The performance and efficiency of sieving are influenced by several factors, including the characteristics of the material being sieved, the design and operation of the sieving equipment, and external environmental conditions. Key material properties such as particle size, agglomeration tendency, and susceptibility to static electricity play a significant role. Additionally, the sieving machine's compatibility with the required filling capacity, its operational settings, and the sieving duration are critical for achieving optimal results. Understanding these factors helps in selecting the right equipment and optimizing the sieving process for specific applications.
Key Points Explained:
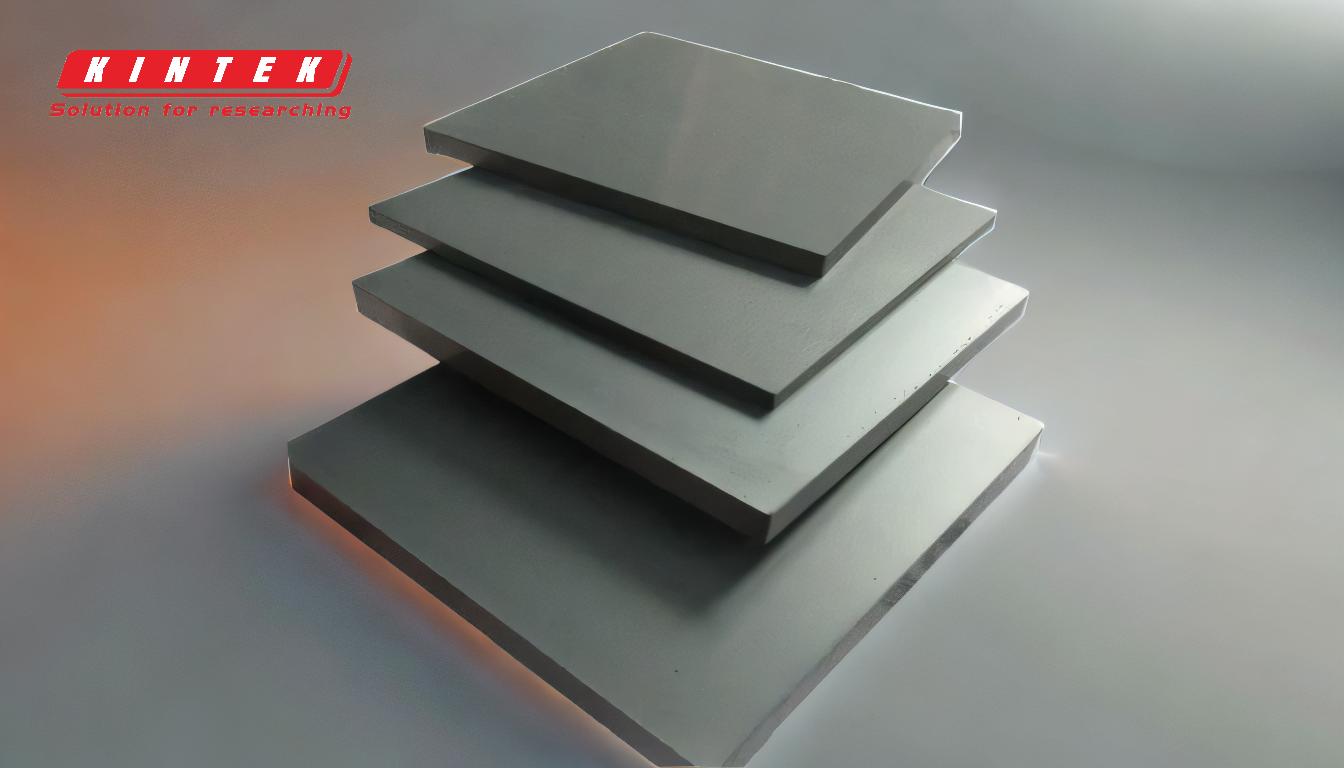
-
Material Characteristics:
- Minimum Particle Size: The smallest particle size to be separated determines the mesh size of the sieve. If the particles are too fine, they may clog the sieve or pass through too slowly, reducing efficiency.
- Agglomeration Tendency: Materials prone to clumping or sticking together can hinder the sieving process. Agglomerated particles may not pass through the sieve, leading to inaccurate results.
- Static Electricity: Materials that generate static electricity can cause particles to adhere to the sieve or each other, reducing sieving efficiency. Anti-static measures may be necessary.
-
Sieving Machine Design and Operation:
- Filling Capacity: The amount of material loaded into the sieve shaker must match the machine's capacity. Overloading can reduce efficiency, while underloading may not utilize the machine's full potential.
- Compatibility with Material: The machine must be suitable for the specific material being sieved. For example, wet sieving may require a different setup than dry sieving.
- Operational Settings: Factors such as vibration intensity, amplitude, and sieving duration must be optimized for the material and desired outcome.
-
Environmental Conditions:
- Humidity and Temperature: High humidity can cause materials to clump, while extreme temperatures may affect the material's properties or the sieve's performance.
- External Vibrations: External disturbances can interfere with the sieving process, leading to inaccurate results.
-
Sieve Mesh and Frame Quality:
- Mesh Size and Shape: The mesh size must be appropriate for the particle size distribution. Irregularly shaped meshes or damaged sieves can lead to inconsistent results.
- Frame Durability: A sturdy frame ensures the sieve remains intact during operation, preventing material loss or contamination.
-
Process Optimization:
- Sieving Duration: The time allocated for sieving must be sufficient to achieve the desired separation without over-processing, which can damage the material or the sieve.
- Cleaning and Maintenance: Regular cleaning and maintenance of the sieving equipment ensure consistent performance and longevity.
By addressing these factors, users can enhance sieving performance and efficiency, ensuring accurate and reliable results for their specific applications.
Summary Table:
Factor | Key Considerations |
---|---|
Material Characteristics | - Minimum particle size - Agglomeration tendency - Static electricity susceptibility |
Machine Design & Operation | - Filling capacity - Compatibility with material - Operational settings (vibration, amplitude, duration) |
Environmental Conditions | - Humidity and temperature - External vibrations |
Sieve Mesh & Frame Quality | - Mesh size and shape - Frame durability |
Process Optimization | - Sieving duration - Cleaning and maintenance |
Maximize your sieving efficiency—contact our experts today for tailored solutions!