Grinding balls are essential components in grinding mills, used to crush and grind materials into fine powders. They are widely used in industries such as mining, cement, and chemical processing. The type of grinding ball selected depends on factors like material hardness, grinding efficiency, and cost. Common types include forged steel balls, cast iron balls, and ceramic balls, each with unique properties and applications. Forged steel balls are durable and suitable for high-impact grinding, while cast iron balls are cost-effective for less demanding tasks. Ceramic balls are ideal for applications requiring high purity and corrosion resistance. Understanding these differences helps in selecting the right grinding ball for specific industrial needs.
Key Points Explained:
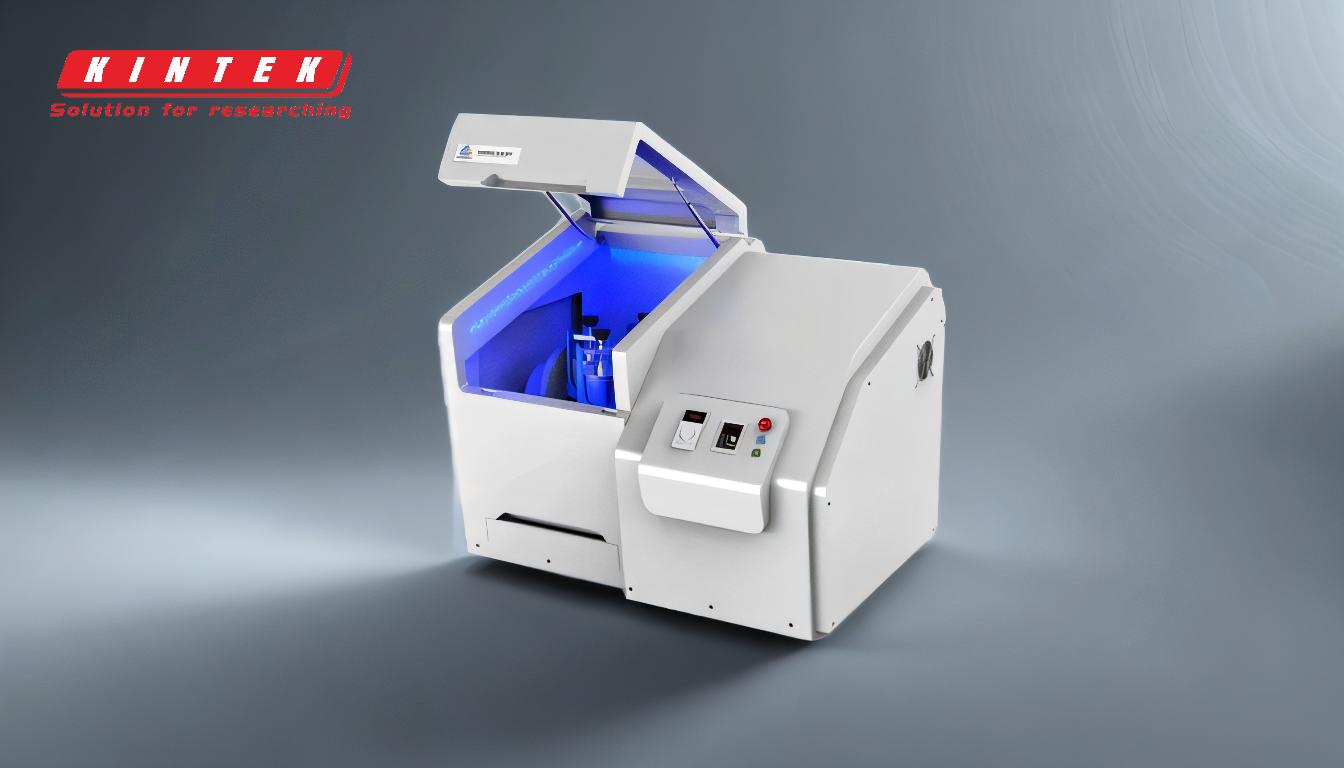
-
Forged Steel Grinding Balls:
- Material Composition: Made from high-quality steel, forged steel grinding balls are known for their high hardness and toughness.
- Manufacturing Process: These balls are produced through a forging process, which involves heating the steel to a high temperature and then shaping it under high pressure. This process enhances the density and strength of the balls.
- Applications: Forged steel balls are ideal for high-impact grinding operations, such as in mining and cement industries. They are particularly effective in grinding hard materials like ores and minerals.
- Advantages: High durability, excellent wear resistance, and ability to withstand high-impact forces.
- Disadvantages: Higher cost compared to cast iron balls, but the extended lifespan often justifies the investment.
-
Cast Iron Grinding Balls:
- Material Composition: Cast iron grinding balls are made from cast iron, which is an alloy of iron, carbon, and silicon. They are generally less hard than forged steel balls but are more cost-effective.
- Manufacturing Process: These balls are produced through a casting process, where molten iron is poured into molds and allowed to cool and solidify.
- Applications: Suitable for less demanding grinding tasks, such as in the cement industry or for grinding softer materials. They are often used in ball mills for grinding clinker and raw materials in cement production.
- Advantages: Lower cost, good wear resistance for less abrasive materials, and ease of production.
- Disadvantages: Lower hardness and toughness compared to forged steel balls, making them less suitable for high-impact grinding.
-
Ceramic Grinding Balls:
- Material Composition: Ceramic grinding balls are made from high-purity ceramic materials, such as alumina or zirconia. These materials are known for their high hardness and chemical inertness.
- Manufacturing Process: Ceramic balls are produced through a process that includes shaping, drying, and sintering at high temperatures. This process results in a dense and hard product.
- Applications: Ideal for applications requiring high purity and corrosion resistance, such as in the pharmaceutical, food, and chemical industries. They are also used in grinding processes where contamination from metal particles must be avoided.
- Advantages: High purity, excellent corrosion resistance, and low wear rate. They are also non-magnetic and non-conductive, making them suitable for specialized applications.
- Disadvantages: Higher cost and lower impact resistance compared to metal balls, making them less suitable for high-impact grinding.
-
Other Types of Grinding Balls:
- Stainless Steel Balls: These are used in applications where corrosion resistance is critical. They are less common but are used in specialized industries like food processing and pharmaceuticals.
- Chrome Steel Balls: Known for their high hardness and wear resistance, these balls are often used in precision grinding applications.
- High Carbon Steel Balls: These balls offer a balance between hardness and cost, making them suitable for general-purpose grinding.
-
Selection Criteria:
- Material Hardness: The hardness of the grinding ball should match the hardness of the material being ground to ensure efficient grinding and minimize wear.
- Grinding Efficiency: The size and density of the grinding balls affect the grinding efficiency. Larger balls are used for coarse grinding, while smaller balls are used for fine grinding.
- Cost: The cost of grinding balls varies depending on the material and manufacturing process. It's important to balance cost with performance and lifespan.
- Application Requirements: Specific industries may have unique requirements, such as the need for high purity or corrosion resistance, which will influence the choice of grinding balls.
-
Maintenance and Lifespan:
- Wear and Tear: Grinding balls are subject to wear and tear during operation. Regular inspection and replacement are necessary to maintain grinding efficiency.
- Replacement Frequency: The frequency of replacement depends on the type of grinding ball and the operating conditions. Forged steel balls generally have a longer lifespan compared to cast iron balls.
- Cost-Benefit Analysis: While some grinding balls may have a higher initial cost, their longer lifespan and reduced maintenance requirements can result in lower overall costs.
In conclusion, the selection of grinding balls is a critical decision that impacts the efficiency and cost-effectiveness of grinding operations. Understanding the different types of grinding balls and their properties allows for informed decision-making, ensuring optimal performance and cost savings in industrial applications.
Summary Table:
Type | Material Composition | Applications | Advantages | Disadvantages |
---|---|---|---|---|
Forged Steel Balls | High-quality steel | Mining, cement (high-impact grinding) | High durability, wear resistance | Higher cost |
Cast Iron Balls | Cast iron (iron, carbon, silicon) | Cement, softer materials (less demanding tasks) | Cost-effective, good wear resistance | Lower hardness, less suitable for high-impact |
Ceramic Balls | Alumina, zirconia | Pharmaceutical, food, chemical (high purity) | High purity, corrosion resistance | Higher cost, lower impact resistance |
Need help selecting the right grinding balls for your application? Contact our experts today for personalized advice!