Spark Plasma Sintering (SPS) is an advanced sintering technique that employs a combination of mechanical pressure, electric fields, and thermal fields to achieve rapid densification of powder materials. Key parameters for SPS include temperature (typically ranging from 800°C to 1000°C), pressure (60 MPa to 80 MPa), dwell time (5 minutes to 15 minutes), and heating rates (100°C/min to 300°C/min). The process utilizes pulsed DC currents to generate localized high temperatures and plasma, which facilitates particle bonding and densification. SPS offers advantages such as fast heating speeds, short sintering times, and the ability to maintain the inherent properties of nano-powders, making it an efficient and environmentally friendly sintering method.
Key Points Explained:
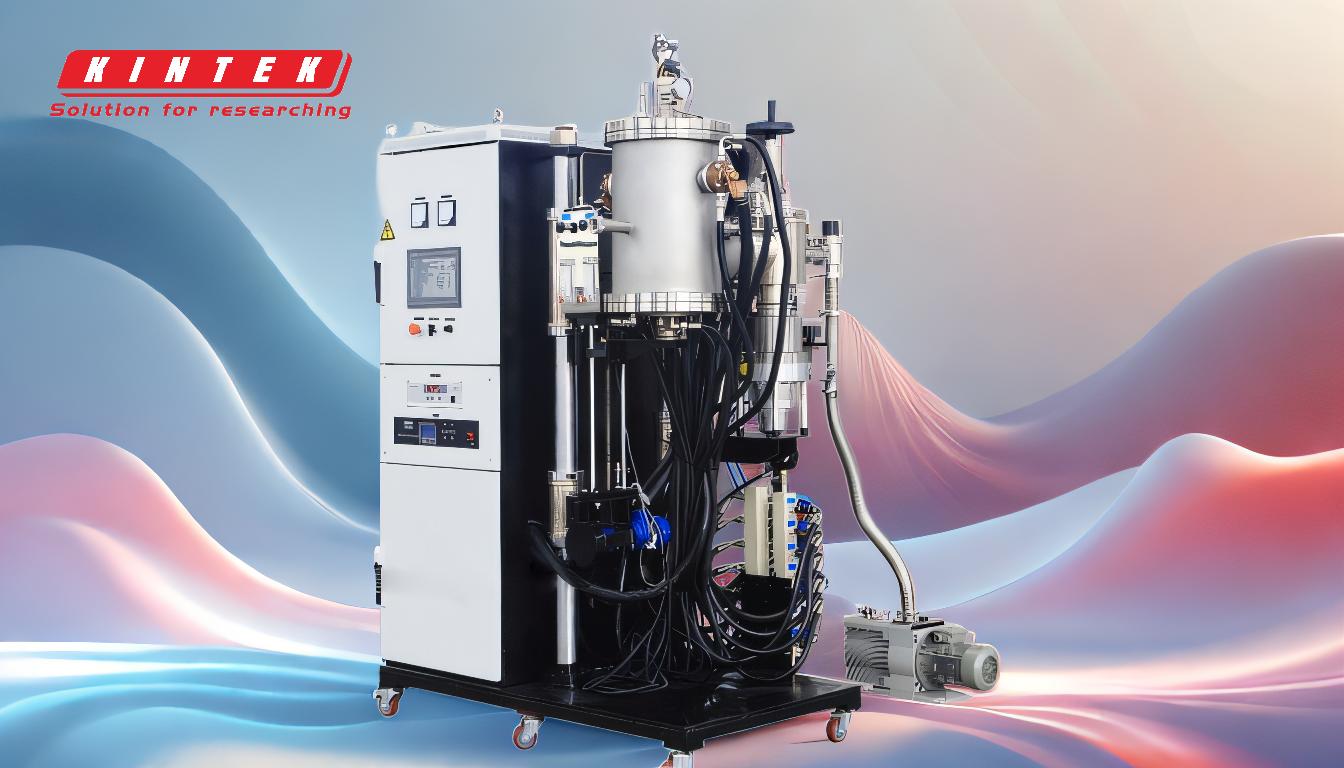
-
Temperature Parameters:
- Range: SPS typically operates at temperatures between 800°C and 1000°C.
- Impact: These temperatures are significantly lower than those required in conventional sintering methods, which helps in preserving the microstructure and properties of the materials being sintered.
-
Pressure Parameters:
- Range: The applied pressure during SPS usually ranges from 60 MPa to 80 MPa.
- Impact: The mechanical pressure aids in the densification process by reducing the gaps between particles and enhancing particle bonding.
-
Dwell Time Parameters:
- Range: Dwell times can vary from 5 minutes to 15 minutes.
- Impact: The dwell time is the period during which the material is held at the sintering temperature. Adequate dwell time ensures complete densification and bonding of particles.
-
Heating Rate Parameters:
- Range: Heating rates in SPS can be as high as 100°C/min to 300°C/min.
- Impact: High heating rates contribute to the rapid densification process, reducing the overall sintering time and minimizing grain growth, which is crucial for maintaining the properties of nano-powders.
-
Electric Current and Plasma Generation:
- Mechanism: SPS uses pulsed DC currents to generate localized high temperatures and plasma between particles.
- Impact: The plasma and high temperatures help in cleaning the particle surfaces by removing contaminants through oxidation or evaporation, and facilitate the formation of necks between particles, leading to densification.
-
Equipment and Setup:
- Punch/Die System: SPS employs a punch/die system similar to hot pressing, where the powder is placed in a die and pressed between two punches under uniaxial mechanical load.
- Heat Source: The die acts as a heat source, and the sample is heated both internally and externally, allowing for rapid heating and cooling rates.
-
Advantages of SPS:
- Fast Heating and Cooling Rates: SPS can achieve heating rates up to 1000°C/min, significantly shortening the sintering time.
- Lower Sintering Temperatures: The process allows for densification at temperatures several hundred degrees lower than conventional sintering methods.
- Controlled Microstructure: The rapid sintering process helps in maintaining the inherent properties of the materials, especially important for nano-powders.
- Energy Efficiency and Environmental Friendliness: The reduced sintering time and lower temperatures contribute to energy savings and reduced environmental impact.
-
Alternative Names and Techniques:
- Field Assisted Sintering Technique (FAST): Another name for SPS, highlighting the role of the electric field in assisting the sintering process.
- Electric Field Assisted Sintering (EFAS): Emphasizes the use of an electric field to enhance densification.
- Direct Current Sintering (DCS): Refers to the use of direct current in the sintering process.
In summary, Spark Plasma Sintering is characterized by its unique combination of temperature, pressure, dwell time, and heating rate parameters, along with the use of pulsed DC currents to generate localized high temperatures and plasma. This results in a rapid, efficient, and environmentally friendly sintering process that is particularly beneficial for advanced materials, including nano-powders.
Summary Table:
Parameter | Range | Impact |
---|---|---|
Temperature | 800°C to 1000°C | Preserves microstructure, lower than conventional methods. |
Pressure | 60 MPa to 80 MPa | Enhances particle bonding and densification. |
Dwell Time | 5 minutes to 15 minutes | Ensures complete densification and bonding. |
Heating Rate | 100°C/min to 300°C/min | Reduces sintering time and minimizes grain growth. |
Electric Current | Pulsed DC currents | Generates plasma for particle cleaning and bonding. |
Advantages | Fast heating, lower temps | Energy-efficient, maintains nano-powder properties, environmentally friendly. |
Learn how Spark Plasma Sintering can revolutionize your material processing—contact us today for expert guidance!