Chemical Vapor Deposition (CVD) reactors are categorized based on their operating conditions, such as pressure, temperature, and the method of initiating chemical reactions. The primary types of CVD reactors include Atmospheric Pressure CVD (APCVD), Low-Pressure CVD (LPCVD), Ultrahigh Vacuum CVD (UHVCVD), Sub-atmospheric CVD (SACVD), Plasma-Enhanced CVD (PECVD), and others like Aerosol-Assisted CVD and Direct Liquid Injection CVD. Additionally, reactors are classified into hot wall and cold wall types based on their heating mechanisms. Each type of CVD reactor has specific applications, advantages, and disadvantages, making them suitable for different materials and deposition processes.
Key Points Explained:
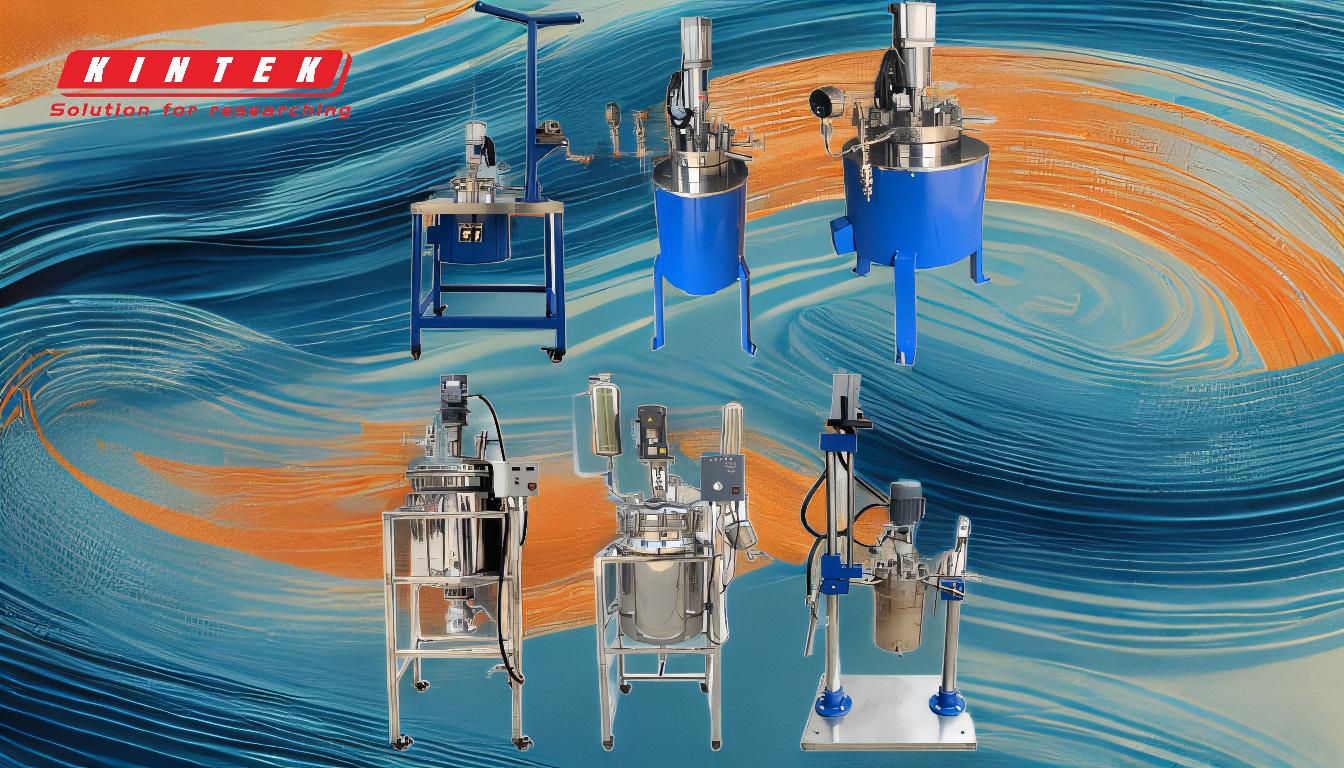
-
Atmospheric Pressure CVD (APCVD):
- Definition: CVD conducted at atmospheric pressure.
- Applications: Commonly used for depositing materials like silicon dioxide and silicon nitride.
- Advantages: Simplicity and cost-effectiveness due to the absence of vacuum systems.
- Disadvantages: Limited control over film uniformity and quality due to higher pressure.
-
Low-Pressure CVD (LPCVD):
- Definition: CVD conducted at sub-atmospheric pressures.
- Applications: Used for depositing materials like polysilicon, silicon nitride, and silicon dioxide.
- Advantages: Better film uniformity and quality due to lower pressure.
- Disadvantages: Requires more complex equipment and higher costs due to vacuum systems.
-
Ultrahigh Vacuum CVD (UHVCVD):
- Definition: CVD conducted at very low pressures, typically below 10^-6 Pa.
- Applications: Suitable for high-purity materials and epitaxial growth.
- Advantages: Extremely high purity and control over film properties.
- Disadvantages: High equipment costs and complexity.
-
Sub-atmospheric CVD (SACVD):
- Definition: CVD conducted at pressures between atmospheric and low-pressure ranges.
- Applications: Used for materials that require moderate pressure conditions.
- Advantages: Balances between the simplicity of APCVD and the control of LPCVD.
- Disadvantages: Moderate equipment complexity and cost.
-
Plasma-Enhanced CVD (PECVD):
- Definition: CVD that uses plasma to activate chemical reactions.
- Applications: Used for depositing materials like silicon nitride and amorphous silicon.
- Advantages: Lower deposition temperatures and faster deposition rates.
- Disadvantages: Requires plasma generation equipment and can introduce impurities.
-
Aerosol-Assisted CVD (AACVD):
- Definition: CVD that uses an aerosol to transport precursors.
- Applications: Suitable for materials that are difficult to vaporize.
- Advantages: Easier precursor transport and use.
- Disadvantages: Limited control over aerosol size and distribution.
-
Direct Liquid Injection CVD (DLI-CVD):
- Definition: CVD that involves injecting a liquid precursor into a heated chamber.
- Applications: Used for materials that are difficult to vaporize.
- Advantages: Precise control over precursor delivery.
- Disadvantages: Requires precise control over injection parameters.
-
Hot Wall Reactors:
- Definition: Reactors where the entire chamber is heated.
- Applications: Suitable for uniform heating and large-scale production.
- Advantages: Uniform temperature distribution.
- Disadvantages: Higher energy consumption and potential for contamination.
-
Cold Wall Reactors:
- Definition: Reactors where only the substrate is heated.
- Applications: Suitable for processes requiring localized heating.
- Advantages: Lower energy consumption and reduced contamination.
- Disadvantages: Less uniform temperature distribution.
-
Other CVD Types:
- High Temperature CVD: Used for depositing materials like silicon or titanium nitride at high temperatures.
- Low Temperature CVD: Used for depositing insulating layers like silicon dioxide at low temperatures.
- Photo Assisted CVD: Uses photons from a laser to activate chemical reactions.
- Metalorganic CVD (MOCVD): Uses metalorganic precursors for depositing compound semiconductors.
Each type of CVD reactor and process has its unique set of applications, advantages, and disadvantages, making them suitable for specific materials and deposition requirements. Understanding these differences is crucial for selecting the appropriate CVD method for a given application.
Summary Table:
Type | Applications | Advantages | Disadvantages |
---|---|---|---|
APCVD | Silicon dioxide, silicon nitride | Simple, cost-effective | Limited film uniformity |
LPCVD | Polysilicon, silicon nitride, silicon dioxide | Better film uniformity, quality | Complex equipment, higher costs |
UHVCVD | High-purity materials, epitaxial growth | Extremely high purity, precise control | High equipment costs, complexity |
SACVD | Moderate pressure materials | Balances simplicity and control | Moderate complexity, cost |
PECVD | Silicon nitride, amorphous silicon | Lower temperatures, faster deposition | Plasma equipment, potential impurities |
AACVD | Hard-to-vaporize materials | Easier precursor transport | Limited control over aerosol size |
DLI-CVD | Hard-to-vaporize materials | Precise precursor delivery | Requires precise injection control |
Hot Wall Reactors | Uniform heating, large-scale production | Uniform temperature distribution | High energy use, contamination risk |
Cold Wall Reactors | Localized heating processes | Lower energy use, reduced contamination | Less uniform temperature distribution |
Need help selecting the right CVD reactor for your application? Contact our experts today for personalized guidance!