The effectiveness of sieving is influenced by several factors, including the characteristics of the material being sieved, the sieving parameters (such as time, amplitude, and speed), and the compatibility of the sieving machine with the material and application. Material properties like particle size, agglomeration tendency, and static electricity play a significant role in determining sieving efficiency. Additionally, adherence to standards and guidelines, as well as the machine's filling capacity, are critical for achieving optimal results. Understanding these factors helps in selecting the right equipment and parameters for efficient sieving.
Key Points Explained:
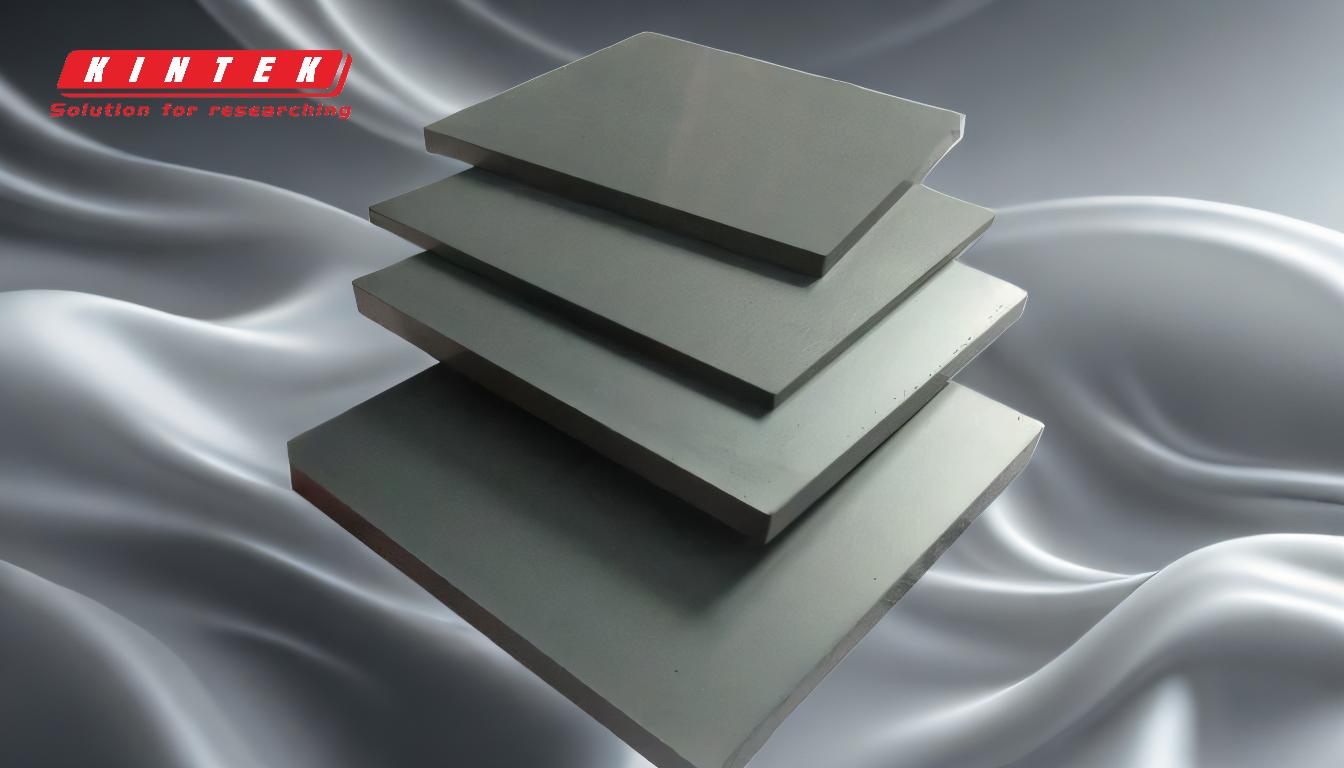
-
Material Characteristics
- Particle Size: The minimum size of particles to be separated directly affects sieving effectiveness. Smaller particles may require finer mesh sizes and longer sieving times.
- Agglomeration: Materials prone to clumping or sticking together can hinder sieving. Anti-static agents or pre-treatment may be necessary to reduce agglomeration.
- Static Electricity: Materials that generate static electricity can cause particles to cling to the sieve mesh, reducing efficiency. Anti-static measures or humidity control may be required.
-
Sieving Parameters
- Sieving Time: The duration of sieving must be optimized based on the material. Too short a time may result in incomplete separation, while too long a time may lead to unnecessary wear on the equipment.
- Amplitude/Speed: The intensity of vibration or movement of the sieve shaker must be adjusted to suit the material. Overly high amplitude or speed can damage delicate particles, while insufficient intensity may fail to separate particles effectively.
- Standards and Guidelines: National, international, and internal standards provide specific recommendations for sieving parameters. Following these ensures consistency and accuracy in results.
-
Machine Compatibility
- Filling Capacity: The sieving machine must match the required capacity for the application. Overloading the sieve can reduce efficiency, while underloading may lead to uneven sieving.
- Device Compatibility: The machine should be compatible with the material's properties and the desired sieving outcomes. For example, wet sieving may require a different machine than dry sieving.
-
Environmental and Operational Factors
- Humidity and Temperature: These can affect material properties like agglomeration and static electricity. Controlling environmental conditions can improve sieving efficiency.
- Maintenance and Calibration: Regular maintenance and calibration of the sieving machine ensure consistent performance and accurate results.
By considering these factors, equipment and consumable purchasers can select the appropriate sieving equipment and parameters to achieve optimal results for their specific applications.
Summary Table:
Factor | Key Considerations |
---|---|
Material Characteristics | - Particle size: Affects mesh size and sieving time. |
- Agglomeration: May require anti-static agents or pre-treatment. | |
- Static electricity: Requires humidity control or anti-static measures. | |
Sieving Parameters | - Time: Optimize for complete separation without over-wearing equipment. |
- Amplitude/Speed: Adjust to avoid particle damage or ineffective separation. | |
- Standards: Follow national/international guidelines for consistency. | |
Machine Compatibility | - Filling capacity: Match machine capacity to application needs. |
- Device compatibility: Ensure suitability for wet or dry sieving. | |
Environmental Factors | - Humidity/Temperature: Control to reduce agglomeration and static issues. |
- Maintenance: Regular calibration ensures consistent performance. |
Need help optimizing your sieving process? Contact our experts today for tailored solutions!