A grinding mill, particularly a ball mill grinder, consists of several key components that work together to achieve the desired grinding or mixing of materials. The primary components include the cylinder and the grinding balls. The cylinder, typically made of durable materials like metal, porcelain, or rubber, rotates around its horizontal axis to facilitate the grinding process. Inside the cylinder, grinding balls, usually made of stainless steel, occupy 30-50% of the cylinder's volume and play a crucial role in breaking down the material through impact and friction. These components are essential for the efficient operation of the grinding mill.
Key Points Explained:
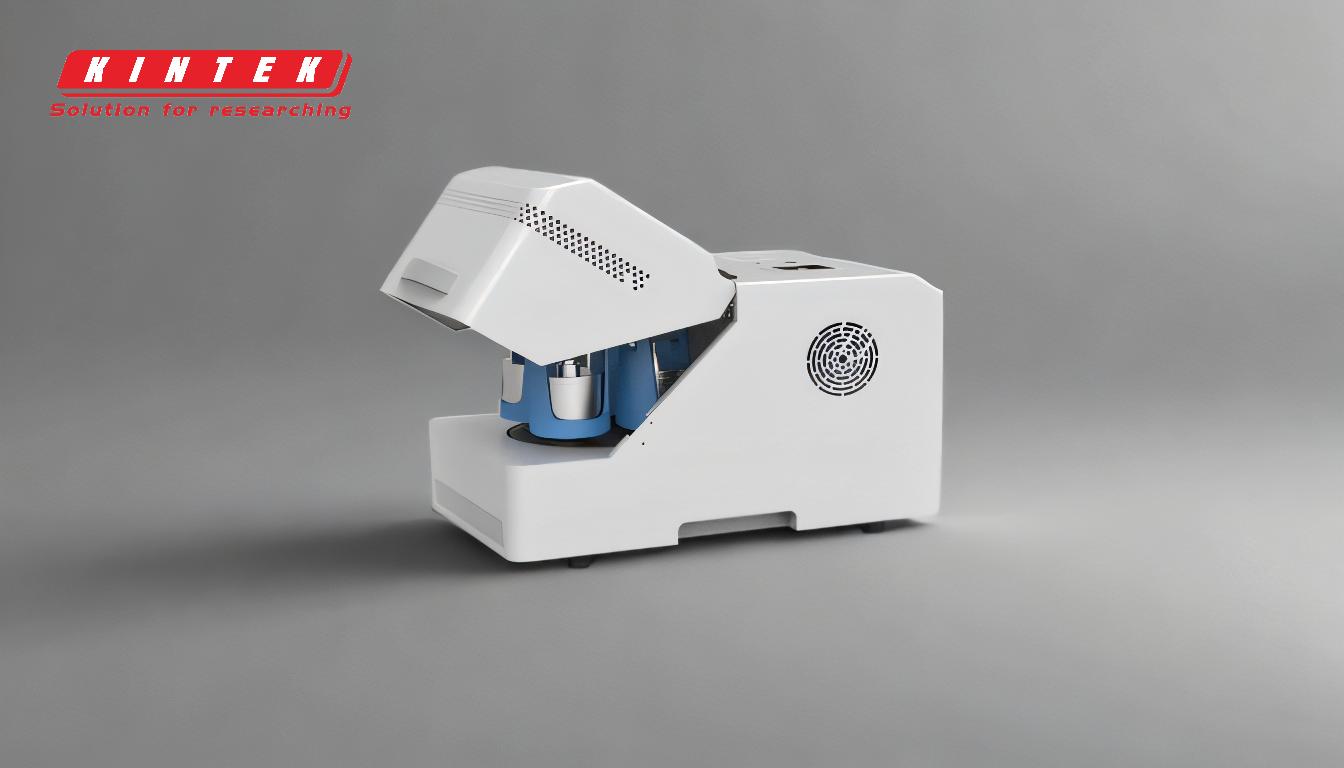
-
Cylinder:
- Function: The cylinder is the main body of the grinding mill, providing the space where the grinding process occurs. It rotates around its horizontal axis, allowing the material and grinding balls to move and interact.
-
Materials: The cylinder can be constructed from various materials, including:
- Metal: Offers durability and strength, suitable for heavy-duty grinding.
- Porcelain: Provides a smooth surface, often used in applications requiring contamination-free grinding.
- Rubber: Used in specific applications where noise reduction or cushioning is necessary.
- Design: The cylinder is typically hollow, allowing for the insertion of grinding balls and the material to be ground. Its design ensures efficient movement and interaction between the balls and the material.
-
Grinding Balls:
- Function: The grinding balls are the primary agents of the grinding process. They impact and crush the material as the cylinder rotates, breaking it down into smaller particles.
- Materials: Grinding balls are usually made of stainless steel due to its hardness, durability, and resistance to wear and corrosion. Other materials may be used depending on the specific application.
- Quantity and Coverage: The balls occupy 30-50% of the cylinder's volume. This range ensures optimal grinding efficiency by providing enough space for the balls to move freely while maintaining sufficient contact with the material.
- Size and Shape: The size and shape of the grinding balls can vary depending on the material being processed and the desired fineness of the grind. Larger balls are used for coarse grinding, while smaller balls are used for finer grinding.
-
Rotation Mechanism:
- Function: The rotation of the cylinder is a critical aspect of the grinding process. It ensures that the grinding balls and the material are constantly in motion, leading to effective grinding.
- Speed Control: The speed of rotation can be adjusted to control the grinding process. Higher speeds result in more aggressive grinding, while lower speeds are used for finer grinding or mixing.
- Drive System: The rotation is typically powered by an electric motor connected to the cylinder via a drive system, such as gears or belts. This system must be robust and reliable to ensure consistent operation.
-
Lining:
- Function: The inner surface of the cylinder may be lined with a protective material to reduce wear and extend the lifespan of the cylinder.
- Materials: Common lining materials include rubber, ceramic, or metal alloys. The choice of lining material depends on the type of material being ground and the desired grinding conditions.
- Benefits: Lining helps to minimize contamination of the ground material, reduce noise, and protect the cylinder from abrasion and impact damage.
-
Discharge Mechanism:
- Function: After the grinding process, the ground material needs to be discharged from the cylinder. The discharge mechanism ensures that the material is efficiently removed without clogging or contamination.
-
Types: Common discharge mechanisms include:
- Grate Discharge: Uses a grate at the end of the cylinder to allow the ground material to exit while retaining the grinding balls.
- Overflow Discharge: Allows the ground material to overflow out of the cylinder, typically used for finer grinding.
- Design Considerations: The discharge mechanism must be designed to handle the specific characteristics of the ground material, such as particle size and flowability.
-
Support Structure:
- Function: The support structure holds the cylinder and other components in place, ensuring stability and alignment during operation.
- Materials: Typically made of heavy-duty steel to withstand the weight and forces generated during grinding.
- Design: The support structure must be designed to allow easy access for maintenance and inspection while providing a stable base for the grinding mill.
In summary, the components of a grinding mill, particularly a ball mill grinder, include the cylinder, grinding balls, rotation mechanism, lining, discharge mechanism, and support structure. Each component plays a vital role in ensuring the efficient and effective grinding of materials. Understanding these components is essential for selecting the right grinding mill for specific applications and ensuring its proper operation and maintenance.
Summary Table:
Component | Function | Materials/Details |
---|---|---|
Cylinder | Main body for grinding; rotates to facilitate material and ball interaction. | Metal, porcelain, or rubber for durability, smoothness, or noise reduction. |
Grinding Balls | Crush and break down material through impact and friction. | Stainless steel (common); size and shape vary based on grinding needs. |
Rotation Mechanism | Powers cylinder rotation for effective grinding. | Electric motor with gears or belts; adjustable speed for control. |
Lining | Protects cylinder from wear and reduces contamination. | Rubber, ceramic, or metal alloys; chosen based on material and grinding conditions. |
Discharge Mechanism | Removes ground material efficiently. | Grate or overflow discharge; designed for particle size and flowability. |
Support Structure | Provides stability and alignment for the grinding mill. | Heavy-duty steel; ensures durability and easy maintenance access. |
Need help selecting the right grinding mill for your application? Contact our experts today for personalized guidance!