Pyrolysis of plastic to fuel is a promising technology for sustainable development, but it faces several significant disadvantages that hinder its widespread adoption. These include high operational and investment costs, technical challenges such as energy losses and reactor design limitations, and environmental concerns like the production of harmful pollutants and hazardous waste. Additionally, pyrolysis oil's lower quality, instability, and corrosiveness make it less economically competitive and difficult to handle. Addressing these issues requires ongoing research and development to improve the technology's efficiency, reduce costs, and mitigate environmental impacts.
Key Points Explained:
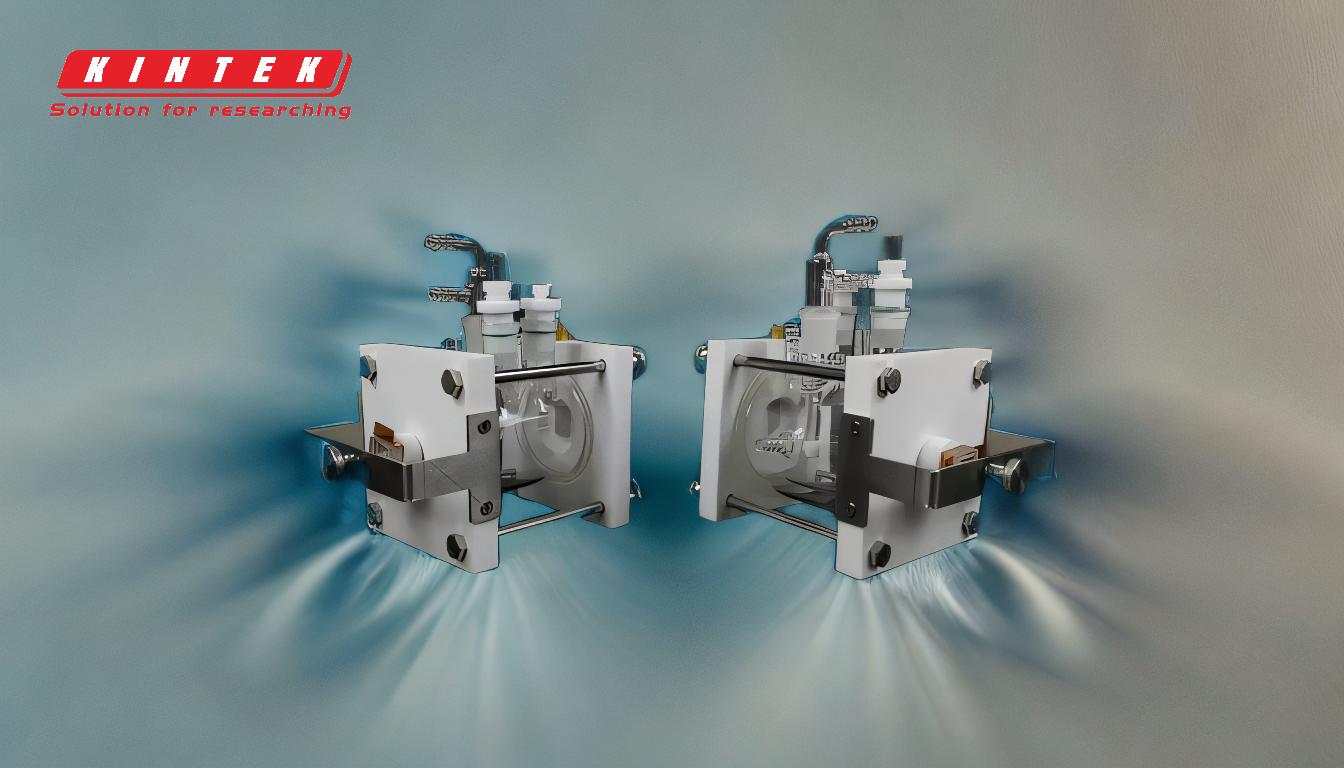
-
High Operational and Investment Costs:
- Pyrolysis plants require significant capital investment for construction and maintenance.
- Operational costs are high due to the need for sophisticated monitoring and auto-adjusting systems to handle variable feed materials like municipal solid waste (MSW).
- The necessity of air purification installations to treat flue gases adds to the overall expenses.
-
Technical Challenges:
- Energy Losses: Reducing parasitic energy losses is crucial to improving the efficiency of pyrolysis processes.
- Reactor Design: Current reactor designs need enhancement to optimize the pyrolysis process and increase bio-oil yields.
- Feedstock Logistics: Efficient handling and preprocessing of feedstock are essential to ensure consistent quality and performance.
- Heating Rate: Increasing the biomass heating rate can improve the overall efficiency of the pyrolysis process.
- Metal and Ash Accumulation: The accumulation of metal and ash in reactor bed materials can impede the pyrolysis process and reduce bio-oil yields.
-
Environmental Concerns:
- Pollutants: The release of harmful pollutants such as nitrous oxides and sulfur dioxides during the burning of pyrolysis oil poses environmental and health risks.
- Hazardous Waste: The production of ashes with high heavy metal content is considered dangerous waste and requires careful disposal.
- Health Risks: Energy recovery processes can pose health risks to workers and nearby communities due to exposure to harmful substances.
-
Quality and Handling Issues of Pyrolysis Oil:
- Lower Quality: Pyrolysis oil generally has lower quality compared to conventional fuels, making it less economically competitive.
- Instability: The oil's instability and corrosiveness require careful handling and specific storage conditions.
- Varying Composition: The complex mixture of oxygenated compounds in pyrolysis oil necessitates specific quality parameters for different applications, complicating its use.
-
Economic and Market Challenges:
- Economic Competitiveness: The current lack of economic competitiveness of pyrolysis oil limits its commercial adoption.
- Impact on Other Processes: The implementation of pyrolysis technology could potentially impact other waste-to-fuel processes, such as solid waste-to-fuel, economically.
-
Global Adoption and Scalability:
- Limited Adoption: The limited global adoption of pyrolysis technology makes it challenging to scale up and apply in real-world conditions.
- Variable Feed Materials: The difficulty of treating variable feed materials like MSW requires advanced and adaptable systems, which are not yet widely available.
In summary, while pyrolysis of plastic to fuel offers a sustainable solution for waste management and energy recovery, it faces significant challenges that need to be addressed. These include high costs, technical limitations, environmental concerns, and issues related to the quality and handling of pyrolysis oil. Overcoming these disadvantages will require continued research, development, and innovation to make pyrolysis a viable and widely adopted technology.
Summary Table:
Category | Key Challenges |
---|---|
High Costs | Significant capital investment, high operational expenses, air purification costs |
Technical Challenges | Energy losses, reactor design limitations, feedstock logistics, heating rate |
Environmental Concerns | Harmful pollutants, hazardous waste, health risks |
Oil Quality Issues | Lower quality, instability, corrosiveness, varying composition |
Economic Challenges | Lack of competitiveness, impact on other waste-to-fuel processes |
Global Adoption | Limited scalability, difficulty with variable feed materials |
Interested in learning more about pyrolysis technology? Contact us today for expert insights and solutions!