Bead milling, while effective for particle size reduction, has several disadvantages that can impact its suitability for certain applications. These include challenges related to heat and shear sensitivity, uneven medium distribution, low grinding efficiency, and difficulties in starting the mill under load. Additionally, bead mills may introduce mechanical anomalies, especially when processing heat-sensitive materials. These limitations make it crucial to carefully evaluate the specific requirements of the material and process before opting for bead milling.
Key Points Explained:
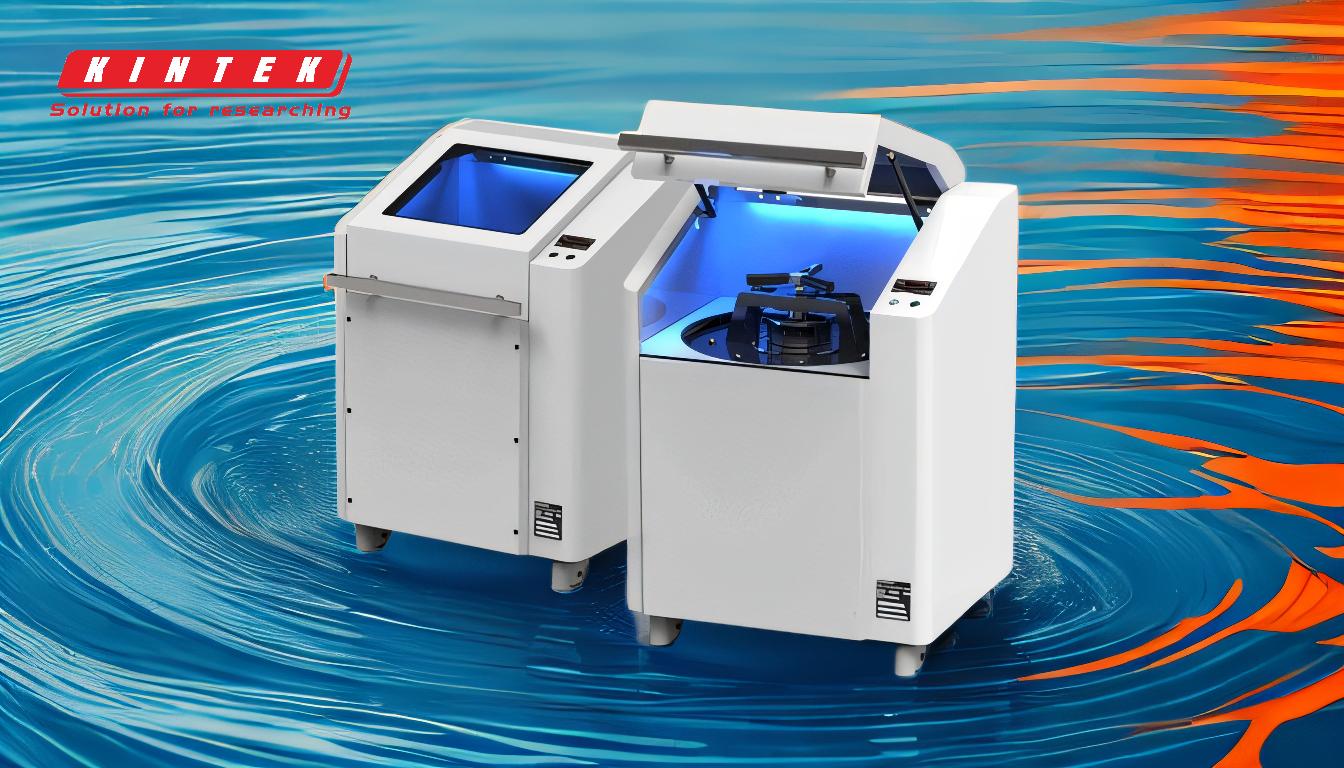
-
Heat and Shear Sensitivity:
- Bead milling can generate heat and shear forces, which may adversely affect heat-sensitive materials such as foods and pharmaceuticals. This can lead to degradation or alteration of the material's chemical properties.
- Impact: For industries requiring precise control over material integrity, such as pharmaceuticals, this can be a significant drawback, necessitating alternative methods like cryogenic grinding or jet milling.
-
Uneven Medium Distribution:
- In vertical bead mills, the distribution of grinding media (beads) can be uneven, leading to inconsistent particle size reduction.
- Impact: This inconsistency can result in a non-uniform product, which may not meet the desired specifications, especially in applications requiring tight particle size distributions.
-
Low Grinding Efficiency:
- The efficiency of grinding technology in bead mills can be relatively low, particularly when compared to other methods like jet milling.
- Impact: Lower efficiency means longer processing times and higher energy consumption, which can increase operational costs and reduce throughput.
-
Difficulty in Starting Under Load:
- Bead mills can be challenging to start when under load, which can complicate the milling process and require additional operational adjustments.
- Impact: This can lead to delays in production and increased wear and tear on the equipment, potentially reducing its lifespan and increasing maintenance costs.
-
Mechanical Anomalies:
- The mechanical action of bead milling can introduce anomalies, particularly in materials that are sensitive to mechanical stress.
- Impact: This can result in undesirable changes to the material's properties, such as altered texture or reduced stability, which can be critical in applications like food processing or pharmaceutical manufacturing.
-
Structural Limitations:
- While bead mills have the advantage of a simple structure and the absence of mechanical seals, this can also be a limitation in terms of scalability and adaptability to different processing needs.
- Impact: The simplicity of the design may limit the ability to customize or upgrade the equipment for specific applications, potentially restricting its use in more complex or demanding processes.
In summary, while bead milling offers certain advantages, its disadvantages—particularly in terms of heat sensitivity, uneven medium distribution, low efficiency, and mechanical anomalies—make it essential to carefully consider the specific requirements of the material and process before selecting this method. Alternative methods like jet milling or cryogenic grinding may be more suitable for certain applications, despite their own set of challenges.
Summary Table:
Disadvantage | Impact |
---|---|
Heat and Shear Sensitivity | Degradation of heat-sensitive materials, affecting industries like pharma. |
Uneven Medium Distribution | Inconsistent particle size, leading to non-uniform products. |
Low Grinding Efficiency | Longer processing times, higher energy costs, and reduced throughput. |
Difficulty Starting Under Load | Delays in production and increased equipment wear. |
Mechanical Anomalies | Altered material properties, critical for food and pharma applications. |
Structural Limitations | Limited scalability and adaptability for complex processes. |
Need help choosing the right milling method? Contact our experts today for tailored solutions!