Isostatic pressing, while advantageous for producing high-density and complex-shaped components, has several notable disadvantages. These include lower accuracy of pressed surfaces adjacent to the flexible bag, necessitating additional machining; the requirement for relatively expensive spray-dried powder in fully automatic dry bag presses; and lower production rates compared to methods like extrusion or die compaction. Additionally, wet-bag isostatic pressing suffers from decreased productivity due to manual loading/unloading of molds, limited automation, and higher tooling costs. These drawbacks increase production time, cost, and complexity, making isostatic pressing less suitable for high-volume or precision-critical applications compared to alternative methods.
Key Points Explained:
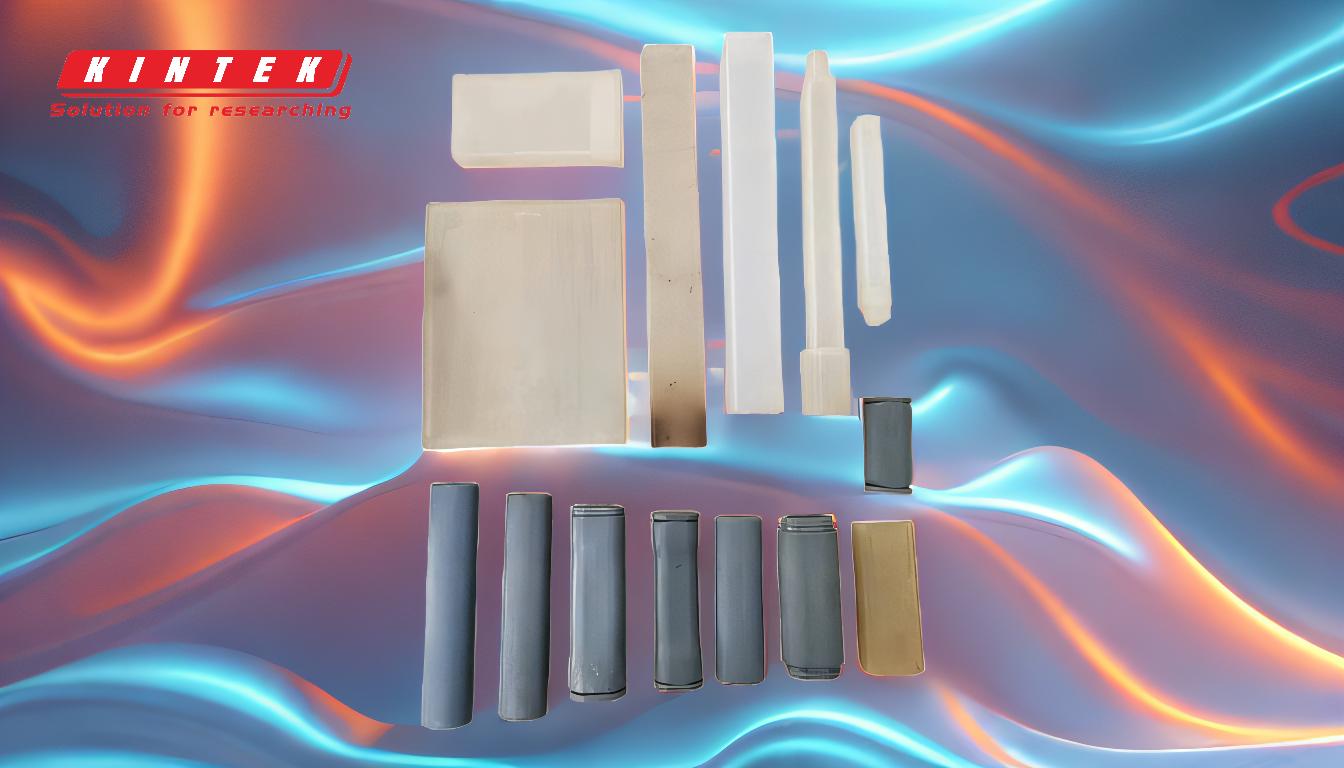
-
Lower Accuracy of Pressed Surfaces:
- Surfaces adjacent to the flexible bag in isostatic pressing often have lower accuracy compared to mechanical pressing or extrusion.
- This is due to the flexible nature of the bag, which cannot provide the same level of precision as rigid molds or dies.
- As a result, subsequent machining is typically required to achieve the desired dimensional tolerances and surface finish.
- This additional step increases both production time and costs, making the process less efficient for applications requiring high precision.
-
Requirement for Expensive Spray-Dried Powder:
- Fully automatic dry bag presses, a type of isostatic pressing, often require the use of relatively expensive spray-dried powder.
- Spray-dried powder is necessary to ensure uniform compaction and flowability in automated systems.
- The higher cost of this specialized powder adds to the overall production expenses, making the process less economical compared to methods that can use cheaper raw materials.
-
Lower Production Rates:
- Isostatic pressing generally has lower production rates compared to extrusion or die compaction.
- The process is slower due to the need for careful loading, pressing, and unloading of materials, especially in wet-bag systems.
- This limitation makes it less suitable for high-volume manufacturing, where faster methods like extrusion or die compaction are preferred.
-
Decreased Productivity in Wet-Bag Systems:
- Wet-bag isostatic pressing involves manual or semi-automated loading and unloading of molds, which reduces productivity.
- The process is less automated compared to dry-bag systems, leading to longer cycle times and higher labor costs.
- Additionally, wet-bag systems have higher tooling costs compared to uniaxial pressing, further increasing the overall expense.
-
Limited Automation and Higher Tooling Costs:
- Isostatic pressing, particularly wet-bag systems, has limited automation capabilities, which restricts its efficiency and scalability.
- The need for specialized molds and tooling increases initial setup costs, making it less attractive for small-scale or low-budget projects.
- These factors contribute to the overall higher cost and lower productivity of isostatic pressing compared to alternative methods.
-
Comparison with Alternative Methods:
- While isostatic pressing offers advantages like high-density compactions and the ability to produce complex shapes, its disadvantages make it less competitive for certain applications.
- Methods like extrusion and die compaction offer higher production rates, better precision, and lower material costs, making them more suitable for high-volume or precision-critical manufacturing.
- The decision to use isostatic pressing must therefore weigh its unique benefits against these significant drawbacks.
Summary Table:
Disadvantage | Description |
---|---|
Lower Accuracy of Pressed Surfaces | Requires additional machining due to flexible bag limitations. |
Expensive Spray-Dried Powder | Higher material costs for fully automatic dry bag presses. |
Lower Production Rates | Slower compared to extrusion or die compaction, unsuitable for high-volume needs. |
Decreased Productivity (Wet-Bag) | Manual loading/unloading reduces efficiency and increases labor costs. |
Limited Automation & High Tooling | Higher setup costs and restricted scalability due to specialized tooling. |
Considering alternative methods for your project? Contact us today to explore the best solution for your needs!