The two-plate mold, while widely used in injection molding, has certain disadvantages that can impact production efficiency, cost, and design flexibility. The primary drawbacks include limitations in gate placement, which restrict design options and may lead to aesthetic or functional compromises. Additionally, the need to remove the runner system after molding increases labor and material waste, affecting overall efficiency and sustainability. Below, we delve into these disadvantages in detail, providing a comprehensive understanding of their implications for equipment and consumable purchasers.
Key Points Explained:
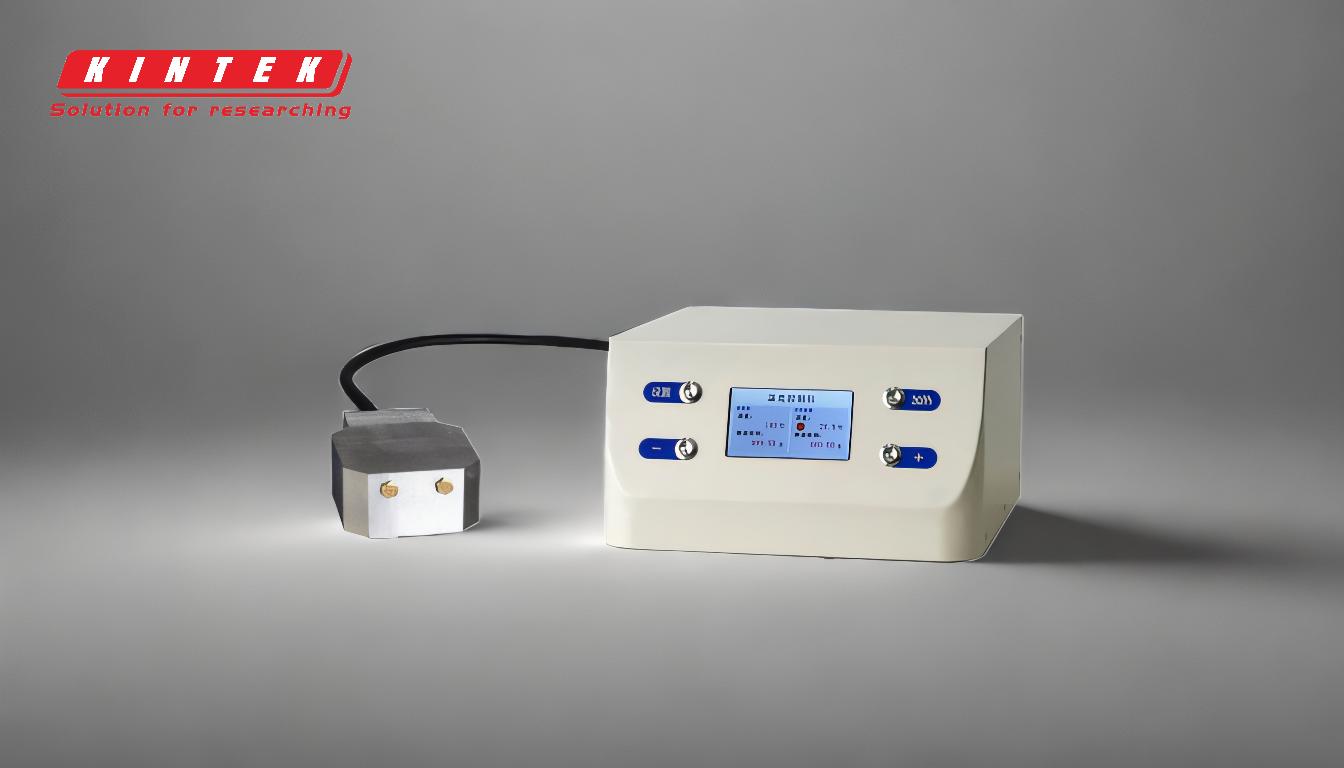
-
Limited Gate Placement Options:
- Explanation: In a two-plate mold, the gate (the point where molten plastic enters the mold cavity) is typically restricted to the side of the part unless special measures are taken. This limitation can affect the design and functionality of the final product.
-
Implications:
- Design Constraints: Side gates may not be suitable for parts requiring aesthetic finishes or those with complex geometries. This can limit the versatility of the mold for different product designs.
- Increased Complexity: Implementing special measures to place gates in alternative locations can increase mold complexity and cost, making it less economical for simpler projects.
-
Runner System Removal:
- Explanation: After injection molding, the runner system (the channels through which molten plastic flows to the mold cavity) must be removed from the finished part. This is a manual or semi-automated process that adds to the production cycle.
-
Implications:
- Increased Labor Costs: The need to remove runners manually or with additional machinery increases labor costs and production time.
- Material Waste: The runner system is typically discarded after removal, leading to material waste. This can be a significant concern for sustainability-focused operations.
- Post-Processing Requirements: The removal process may require additional equipment or steps, such as trimming or grinding, further complicating the production workflow.
-
Impact on Production Efficiency:
- Explanation: The combined effect of limited gate placement and runner removal can reduce overall production efficiency.
-
Implications:
- Longer Cycle Times: The need to remove runners and potential design constraints can extend the production cycle, reducing throughput.
- Higher Operational Costs: Increased labor, material waste, and potential need for additional equipment contribute to higher operational costs.
- Scalability Issues: For large-scale production, these inefficiencies can become significant, making two-plate molds less suitable for high-volume manufacturing.
-
Material Considerations:
- Explanation: The type of material used in injection molding can exacerbate the disadvantages of two-plate molds.
-
Implications:
- Material Compatibility: Some materials may not flow well through side gates, leading to defects or inconsistencies in the final product.
- Thermal Properties: Materials with specific thermal properties may require more precise gate placement, which can be challenging with two-plate molds.
-
Alternative Solutions:
- Explanation: While two-plate molds have their disadvantages, understanding alternative solutions can help mitigate these issues.
-
Implications:
- Three-Plate Molds: These molds allow for more flexible gate placement and automatic runner separation, reducing labor and material waste.
- Hot Runner Systems: These systems eliminate the need for runner removal by keeping the plastic molten in the runner system, improving efficiency and reducing waste.
- Design Optimization: Working closely with mold designers to optimize gate placement and runner design can help mitigate some of the disadvantages of two-plate molds.
In conclusion, while two-plate molds are a common choice for injection molding, their limitations in gate placement and the need for runner removal can impact production efficiency, cost, and design flexibility. Understanding these disadvantages is crucial for equipment and consumable purchasers to make informed decisions and explore alternative solutions that better meet their production needs.
Summary Table:
Disadvantage | Explanation | Implications |
---|---|---|
Limited Gate Placement Options | Gates are typically restricted to the side, affecting design and functionality. | - Design constraints for aesthetics/complex geometries. - Increased mold costs. |
Runner System Removal | Manual or semi-automated removal of runners post-molding. | - Higher labor costs. - Material waste. - Additional post-processing steps. |
Impact on Production Efficiency | Combined effects of gate limitations and runner removal. | - Longer cycle times. - Higher operational costs. - Scalability challenges. |
Material Considerations | Material type can worsen two-plate mold issues. | - Compatibility issues with side gates. - Thermal property challenges. |
Alternative Solutions | Options to mitigate two-plate mold drawbacks. | - Three-plate molds. - Hot runner systems. - Design optimization. |
Discover how alternative solutions can improve your injection molding process—contact us today for expert advice!