The productivity and grinding performance of a ball mill are influenced by a variety of factors, including the design of the mill, the properties of the material being ground, and the operational parameters. Key factors include the drum diameter and its ratio to length, the physical-chemical properties of the feed material, the size and filling of the grinding balls, the shape of the armor surface, the rotation speed, the fineness of milling, and the timely removal of the ground product. Additionally, the residence time of the material in the mill, the nature of the grinding material, and the feed rate and level in the vessel also play significant roles. Understanding these factors can help optimize the performance and efficiency of a ball mill.
Key Points Explained:
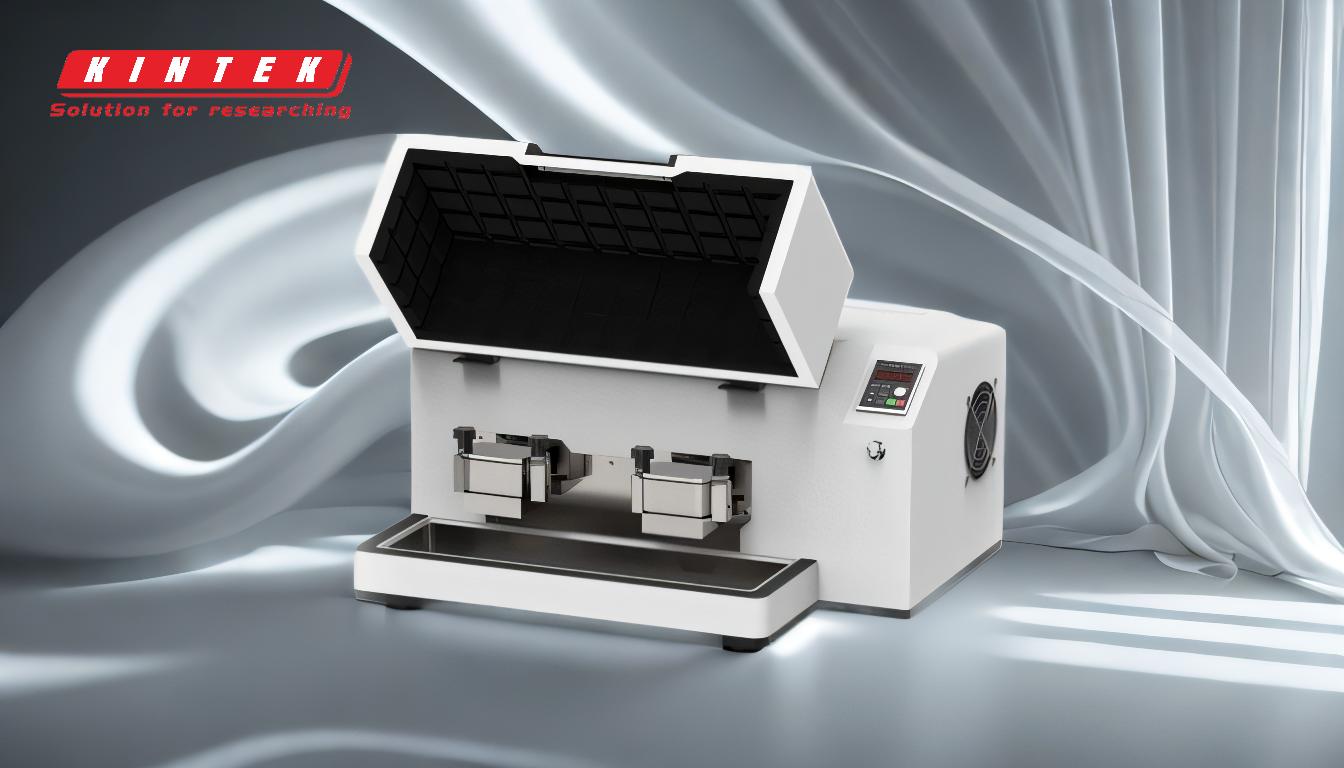
-
Drum Diameter and Length-to-Diameter Ratio (L:D Ratio)
- Drum Diameter: Larger drum diameters generally increase the mill's capacity and productivity. However, the relationship is not linear, and other factors must be considered.
- L:D Ratio: The optimal length-to-diameter ratio for a ball mill is typically between 1.56 and 1.64. This ratio affects the residence time of the material in the mill and the efficiency of the grinding process. A ratio that is too high or too low can lead to suboptimal grinding performance.
-
Physical-Chemical Properties of Feed Material
- Hardness and Brittleness: Harder materials require more energy to grind, while brittle materials may fracture more easily, affecting the grinding efficiency.
- Moisture Content: High moisture content can lead to clogging and reduced grinding efficiency.
- Particle Size Distribution: The initial size distribution of the feed material can influence the grinding kinetics and the final product size.
-
Ball Filling and Sizes
- Ball Filling: The percentage of the mill volume filled with grinding balls (filling ratio) affects the grinding efficiency. Overfilling or underfilling can lead to inefficient grinding.
- Ball Sizes: The size of the grinding balls influences the impact energy and the surface area available for grinding. A mix of different ball sizes can optimize the grinding process.
-
Armor Surface Shape
- The shape and design of the mill's internal armor (liners) can affect the trajectory of the grinding balls and the efficiency of the grinding process. Smooth liners may reduce wear but can also reduce grinding efficiency, while ribbed or wave-shaped liners can enhance grinding efficiency.
-
Rotation Speed
- Critical Speed: The rotation speed of the mill affects the motion of the grinding balls. Operating below the critical speed (where the balls are not lifted high enough) or above it (where the balls are centrifuged) can reduce grinding efficiency. The optimal speed is typically around 65-75% of the critical speed.
- Impact and Shear Forces: The rotation speed influences the impact and shear forces exerted on the material, which in turn affects the grinding efficiency.
-
Milling Fineness
- The desired fineness of the ground product influences the grinding time and energy consumption. Finer grinding requires more energy and time, and may also require adjustments to other parameters such as ball size and rotation speed.
-
Timely Removal of Ground Product
- Efficient removal of the ground product from the mill is crucial to prevent over-grinding and to maintain optimal grinding conditions. Over-grinding can lead to energy waste and reduced product quality.
-
Residence Time of Material
- The time that the material spends in the mill chamber affects the degree of grinding. Longer residence times generally lead to finer grinding but can also increase energy consumption and wear on the mill.
-
Nature of the Grinding Material
- The specific characteristics of the material being ground, such as its abrasiveness, toughness, and chemical composition, can influence the grinding process and the wear on the mill components.
-
Feed Rate and Level in the Vessel
- The rate at which material is fed into the mill and the level of material in the vessel can affect the grinding efficiency. Overloading the mill can reduce grinding efficiency, while underloading can lead to excessive wear on the grinding media.
-
Filling Ratio of the Mill
- The filling ratio, or the percentage of the mill volume filled with grinding medium, affects the grinding efficiency. An optimal filling ratio ensures that there is enough grinding medium to effectively grind the material without causing excessive wear or energy consumption.
By carefully considering and optimizing these factors, the productivity and efficiency of a ball mill can be significantly improved, leading to better grinding performance and higher-quality products.
Summary Table:
Factor | Impact on Grinding Performance |
---|---|
Drum Diameter & L:D Ratio | Affects capacity, residence time, and grinding efficiency. Optimal L:D ratio is 1.56–1.64. |
Feed Material Properties | Hardness, brittleness, moisture, and particle size distribution influence grinding kinetics. |
Ball Filling & Sizes | Filling ratio and ball size affect grinding efficiency and energy consumption. |
Armor Surface Shape | Liners influence ball trajectory and grinding efficiency. Ribbed liners enhance performance. |
Rotation Speed | Optimal speed (65–75% of critical speed) maximizes impact and shear forces for efficient grinding. |
Milling Fineness | Finer grinding requires more energy and time, impacting overall efficiency. |
Timely Removal of Ground Product | Prevents over-grinding and maintains optimal grinding conditions. |
Residence Time | Longer residence times lead to finer grinding but increase energy consumption. |
Nature of Grinding Material | Abrasiveness, toughness, and chemical composition affect grinding and wear. |
Feed Rate & Level | Overloading or underloading the mill reduces grinding efficiency. |
Filling Ratio | Optimal filling ratio ensures effective grinding without excessive wear or energy waste. |
Optimize your ball mill's performance today—contact our experts for tailored solutions!