Ball mills are versatile grinding machines used in various industries for size reduction and mixing of materials. They differ in operating principles, design, and capacity, making them suitable for specific applications. The primary types of ball mills include planetary ball mills, mixer mills, vibration mills, and horizontal rolling ball mills. Each type has unique features, such as varying capacities (from small laboratory sizes to several hundred liters) and distinct operating mechanisms. Understanding these differences is crucial for selecting the right ball mill for specific tasks, whether for research, industrial processing, or material synthesis.
Key Points Explained:
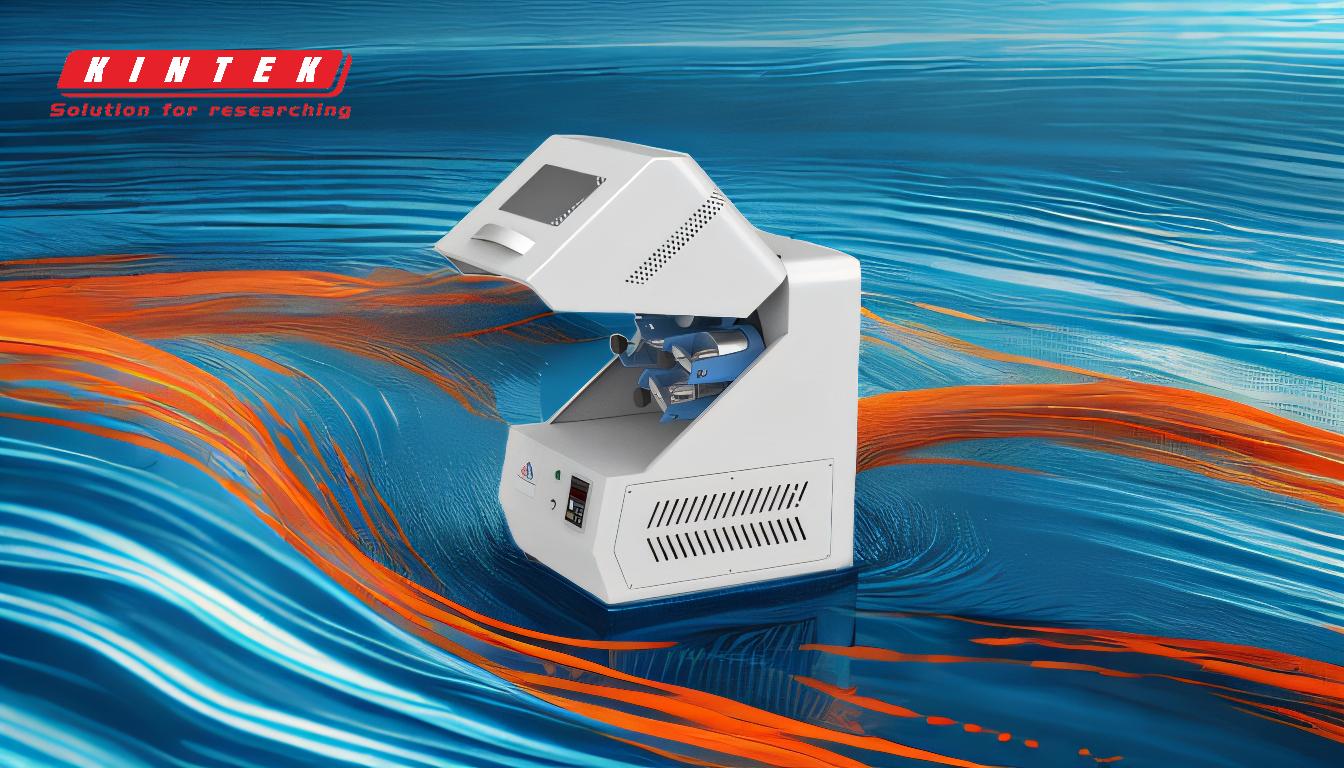
-
Planetary Ball Mills
- Operating Principle: Planetary ball mills consist of one or more grinding jars arranged eccentrically on a rotating platform. The jars rotate around their own axis while simultaneously orbiting the central axis, creating high-energy impacts and friction.
- Applications: Ideal for fine grinding, mechanical alloying, and nanomaterial synthesis due to their high energy input.
- Capacity: Typically used in laboratory settings with small capacities, but some models can handle larger volumes.
- Advantages: High grinding efficiency, uniform particle size distribution, and versatility for various materials.
-
Mixer Mills
- Operating Principle: Mixer mills use high-frequency vibrations to grind materials. The grinding jars oscillate rapidly, causing the grinding balls to impact and grind the sample.
- Applications: Suitable for dry, wet, and cryogenic grinding, often used in laboratories for small-scale sample preparation.
- Capacity: Generally limited to small volumes, making them ideal for research and development.
- Advantages: Fast and efficient grinding, compact design, and ability to handle multiple samples simultaneously.
-
Vibration Mills
- Operating Principle: Vibration mills operate by subjecting the grinding jar to high-frequency vibrations, causing the grinding media to move rapidly and grind the material through impact and friction.
- Applications: Used for fine grinding, mechanical alloying, and mixing of powders in both laboratory and industrial settings.
- Capacity: Available in a range of sizes, from small laboratory mills to larger industrial models.
- Advantages: High grinding speed, uniform particle size, and suitability for both brittle and tough materials.
-
Horizontal Rolling Ball Mills
- Operating Principle: These mills consist of a horizontally rotating cylinder filled with grinding media. The material is ground by the cascading and tumbling action of the balls as the cylinder rotates.
- Applications: Commonly used in industrial settings for large-scale grinding of ores, ceramics, and other materials.
- Capacity: Capable of handling large volumes, with capacities up to several hundred liters.
- Advantages: High throughput, continuous operation, and suitability for wet or dry grinding processes.
-
Key Differences and Selection Criteria
- Energy Input: Planetary and vibration mills provide higher energy input compared to horizontal rolling ball mills, making them suitable for fine grinding and nanomaterial synthesis.
- Capacity: Horizontal rolling ball mills are designed for large-scale industrial applications, while planetary, mixer, and vibration mills are better suited for laboratory and small-scale operations.
- Material Compatibility: The choice of mill depends on the material properties, such as hardness, brittleness, and desired particle size.
- Operational Flexibility: Planetary and mixer mills offer greater flexibility for different grinding conditions (e.g., dry, wet, cryogenic), while horizontal rolling ball mills are more specialized for continuous industrial processes.
By understanding the distinct features and applications of each type of ball mill, purchasers can make informed decisions based on their specific requirements, whether for research, material synthesis, or industrial processing.
Summary Table:
Type | Operating Principle | Applications | Capacity | Advantages |
---|---|---|---|---|
Planetary Ball Mills | Jars rotate eccentrically, creating high-energy impacts and friction. | Fine grinding, mechanical alloying, nanomaterial synthesis. | Small lab sizes to larger volumes. | High efficiency, uniform particle size, versatile for various materials. |
Mixer Mills | High-frequency vibrations cause grinding balls to impact and grind the sample. | Dry, wet, and cryogenic grinding; small-scale sample preparation. | Limited to small volumes. | Fast grinding, compact design, handles multiple samples. |
Vibration Mills | High-frequency vibrations cause rapid movement of grinding media. | Fine grinding, mechanical alloying, powder mixing in labs and industries. | Small lab sizes to larger industrial models. | High speed, uniform particle size, suitable for brittle and tough materials. |
Horizontal Rolling | Horizontally rotating cylinder with grinding media cascades and tumbles to grind. | Large-scale grinding of ores, ceramics, and other materials. | Up to several hundred liters. | High throughput, continuous operation, suitable for wet or dry grinding. |
Need help selecting the right ball mill for your application? Contact our experts today for personalized advice!