Pyrolysis reactors are critical components in the thermal decomposition of organic materials in the absence of oxygen. The choice of reactor type significantly influences the efficiency, yield, and quality of the pyrolysis products. Common reactor types include fluidized bed, fixed bed, rotary kiln, vacuum, circulating, ablative, auger, and cyclonic reactors, among others. Each type has unique characteristics, such as heat transfer efficiency, residence time, and processing capacity, which make them suitable for specific applications. Understanding the differences between these reactors is essential for selecting the right system based on the feedstock, desired products, and operational requirements.
Key Points Explained:
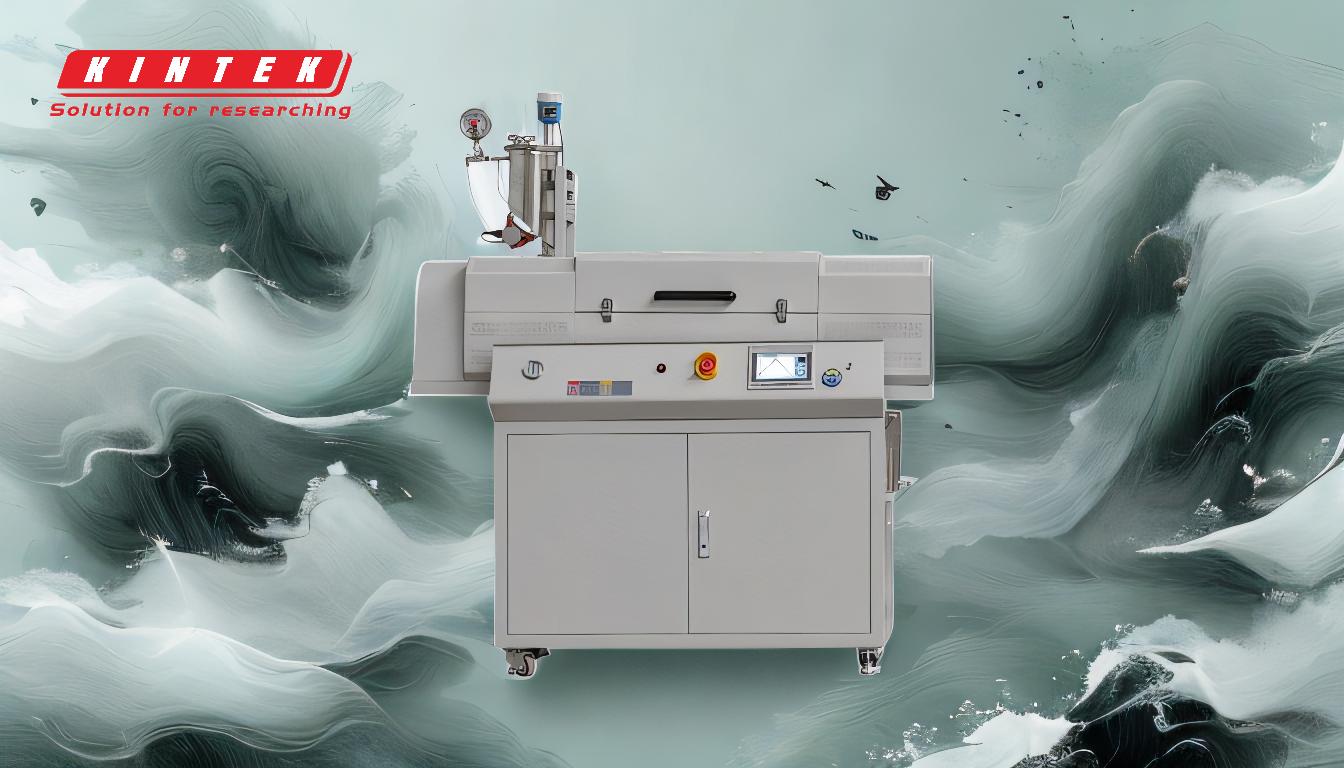
-
Fluidized Bed Reactors:
- Bubbling Fluidized Bed: This type uses a bed of inert particles (like sand) fluidized by a gas stream. The feedstock is introduced into the bed, where it undergoes rapid heating and decomposition. It offers excellent heat transfer and uniform temperature distribution, making it suitable for continuous operation.
- Circulating Fluidized Bed: Similar to the bubbling fluidized bed but with higher gas velocities, causing the particles to circulate continuously. This design enhances heat transfer and allows for larger-scale operations.
- Advantages: High heat transfer rates, short residence time, and scalability.
- Applications: Commonly used for biomass pyrolysis and waste-to-energy processes.
-
Fixed Bed Reactors:
- Design: The feedstock is placed in a stationary bed, and heat is applied either directly or indirectly. The pyrolysis products are collected as gases, liquids, or solids.
- Advantages: Simple design, low operating costs, and suitability for small-scale operations.
- Disadvantages: Limited heat transfer efficiency and longer residence times.
- Applications: Often used for slow pyrolysis processes, such as charcoal production.
-
Rotary Kiln Reactors:
- Design: A cylindrical vessel that rotates to mix the feedstock and expose it to heat. The rotation ensures even heating and prevents material from sticking to the walls.
- Advantages: Indirect heating reduces contamination risk, and the design is suitable for handling heterogeneous feedstocks.
- Applications: Widely used for pyrolysis of plastics, tires, and other waste materials.
-
Vacuum Reactors:
- Design: Operates under reduced pressure to lower the boiling points of volatile compounds, facilitating their removal at lower temperatures.
- Advantages: Reduces thermal degradation of sensitive compounds and improves the quality of pyrolysis oil.
- Applications: Suitable for producing high-quality bio-oil from biomass.
-
Ablative Reactors:
- Design: The feedstock is pressed against a hot surface, causing rapid heating and decomposition. The process is driven by mechanical force rather than gas flow.
- Advantages: High heating rates, short residence times, and minimal gas flow requirements.
- Applications: Ideal for processing large particles or feedstocks with high moisture content.
-
Auger (Screw) Reactors:
- Design: Uses a screw mechanism to transport the feedstock through a heated chamber, ensuring continuous processing.
- Advantages: Compact design, continuous operation, and suitability for small-scale applications.
- Applications: Often used for pyrolysis of agricultural residues and municipal waste.
-
Cyclonic Reactors:
- Design: Utilizes centrifugal force to separate pyrolysis products based on their density. The feedstock is introduced into a high-speed gas stream, causing rapid heating and decomposition.
- Advantages: High throughput, short residence times, and efficient separation of products.
- Applications: Suitable for fast pyrolysis processes.
-
Batch and Semi-Batch Reactors:
- Batch Reactors: Operate in a closed system where the feedstock is loaded, processed, and then unloaded in cycles.
- Semi-Batch Reactors: Allow for continuous feeding or removal of certain components while maintaining a closed system.
- Advantages: Flexibility in operation and suitability for small-scale or experimental setups.
- Disadvantages: Lower efficiency and scalability compared to continuous systems.
-
Other Reactor Types:
- Tubular Reactors: Use a series of tubes to heat the feedstock, offering precise temperature control.
- Heinz Retort: A specialized reactor for producing high-quality charcoal.
- Wire Mesh Reactors: Used for fast pyrolysis of small particles, offering rapid heating and short residence times.
- Entrained-Flow Reactors: Similar to cyclonic reactors but designed for even higher gas velocities, suitable for gasification processes.
-
Factors Influencing Reactor Selection:
- Feedstock Type: The physical and chemical properties of the feedstock, such as particle size, moisture content, and composition, influence the choice of reactor.
- Product Requirements: The desired yield and quality of pyrolysis products (bio-oil, syngas, or biochar) determine the optimal reactor design.
- Operational Scale: Continuous reactors are preferred for large-scale operations, while batch reactors are suitable for small-scale or experimental setups.
- Heat Transfer Efficiency: Reactors with high heat transfer rates, such as fluidized beds, are ideal for fast pyrolysis processes.
- Residence Time: The time the feedstock spends in the reactor affects the degree of decomposition and product composition.
In conclusion, the selection of a pyrolysis reactor depends on various factors, including the type of feedstock, desired products, and operational requirements. Each reactor type offers unique advantages and limitations, making it essential to evaluate these factors carefully to achieve optimal performance and product quality.
Summary Table:
Reactor Type | Key Features | Applications |
---|---|---|
Fluidized Bed | High heat transfer, short residence time, scalable | Biomass pyrolysis, waste-to-energy |
Fixed Bed | Simple design, low operating costs, suitable for small-scale operations | Charcoal production, slow pyrolysis |
Rotary Kiln | Indirect heating, handles heterogeneous feedstocks | Plastics, tires, and waste pyrolysis |
Vacuum | Operates under reduced pressure, improves bio-oil quality | High-quality bio-oil production |
Ablative | High heating rates, minimal gas flow requirements | Large particles, high-moisture feedstocks |
Auger (Screw) | Compact design, continuous operation, small-scale applications | Agricultural residues, municipal waste |
Cyclonic | High throughput, efficient product separation | Fast pyrolysis processes |
Batch/Semi-Batch | Flexible operation, suitable for small-scale or experimental setups | Experimental or small-scale pyrolysis |
Need help selecting the right pyrolysis reactor for your application? Contact our experts today for tailored solutions!