Sieve analysis, while widely used for particle size distribution measurement, has several inherent limitations that can affect its accuracy, efficiency, and applicability. These limitations include restricted resolution due to a limited number of size fractions, ineffectiveness with wet or fine particles, time consumption, and challenges with non-spherical particles. Additionally, sieve clogging, mesh variations, and the need for careful handling further complicate its use. Understanding these limitations is crucial for selecting the appropriate method for specific particle analysis needs.
Key Points Explained:
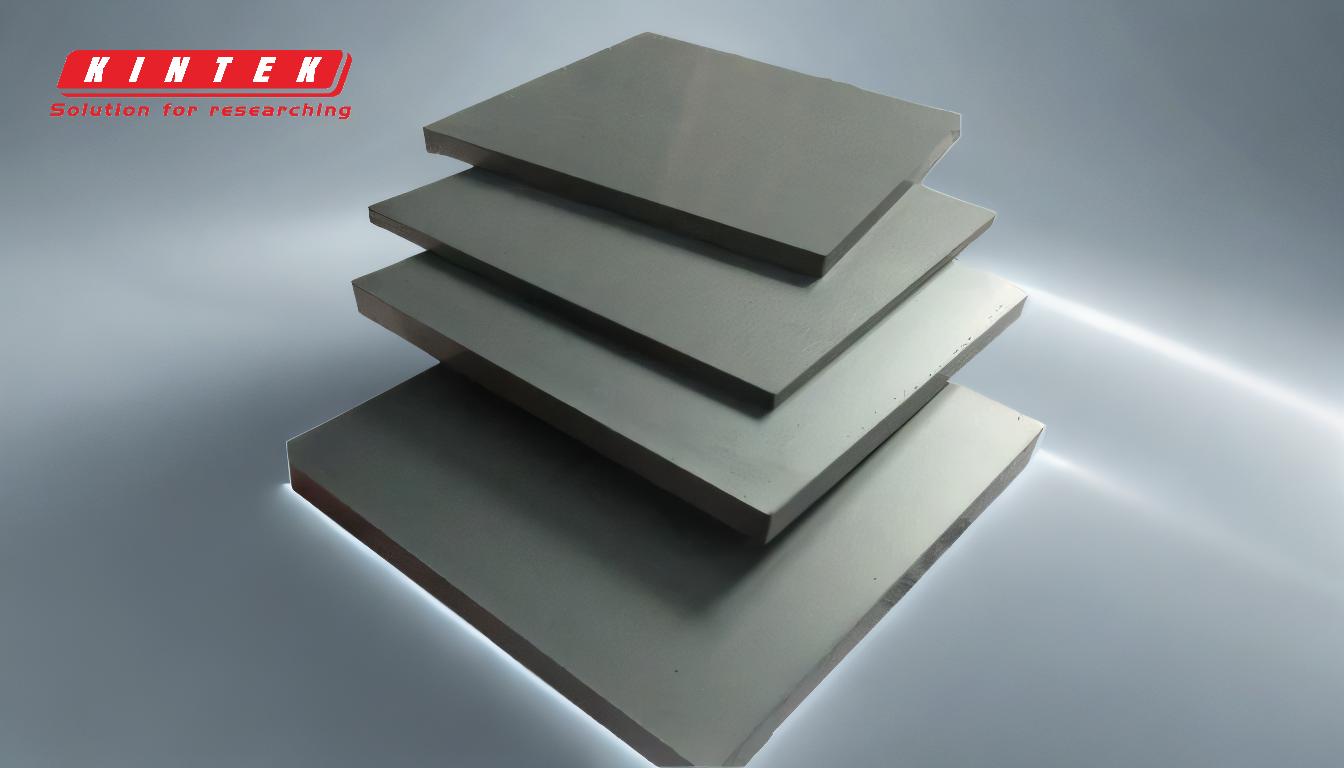
-
Limited Resolution of Particle Size Distribution:
- Sieve analysis typically uses up to 8 sieves, which restricts the number of size fractions that can be measured. This limitation reduces the resolution of the particle size distribution, making it less precise for detailed analysis.
- For applications requiring high-resolution data, alternative methods like laser diffraction or dynamic image analysis might be more suitable.
-
Ineffectiveness with Wet or Fine Particles:
- Sieve analysis is only effective with dry particles. Wet particles can clog the sieve openings, leading to inaccurate results.
- The method has a minimum measurement limit of 50 µm, making it unsuitable for analyzing very fine particles. Special techniques can extend this limit down to 5 µm, but these are not standard and can be cumbersome.
-
Time-Consuming Process:
- The process of sieving can be time-consuming, especially when dealing with large sample sizes or fine particles that require extended shaking periods.
- This can be a significant drawback in industrial settings where time efficiency is crucial.
-
Challenges with Non-Spherical Particles:
- Sieve analysis assumes that all particles are round or nearly spherical. This assumption can lead to unreliable mass-based results for elongated or flat particles.
- Non-spherical particles may not pass through the sieve openings as expected, leading to inaccuracies in size distribution measurements.
-
Sieve Clogging and Distortion:
- Using sieves with very fine pore sizes (less than 20 µm) can lead to clogging or blockage by certain types of solid particles.
- Improper handling and maintenance can cause sieves to become clogged or distorted, further affecting the accuracy of the results.
-
Variations in Mesh Weave:
- Variations in the weave of the mesh material can affect the reproducibility of test results. These variations need to be accounted for in data presentation and analysis.
- Consistent and accurate results require high-quality sieves and regular calibration to minimize these variations.
-
Potential for Particle Size Reduction:
- The mechanical action of sieving can cause further reduction in particle size, especially for brittle materials. This can introduce errors in the measured size distribution.
- Care must be taken to minimize particle breakage during the sieving process.
Understanding these limitations is essential for selecting the appropriate particle size analysis method for specific applications. While sieve analysis is a straightforward and cost-effective method, its limitations may necessitate the use of more advanced techniques for certain types of particles or precision requirements.
Summary Table:
Limitation | Description |
---|---|
Limited Resolution | Only up to 8 sieves, reducing precision for detailed analysis. |
Ineffectiveness with Wet/Fine Particles | Not suitable for wet particles or particles smaller than 50 µm. |
Time-Consuming Process | Extended shaking periods for large or fine samples. |
Challenges with Non-Spherical Particles | Assumes spherical shapes, leading to inaccuracies for elongated or flat particles. |
Sieve Clogging and Distortion | Fine pore sizes (<20 µm) can clog; improper handling distorts results. |
Variations in Mesh Weave | Mesh inconsistencies affect reproducibility. |
Particle Size Reduction | Mechanical action may break brittle particles, skewing results. |
Need a more precise particle size analysis solution? Contact our experts today to find the right method for your needs.