Pyrolysis is a complex thermal decomposition process influenced by multiple factors that determine its efficiency, outcomes, and product quality. Key factors include temperature, pressure, residence time, feed characteristics (such as moisture content, particle size, and composition), and the atmosphere within the reactor. Each factor interacts with the others, impacting the thermal degradation of materials and the distribution of end products (gases, liquids, and solids). Understanding and optimizing these factors is crucial for achieving desired results, whether the goal is maximizing gas production, enhancing bio-oil yield, or producing high-quality solid residues like biochar.
Key Points Explained:
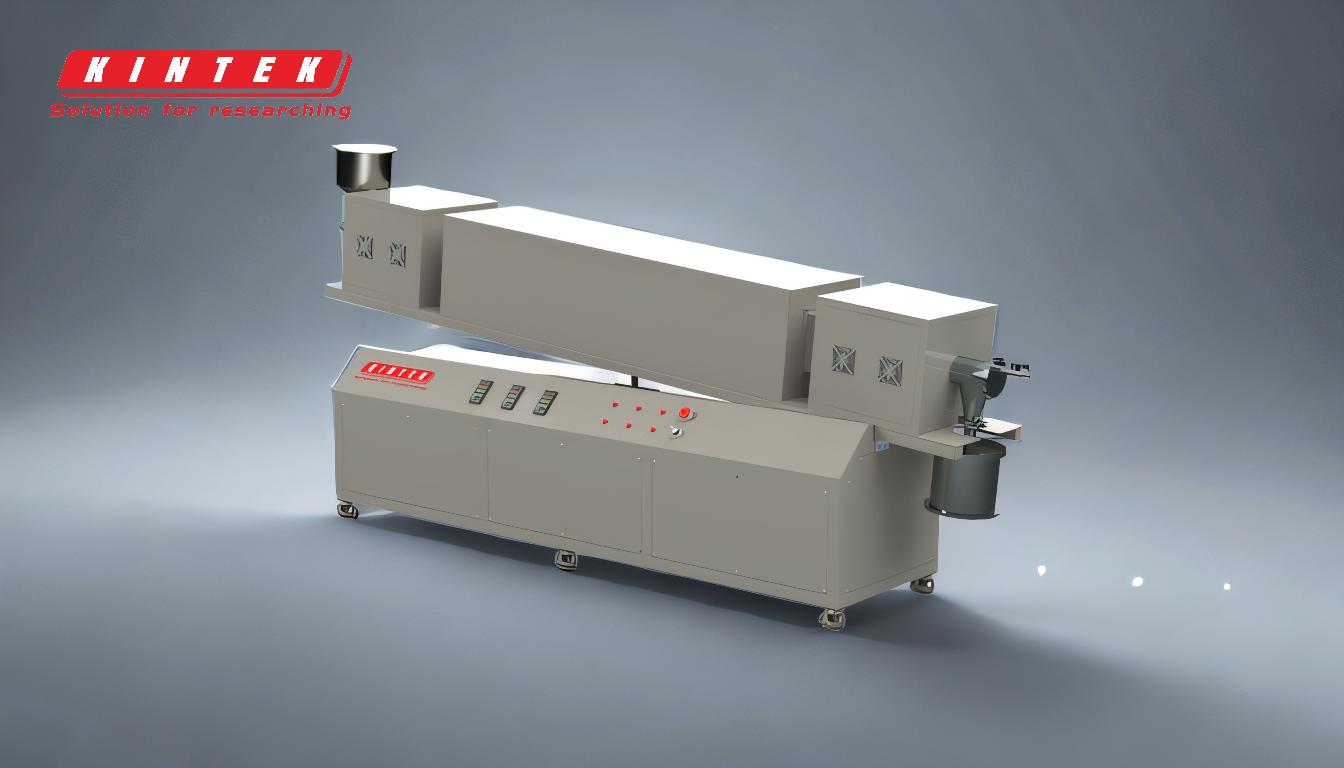
-
Temperature:
- Temperature is one of the most critical factors in pyrolysis. It directly influences the rate of thermal decomposition and the distribution of end products.
- Higher temperatures (typically above 500°C) favor the production of non-condensable gases, such as hydrogen, methane, and carbon monoxide, due to increased cracking of organic compounds.
- Lower temperatures (typically between 300°C and 500°C) promote the formation of bio-oil and solid char, as the thermal degradation is less intense.
- Each component of biomass or waste decomposes at specific temperature ranges, so controlling the temperature ensures optimal conversion of the feedstock.
-
Pressure:
- Pressure affects the physical and chemical reactions during pyrolysis. Higher pressures can influence the yield and composition of gases and liquids.
- In some systems, elevated pressure can enhance the production of certain gases or alter the chemical pathways of decomposition.
- However, pressure must be carefully controlled to avoid safety risks or undesirable reactions.
-
Residence Time:
- Residence time refers to the duration that the feedstock remains in the pyrolysis chamber. It impacts the degree of thermal conversion and the quality of the end products.
- Longer residence times allow for more complete decomposition of the material, leading to higher gas yields and lower char production.
- Shorter residence times may result in incomplete pyrolysis, producing more bio-oil and solid residues.
-
Feed Characteristics:
- Moisture Content: High moisture content in the feedstock can reduce pyrolysis efficiency by requiring additional energy to evaporate water, lowering the effective temperature for thermal decomposition. Dry feedstocks are generally preferred for optimal performance.
- Particle Size and Structure: Smaller particle sizes increase the surface area available for heat transfer, leading to faster and more uniform thermal decomposition. This can enhance the yield of pyrolysis oil and gases.
- Composition: The chemical composition of the feedstock (e.g., cellulose, hemicellulose, lignin) determines its thermal behavior. Different components decompose at different temperatures, affecting the overall process outcomes.
-
Atmosphere:
- The atmosphere within the pyrolysis reactor (e.g., inert gases like nitrogen or reactive gases like steam) influences the chemical reactions and product distribution.
- An inert atmosphere prevents oxidation and ensures that pyrolysis proceeds as a purely thermal decomposition process.
- Reactive atmospheres can introduce additional chemical pathways, potentially altering the composition of the end products.
-
Heating Rate:
- The rate at which the feedstock is heated affects the pyrolysis process. Fast heating rates (flash pyrolysis) favor the production of bio-oil, while slower heating rates promote char formation.
- Rapid heating minimizes secondary reactions, preserving the integrity of the primary pyrolysis products.
-
Reactor Design and Operation:
- The type of pyrolysis reactor (e.g., fluidized bed, fixed bed, rotary kiln) and its operational parameters (e.g., feed rate, temperature control) play a significant role in determining process efficiency and product yields.
- Proper maintenance and operation of the reactor are essential for consistent performance and safety.
-
End Product Goals:
- The desired end products (gases, liquids, or solids) dictate the optimization of pyrolysis conditions. For example, maximizing bio-oil production requires different conditions than maximizing gas or char production.
- Understanding the trade-offs between these goals helps in tailoring the pyrolysis process to specific applications.
By carefully controlling and optimizing these factors, pyrolysis can be tailored to produce the desired mix of gases, liquids, and solids, making it a versatile and valuable process for converting biomass and waste into useful products.
Summary Table:
Factor | Impact on Pyrolysis |
---|---|
Temperature | Higher temps favor gas production; lower temps favor bio-oil and char. |
Pressure | Influences gas and liquid yields; must be controlled to avoid safety risks. |
Residence Time | Longer times increase gas yield; shorter times favor bio-oil and solid residues. |
Feed Characteristics | Moisture, particle size, and composition affect thermal decomposition and product yield. |
Atmosphere | Inert gases prevent oxidation; reactive gases alter chemical pathways. |
Heating Rate | Fast rates favor bio-oil; slow rates promote char formation. |
Reactor Design | Type and operation of the reactor influence efficiency and product yields. |
End Product Goals | Tailor conditions to maximize gases, liquids, or solids based on desired outcomes. |
Ready to optimize your pyrolysis process? Contact our experts today for tailored solutions!