Diamond-like carbon (DLC) coatings are widely used for their excellent wear resistance, low friction, and chemical inertness. However, they also have several disadvantages, including limitations in processing temperatures, challenges in application due to high-temperature requirements, and issues related to stress, cracking, and coating uniformity. Additionally, DLC coatings may not be suitable for all materials or applications, particularly those involving interrupted cutting processes or requiring precise masking. These factors can limit their effectiveness and applicability in certain industrial contexts.
Key Points Explained:
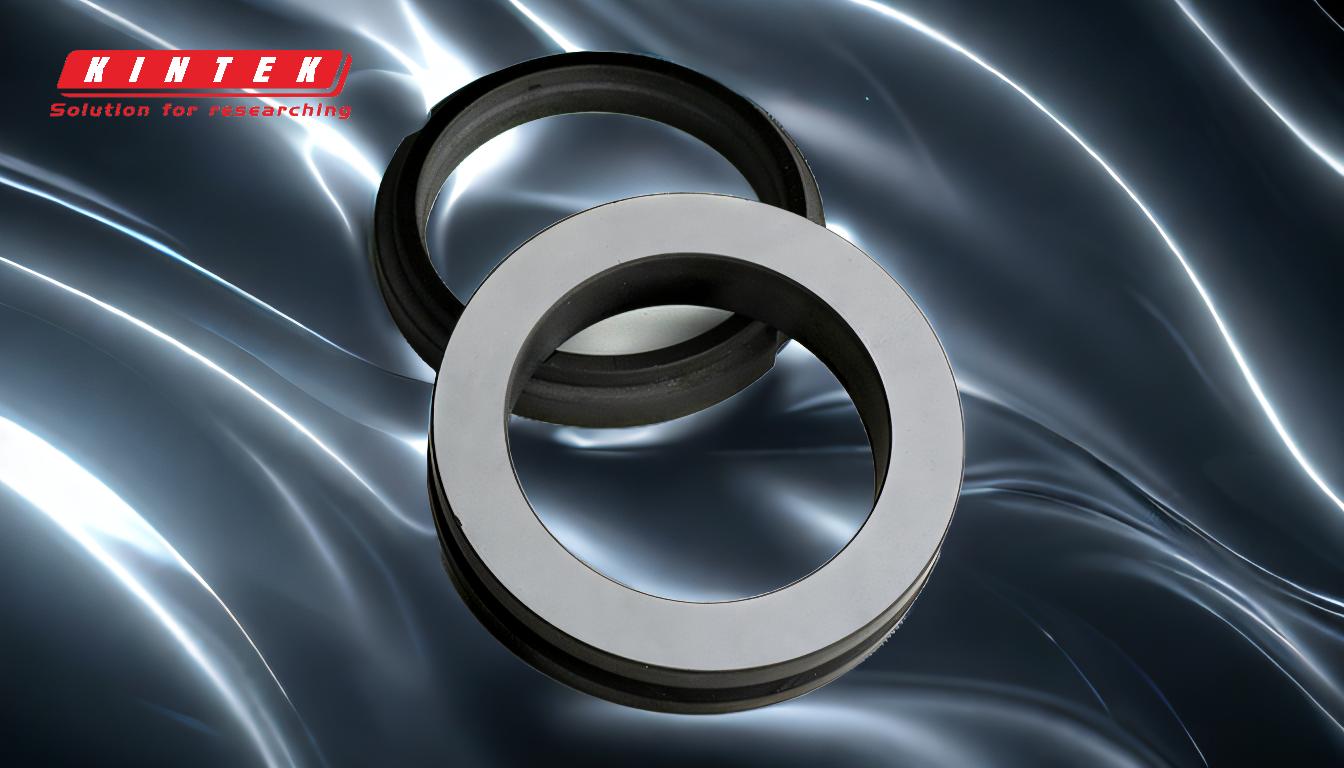
-
High Processing Temperatures:
- DLC coatings, particularly those applied via chemical vapor deposition (CVD), require high processing temperatures (800–1000°C or 1875–1925°F). This limits their use to materials that can withstand such heat, such as cemented carbide. Many substrates, especially those with lower melting points or thermal stability, cannot tolerate these conditions, restricting the range of applications for DLC coatings.
-
Tensile Stress and Cracking:
- The thick nature of CVD coatings (10–20 μm) can lead to tensile stress during cooling. This stress often results in fine cracks that may propagate under external impact, causing the coating to peel off. This makes DLC coatings less suitable for applications involving interrupted cutting processes, such as milling, where the coating is more prone to failure.
-
Limitations in Masking and Coating Uniformity:
- CVD processes make it difficult to mask specific areas, often resulting in an all-or-nothing coating. This lack of precision can be problematic for applications requiring selective coating. Additionally, the size of parts that can be coated is limited by the reaction chamber capacity, and parts must often be disassembled into individual components for coating.
-
Non-Uniform Grain Structure and Surface Roughness:
- The grain structure of CVD diamond coatings is non-uniform due to the growth process, and the surface roughness evolves with thickness. This necessitates polishing for applications requiring smooth surfaces, such as thermal spreaders. The non-uniformity can also affect the mechanical and thermal properties of the coating.
-
Metastable Nature and Bonding Variability:
- DLC is a metastable form of amorphous or hydrogenated amorphous carbon, containing a mix of sp2 and sp3 bonds. The properties of the film depend on the ratio of these bonds, which can vary significantly. This variability can lead to inconsistencies in hardness, wear resistance, and other critical properties, making it challenging to achieve uniform performance across different coatings.
-
Limited Suitability for Interrupted Cutting Processes:
- Due to the propensity for cracking and peeling under stress, DLC coatings are less effective in interrupted cutting processes like milling. The repeated impact and thermal cycling in such processes can exacerbate coating failure, limiting their use in these applications.
-
Logistical Challenges:
- The CVD process is not an "on-site" process, meaning parts must be shipped to specialized coating centers. This adds logistical complexity, cost, and time to the production process, particularly for large or complex components.
-
Chemical and Wear Resistance Trade-offs:
- While DLC coatings are known for their excellent wear and chemical resistance, these properties can vary depending on the deposition technique and the specific composition of the coating. In some cases, achieving optimal wear resistance may come at the expense of other desirable properties, such as adhesion or thermal conductivity.
In summary, while DLC coatings offer significant advantages in terms of durability, friction reduction, and chemical resistance, their high processing temperatures, susceptibility to stress and cracking, and limitations in masking and uniformity present notable disadvantages. These factors must be carefully considered when selecting DLC coatings for specific applications.
Summary Table:
Disadvantage | Description |
---|---|
High Processing Temperatures | Requires 800–1000°C, limiting use to heat-resistant materials like cemented carbide. |
Tensile Stress and Cracking | Thick coatings lead to stress-induced cracks, making them unsuitable for interrupted cutting processes. |
Masking and Coating Uniformity | CVD processes lack precision in masking, resulting in all-or-nothing coatings. |
Non-Uniform Grain Structure | Grain structure and surface roughness vary, requiring polishing for smooth applications. |
Metastable Nature and Bonding Variability | Properties depend on sp2/sp3 bond ratios, leading to inconsistent hardness and wear resistance. |
Limited Suitability for Interrupted Cutting | Prone to failure in milling and similar processes due to stress and thermal cycling. |
Logistical Challenges | Parts must be shipped to specialized centers, adding time and cost. |
Chemical and Wear Resistance Trade-offs | Optimal wear resistance may compromise adhesion or thermal conductivity. |
Need help determining if DLC coatings are right for your application? Contact our experts today for tailored advice!