Plastic pyrolysis oil is a product derived from the thermal decomposition of plastic waste. While it offers a promising avenue for recycling and energy recovery, the oil often contains various contaminants that can affect its quality and usability. These contaminants arise from the heterogeneous nature of plastic waste, which includes different types of plastics, additives, and non-plastic materials. Understanding these contaminants is crucial for improving the purification processes and ensuring the oil's suitability for various applications.
Key Points Explained:
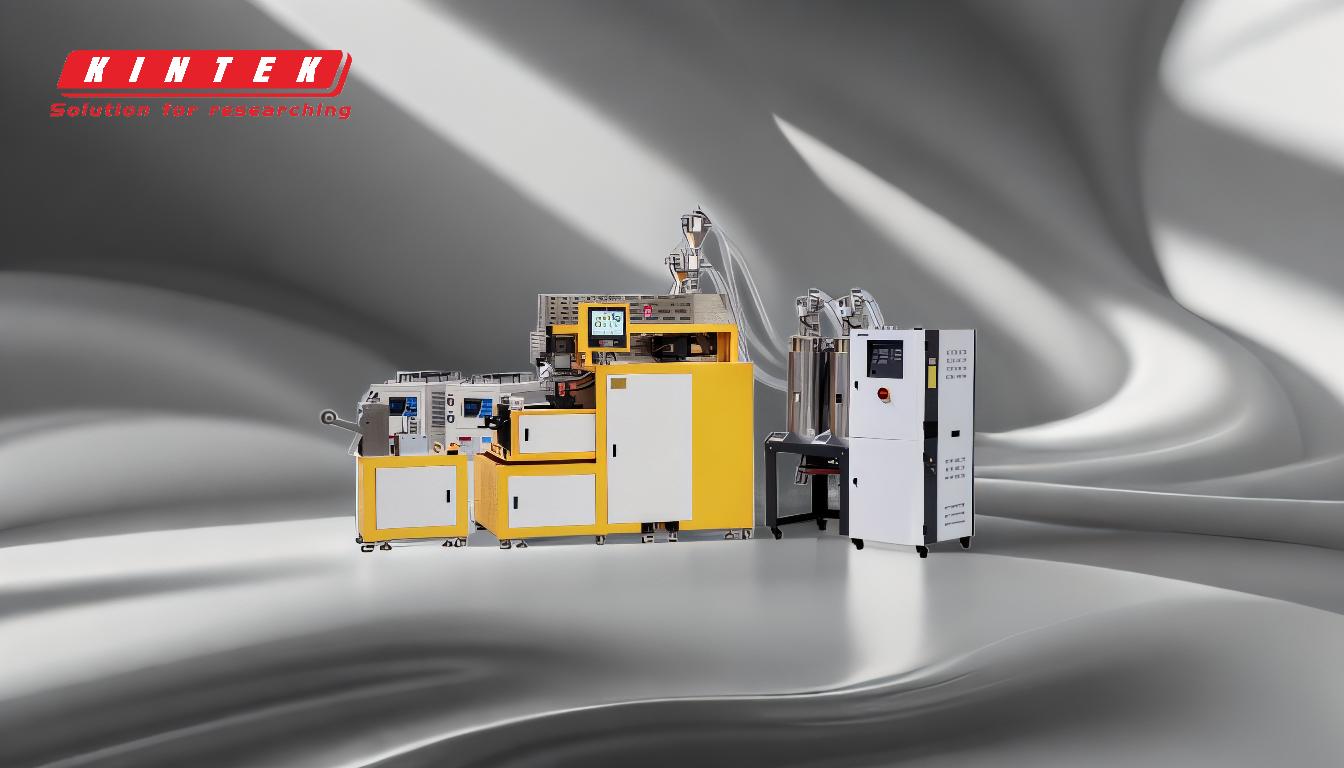
-
Sources of Contaminants in Plastic Pyrolysis Oil
- Plastic Composition: Different types of plastics (e.g., polyethylene, polypropylene, PVC) have varying chemical structures, which can lead to the formation of different contaminants during pyrolysis. For example, PVC can release chlorine compounds, which are harmful contaminants.
- Additives: Plastics often contain additives like plasticizers, flame retardants, and stabilizers. These additives can break down during pyrolysis and contribute to the contamination of the oil.
- Non-Plastic Content: Plastic waste often includes non-plastic materials such as paper, adhesives, and metals. These materials can introduce impurities like ash, char, and inorganic compounds into the pyrolysis oil.
- Moisture Content: High moisture content in the feedstock can lead to the formation of water and oxygenated compounds in the oil, reducing its quality.
-
Types of Contaminants
- Chlorinated Compounds: Derived from chlorine-containing plastics like PVC, these compounds are toxic and corrosive, posing environmental and operational challenges.
- Sulfur Compounds: Plastics with sulfur-containing additives can produce sulfur oxides and other sulfur-based contaminants, which are harmful to the environment and equipment.
- Heavy Metals: Metals from pigments, stabilizers, or other additives can end up in the pyrolysis oil, posing health and environmental risks.
- Particulate Matter: Char and ash particles from incomplete pyrolysis or non-plastic content can contaminate the oil, affecting its clarity and usability.
- Oxygenated Compounds: Water and oxygen in the feedstock can lead to the formation of acids, alcohols, and other oxygenated compounds, which degrade the oil's stability and energy content.
-
Impact of Contaminants
- Environmental Concerns: Chlorinated and sulfur compounds can contribute to air pollution and acid rain when the oil is combusted. Heavy metals can accumulate in the environment, causing long-term ecological damage.
- Operational Challenges: Contaminants like particulate matter and heavy metals can cause fouling and corrosion in storage tanks, pipelines, and engines, increasing maintenance costs.
- Reduced Usability: The presence of contaminants limits the oil's applications. For instance, high chlorine content may prevent its use as a fuel in certain industrial processes due to regulatory restrictions.
-
Mitigation Strategies
- Feedstock Pre-Treatment: Sorting and cleaning plastic waste before pyrolysis can reduce the introduction of non-plastic materials and moisture. Removing chlorine-containing plastics like PVC can significantly reduce chlorinated contaminants.
- Advanced Pyrolysis Technologies: Technologies like catalytic pyrolysis can help break down contaminants more effectively, improving oil quality.
- Post-Pyrolysis Purification: Techniques such as filtration, distillation, and chemical treatment can remove contaminants like particulates, heavy metals, and chlorine compounds.
- Additive Removal: Developing methods to extract or neutralize additives before pyrolysis can reduce the formation of harmful by-products.
-
Future Directions
- Improved Feedstock Quality: Enhancing the sorting and pre-treatment of plastic waste will be critical to minimizing contaminants in pyrolysis oil.
- Innovative Purification Methods: Research into new purification technologies, such as membrane filtration and advanced chemical treatments, can further improve oil quality.
- Regulatory Standards: Establishing clear standards for pyrolysis oil quality will drive the development of better purification processes and expand the oil's applications.
In conclusion, contaminants in plastic pyrolysis oil are a significant challenge that stems from the diverse and often impure nature of plastic waste. Addressing these contaminants requires a combination of feedstock pre-treatment, advanced pyrolysis technologies, and post-pyrolysis purification methods. By improving the quality of pyrolysis oil, we can enhance its usability and environmental sustainability, making it a more viable solution for plastic waste management and energy recovery.
Summary Table:
Category | Details |
---|---|
Sources of Contaminants | - Plastic composition (e.g., PVC, polyethylene) |
- Additives (plasticizers, flame retardants) | |
- Non-plastic content (paper, metals, adhesives) | |
- Moisture content | |
Types of Contaminants | - Chlorinated compounds (toxic, corrosive) |
- Sulfur compounds (harmful to environment and equipment) | |
- Heavy metals (health and environmental risks) | |
- Particulate matter (char, ash) | |
- Oxygenated compounds (acids, alcohols) | |
Impact of Contaminants | - Environmental pollution (air, acid rain, heavy metal accumulation) |
- Operational challenges (fouling, corrosion, increased maintenance costs) | |
- Reduced usability (regulatory restrictions, limited applications) | |
Mitigation Strategies | - Feedstock pre-treatment (sorting, cleaning) |
- Advanced pyrolysis technologies (catalytic pyrolysis) | |
- Post-pyrolysis purification (filtration, distillation, chemical treatment) | |
- Additive removal (neutralizing harmful by-products) | |
Future Directions | - Improved feedstock quality |
- Innovative purification methods (membrane filtration, chemical treatments) | |
- Regulatory standards for pyrolysis oil quality |
Discover how to optimize plastic pyrolysis oil quality—contact our experts today for tailored solutions!