Hot isostatic pressing (HIP) is a manufacturing process that improves material properties by applying high temperature and pressure uniformly in all directions. While it offers significant advantages such as enhanced mechanical properties and the ability to produce high-density components, it also comes with several disadvantages. These include high equipment and production costs, limited target size due to equipment constraints, low production efficiency, and challenges in temperature control. Additionally, HIP requires specialized skills for operation and may not be compatible with certain powder materials, further limiting its applicability.
Key Points Explained:
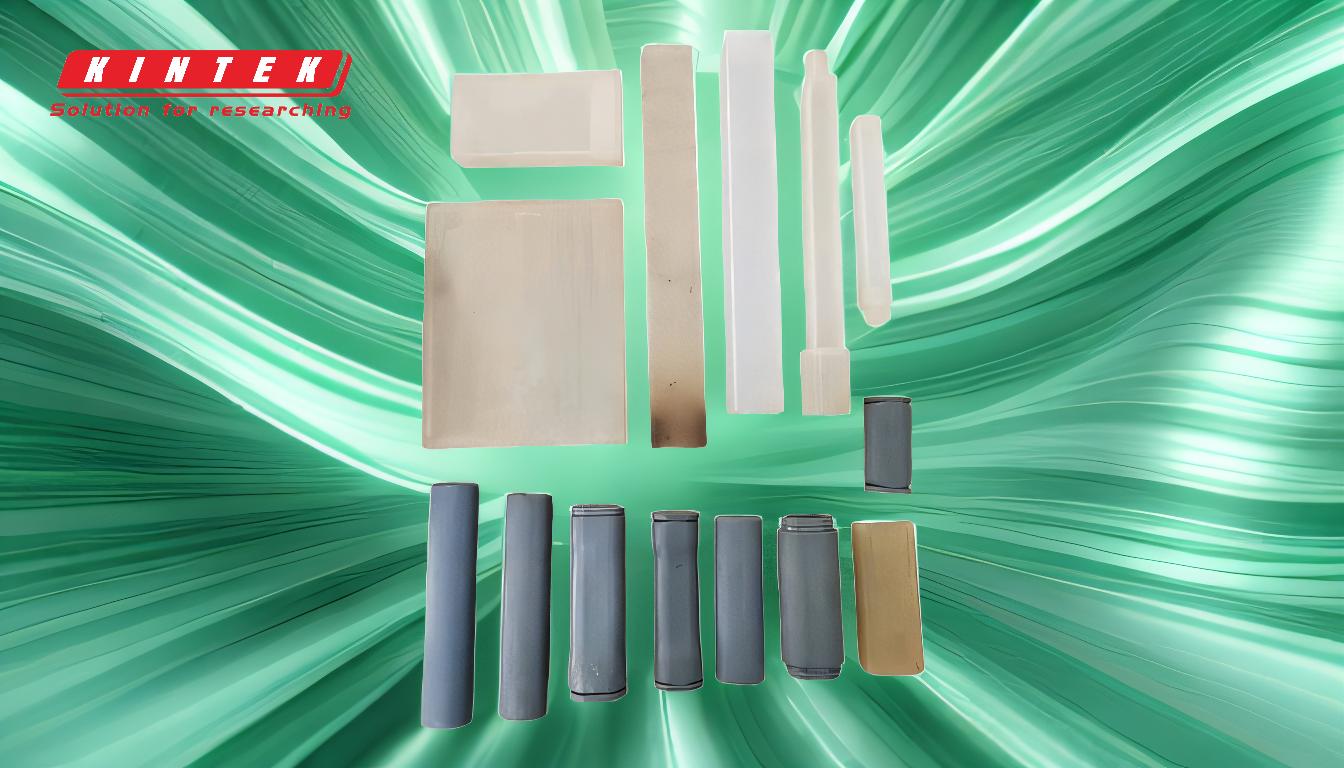
-
High Equipment and Production Costs:
- HIP equipment is expensive to purchase and maintain, requiring significant initial investment.
- The process itself is costly due to the need for high temperatures and pressures, as well as specialized materials like spray-dried powders.
- These costs make HIP less competitive compared to other sintering methods, especially for large-scale production.
-
Limited Target Size:
- The size of components that can be processed using HIP is constrained by the pressure and size of the equipment's working cylinder.
- This limitation makes it difficult to produce large-sized targets, restricting the application of HIP in industries requiring large components.
-
Low Production Efficiency:
- HIP has relatively low production rates compared to methods like extrusion or die compaction.
- The process is time-consuming, which further reduces its efficiency and increases production costs.
-
Challenges in Temperature Control:
- Precise temperature control is difficult due to the heating of the pressure medium caused by friction and supercharging.
- Ensuring uniform temperature distribution within the working cylinder is also challenging, which can affect the quality of the final product.
-
Specialized Skill Requirements:
- Operating HIP equipment requires a skilled workforce, which may not be readily available.
- The complexity of the process necessitates specialized training, adding to the overall cost and limiting its adoption in some regions.
-
Material Compatibility Issues:
- Powders processed using HIP are often not compatible with melting processes, either requiring excessively high temperatures or resulting in unfavorable microstructures.
- This limitation restricts the range of materials that can be effectively processed using HIP.
-
Surface Accuracy and Machining Requirements:
- The surfaces of components pressed adjacent to the flexible bag in HIP have lower accuracy compared to mechanical pressing or extrusion.
- This often necessitates additional machining, increasing the overall production time and cost.
-
High Initial Cost and Investment:
- The initial cost of setting up an HIP facility is high, including the cost of the press, auxiliary equipment, and infrastructure.
- This high initial investment can be a barrier for smaller companies or those with limited budgets.
In summary, while HIP offers significant advantages in terms of material properties and component quality, its disadvantages—such as high costs, limited size, low efficiency, and specialized skill requirements—make it less suitable for certain applications. These factors should be carefully considered when evaluating the use of HIP in manufacturing processes.
Summary Table:
Disadvantage | Explanation |
---|---|
High Equipment and Production Costs | Expensive equipment, high maintenance, and costly process materials. |
Limited Target Size | Restricted by equipment size, making large components difficult to produce. |
Low Production Efficiency | Time-consuming process with slower production rates compared to other methods. |
Challenges in Temperature Control | Difficulty in maintaining precise and uniform temperature distribution. |
Specialized Skill Requirements | Requires skilled operators and specialized training, increasing costs. |
Material Compatibility Issues | Limited compatibility with certain powder materials, restricting applications. |
Surface Accuracy and Machining | Lower surface accuracy often requires additional machining, increasing costs. |
High Initial Cost and Investment | Significant upfront investment in equipment and infrastructure. |
Considering HIP for your manufacturing process? Contact our experts today to discuss your needs!