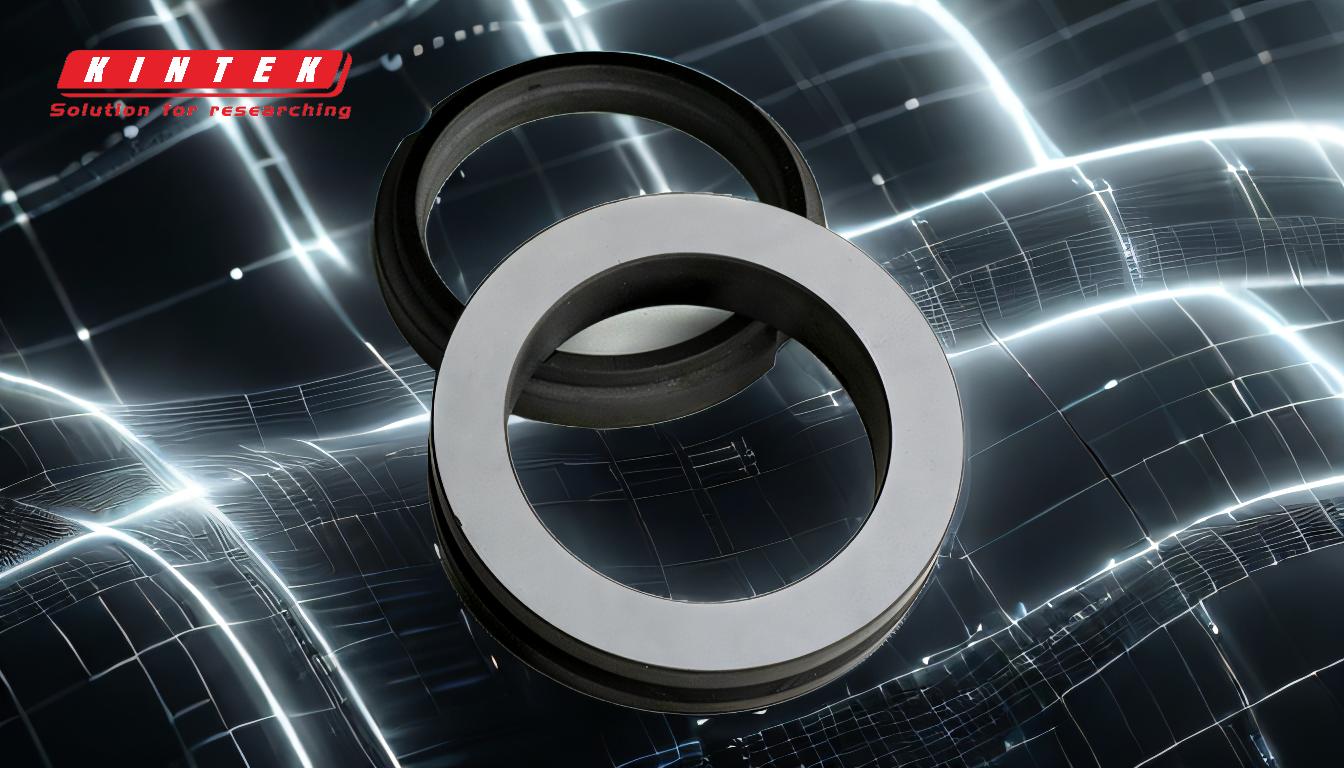
-
Exceptional Mechanical Strength:
- Diamond is renowned for its extreme mechanical strength, making it one of the hardest known materials. This property is crucial for applications requiring wear-resistant coatings, such as in industrial machinery and cutting tools. The durability of diamond coatings ensures longer lifespan and reduced maintenance costs for equipment subjected to high wear and tear.
-
High Thermal Conductivity:
- Diamond has one of the highest thermal conductivities of any material, which is essential for applications in thermal management. This property is particularly beneficial in electronics, where efficient heat dissipation is critical to maintaining performance and preventing overheating. Diamond coatings are used in thermal spreaders and heat sinks to enhance the thermal management of high-performance electronic devices.
-
Excellent Biocompatibility:
- Diamond films exhibit excellent biocompatibility, making them suitable for biomedical applications. For instance, diamond coatings are used on artificial joints to reduce wear and improve longevity. Additionally, the smooth surface of diamond films minimizes friction and wear in biomedical implants, enhancing patient outcomes.
-
Superior Optical Properties:
- The optical properties of diamond materials are exceptional, making them ideal for use in optical components and biological detection systems. Diamond coatings can be used in lenses, windows, and other optical devices where high transparency and low optical distortion are required. In biomedical imaging, diamond's optical properties enable high-resolution imaging and accurate detection.
-
Versatility in Industrial Applications:
- Synthetic diamond is utilized in a wide range of industrial applications, including precision machining, drilling, and crushing. Its unique properties make it suitable for industries that demand high performance in challenging environments. Diamond coatings are also used in water treatment systems, where their durability and resistance to corrosion are advantageous.
-
Advanced Sensing and Detection:
- Diamond materials are integral to advanced sensing technologies. For example, nano-diamond particles are used as bio-markers and in drug delivery monitoring. Diamond-based quantum sensors, which utilize shallow nitrogen vacancy (NV) centers, can detect variations in magnetic and electric fields, temperature, and gravity with high precision. These sensors are crucial for applications in scientific research, medical diagnostics, and environmental monitoring.
-
Fundamental and Applied Research:
- Diamond thin films, which possess properties similar to bulk diamond, are used in both industrial applications and fundamental studies in academia. Researchers utilize diamond coatings to explore new materials and technologies, pushing the boundaries of what is possible in fields such as electronics, photonics, and quantum computing.
In summary, the benefits of diamond coatings are vast and varied, driven by the exceptional properties of diamond materials. From enhancing the durability of industrial equipment to enabling cutting-edge biomedical and sensing technologies, diamond coatings play a pivotal role in advancing modern technology and improving the performance of a wide range of applications.
Summary Table:
Property | Benefits | Applications |
---|---|---|
Exceptional Mechanical Strength | High durability, wear resistance, reduced maintenance costs | Industrial machinery, cutting tools |
High Thermal Conductivity | Efficient heat dissipation, prevents overheating | Electronics, thermal spreaders, heat sinks |
Excellent Biocompatibility | Reduced wear, improved longevity, minimal friction | Biomedical implants, artificial joints |
Superior Optical Properties | High transparency, low distortion, accurate detection | Optical components, biomedical imaging |
Versatility in Industrial Use | High performance in challenging environments, corrosion resistance | Precision machining, water treatment systems |
Advanced Sensing & Detection | High-precision detection of magnetic/electric fields, temperature, gravity | Quantum sensors, scientific research, medical diagnostics |
Fundamental & Applied Research | Exploration of new materials and technologies | Electronics, photonics, quantum computing |
Explore how diamond coatings can enhance your applications—contact our experts today!