Pyrolysis, while a promising technology for waste management and energy production, comes with several significant disadvantages. These include high operational and investment costs, the need for advanced air purification systems to treat flue gases, and the production of hazardous waste such as ashes containing heavy metals. Additionally, the process requires high energy consumption, long residence times, and further refining of products like bio-oil, making it less cost-effective for small-scale applications. Emissions from pyrolysis can negatively impact air quality, and the process faces technical challenges in scaling up, along with variability in feedstock quality and final product consistency. These factors necessitate ongoing research and development to optimize the process and mitigate its drawbacks.
Key Points Explained:
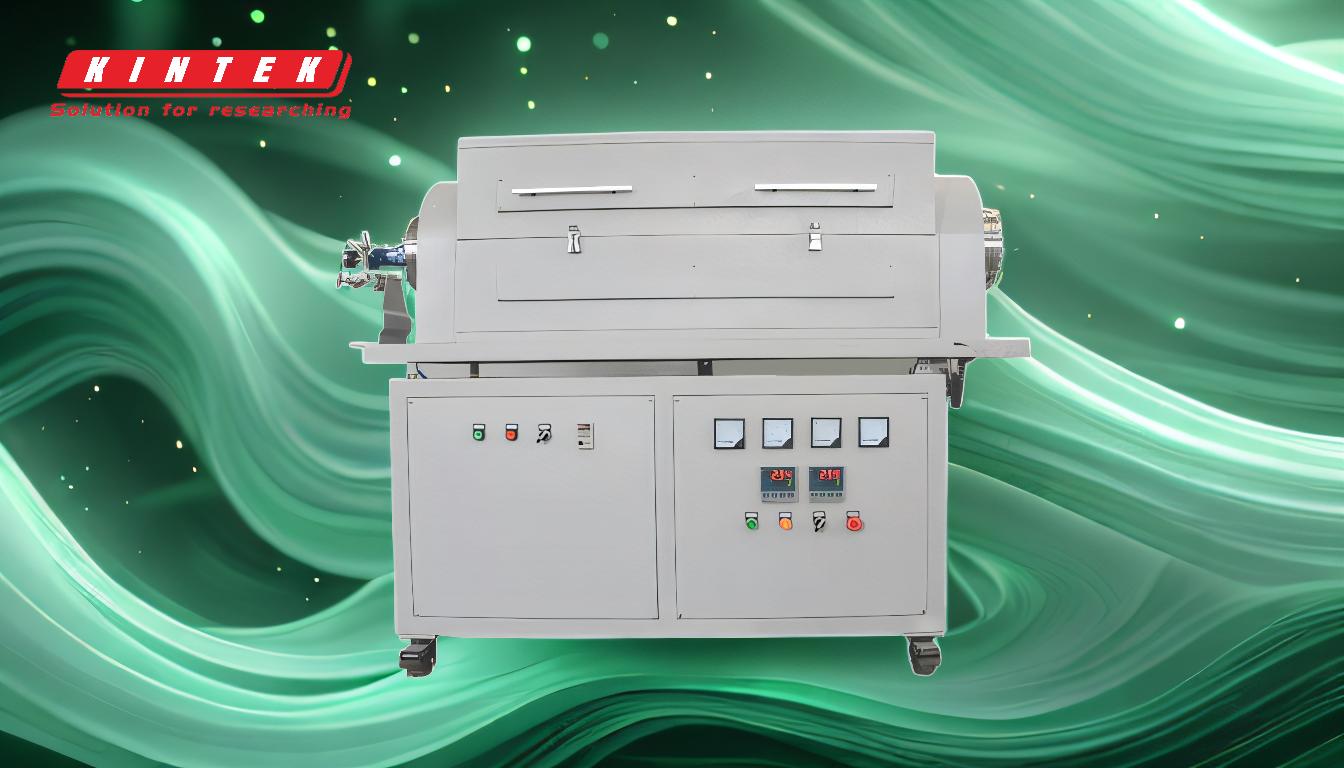
-
High Operational and Investment Costs
- Pyrolysis requires significant capital investment due to the need for specialized equipment capable of withstanding high temperatures and processing mixed product streams.
- Operational costs are also high, as the process consumes large amounts of energy to maintain the necessary high temperatures and long residence times.
- The mixed product stream often requires further separation and purification, adding to the overall cost.
-
Air Purification and Emissions Control
- The process generates flue gases that contain harmful emissions, including volatile organic compounds (VOCs) and particulate matter, which can negatively impact air quality.
- To comply with environmental regulations, such as EU clean air standards, advanced air purification systems are required. These systems are technically demanding and expensive to install and maintain.
- Proper design, operation, and maintenance are critical to minimizing emissions and ensuring the process is environmentally friendly.
-
Production of Hazardous Waste
- Pyrolysis produces ashes with high concentrations of heavy metals, which are classified as dangerous waste.
- Disposal of this hazardous waste requires specialized handling and treatment, further increasing costs and environmental concerns.
-
Energy Consumption and Process Efficiency
- The process demands high energy input to achieve the necessary temperatures and sustain the reaction over long residence times.
- This high energy consumption reduces the overall efficiency of the process, particularly for small-scale applications.
-
Challenges in Product Refinement
- Bio-oil, one of the primary products of pyrolysis, requires additional refining before it can be used as a transportation fuel.
- The need for refining adds complexity and cost, making the process less economically viable for certain applications.
-
Technical Challenges in Scaling Up
- Scaling up pyrolysis from laboratory or pilot-scale to industrial-scale operations presents significant technical challenges.
- Variability in feedstock quality and composition can affect the consistency and quality of the final products, complicating large-scale implementation.
-
Environmental and Regulatory Concerns
- The process must adhere to strict environmental regulations, which can be difficult and costly to meet.
- Emissions control and waste management are critical to ensuring the process does not harm the environment or public health.
-
Feedstock Variability
- The quality and composition of feedstock can vary widely, impacting the efficiency and output of the pyrolysis process.
- This variability necessitates careful selection and preprocessing of feedstock, adding to the complexity and cost.
-
Need for Further Research and Development
- Many of the challenges associated with pyrolysis, such as emissions control, waste management, and process optimization, require ongoing research and development.
- Innovations in technology and process design are essential to making pyrolysis more economically viable and environmentally sustainable.
In conclusion, while pyrolysis offers potential benefits for waste management and energy production, its disadvantages—ranging from high costs and technical challenges to environmental concerns—highlight the need for continued innovation and optimization to address these issues effectively.
Summary Table:
Disadvantage | Key Details |
---|---|
High Operational Costs | Significant capital investment, high energy consumption, and purification costs. |
Emissions & Air Purification | Requires advanced systems to treat harmful flue gases and comply with regulations. |
Hazardous Waste Production | Ashes with heavy metals require specialized disposal, increasing costs. |
Energy Consumption | High energy input reduces efficiency, especially for small-scale applications. |
Product Refinement Challenges | Bio-oil needs additional refining, adding complexity and cost. |
Scaling Up Difficulties | Technical challenges and feedstock variability complicate large-scale operations. |
Environmental & Regulatory Hurdles | Strict regulations increase costs and complexity. |
Feedstock Variability | Inconsistent feedstock quality impacts process efficiency and output. |
Need for R&D | Ongoing innovation is required to optimize and mitigate drawbacks. |
Interested in overcoming pyrolysis challenges? Contact our experts today to explore sustainable solutions!