Flash pyrolysis, while offering high bio-oil yields (up to 75–80 wt%), faces several significant disadvantages that hinder its widespread adoption. These include high operational and investment costs, challenges in controlling the process due to the rapid heating rates, and the production of toxic by-products and hazardous waste. Additionally, the process requires sophisticated equipment and monitoring systems, making it difficult to scale up and apply in real-world conditions. The need for efficient separation and purification of end products, as well as the accumulation of metal and ash in reactor bed materials, further complicates the process. These factors collectively limit the economic feasibility and environmental sustainability of flash pyrolysis.
Key Points Explained:
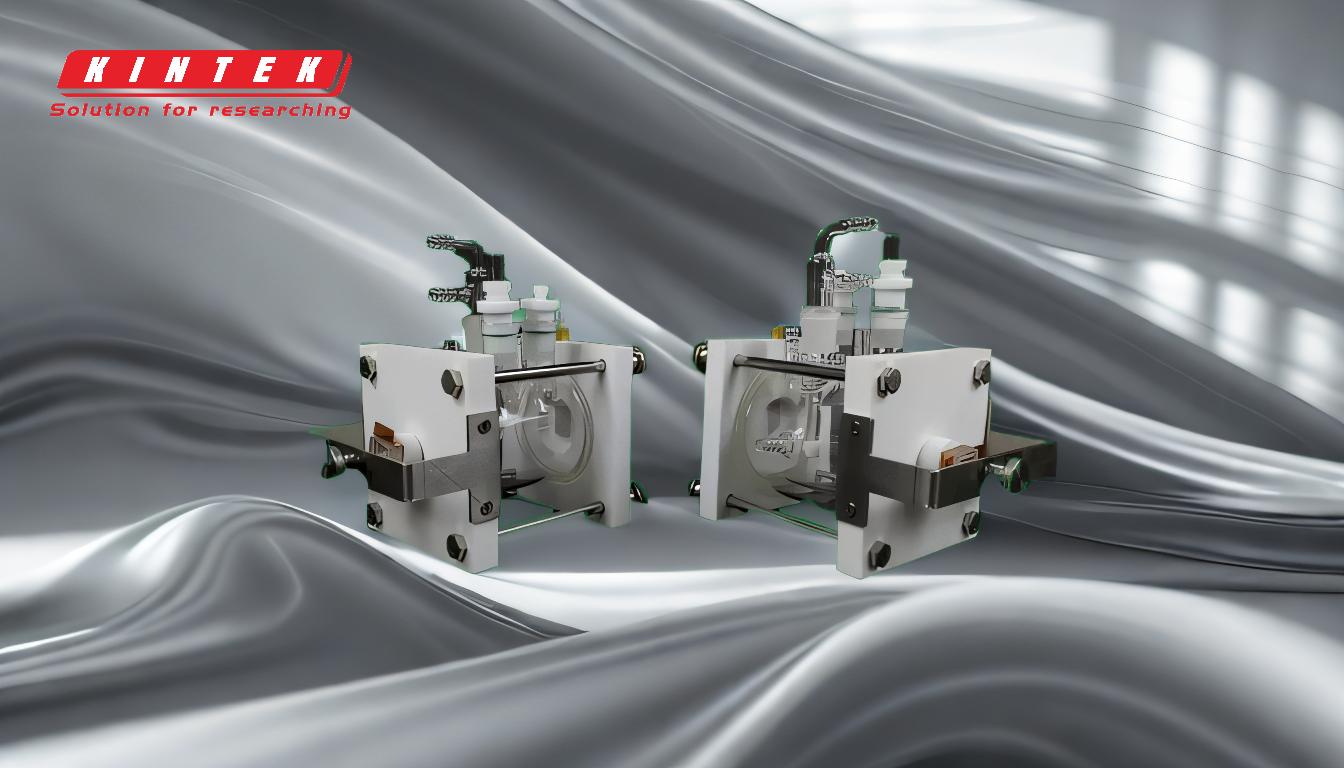
-
High Operational and Investment Costs:
- Flash pyrolysis requires advanced and expensive equipment to achieve the high heating rates necessary for optimal bio-oil yields.
- The process demands sophisticated monitoring and auto-adjusting systems to maintain control over the rapid reactions, further increasing costs.
- The economic viability of flash pyrolysis is often questioned due to these high initial and ongoing expenses.
-
Difficulty in Controlling the Process:
- The rapid heating rates in flash pyrolysis make it challenging to control the types and quality of decomposition products.
- Organic materials, which are poor heat conductors, complicate temperature control throughout the feedstock, leading to uneven heating and potential process inefficiencies.
- The process is particularly difficult to manage when the feedstock contains materials like plastic or rubber, which become sticky when heated, further disrupting continuous processing.
-
Production of Toxic By-Products and Hazardous Waste:
- Flash pyrolysis generates a significant amount of toxic by-products, which require careful handling and disposal.
- The process produces ashes with high heavy metal content, classified as dangerous waste, necessitating costly air purification installations to treat flue gases.
- The environmental impact of these by-products and waste materials poses a significant challenge to the sustainability of the process.
-
Challenges in Scaling and Real-World Application:
- The technology's limited global adoption and the difficulty in treating variable feed materials, such as municipal solid waste (MSW), hinder its scalability.
- Continuous processing, essential for economic efficiency, is difficult to achieve due to the uneven heating and handling of moving materials.
- These factors make it challenging to implement flash pyrolysis on a large scale, limiting its practical application in real-world scenarios.
-
Accumulation of Metal and Ash in Reactor Bed Materials:
- The accumulation of metal and ash in reactor bed materials can impede the pyrolysis process, reducing bio-oil yields and overall efficiency.
- This issue necessitates frequent maintenance and cleaning of the reactor, adding to the operational costs and downtime.
-
Need for Efficient Separation and Purification of End Products:
- Flash pyrolysis produces a mixture of bio-oil, bio-char, and syngas, which require efficient separation and purification to be usable.
- The complexity and cost of these downstream processes further detract from the overall economic feasibility of the technology.
In summary, while flash pyrolysis offers the potential for high bio-oil yields, its disadvantages—ranging from high costs and process control challenges to environmental and scalability issues—present significant barriers to its widespread adoption and practical application. Addressing these challenges is crucial for realizing the full potential of flash pyrolysis as a sustainable and economically viable technology.
Summary Table:
Disadvantage | Key Challenges |
---|---|
High Operational and Investment Costs | Expensive equipment, sophisticated monitoring systems, and high ongoing expenses. |
Difficulty in Controlling the Process | Rapid heating rates, uneven heating, and challenges with sticky feed materials. |
Toxic By-Products and Hazardous Waste | Heavy metal ashes, dangerous waste, and costly air purification requirements. |
Challenges in Scaling and Application | Limited global adoption, difficulty in treating variable feed materials. |
Metal and Ash Accumulation | Frequent maintenance, reduced efficiency, and increased downtime. |
Separation and Purification Needs | Complex and costly downstream processes for bio-oil, bio-char, and syngas. |
Interested in overcoming the challenges of flash pyrolysis? Contact our experts today for tailored solutions!