Sieve analysis is a widely used method for determining the particle size distribution of granular materials, but it is not without its limitations and potential sources of error. Key factors that can affect the accuracy of sieve analysis include environmental conditions, such as relative humidity, which can cause fine particles to adhere to sieve components due to electrostatic charges. Additionally, the method is limited by the number of size fractions it can provide, typically up to 8 sieves, which restricts the resolution of particle size distribution. Other limitations include its ineffectiveness with wet particles, a minimum measurement limit of 50 µm, and the time-consuming nature of the process. Understanding these potential sources of error is crucial for obtaining reliable results.
Key Points Explained:
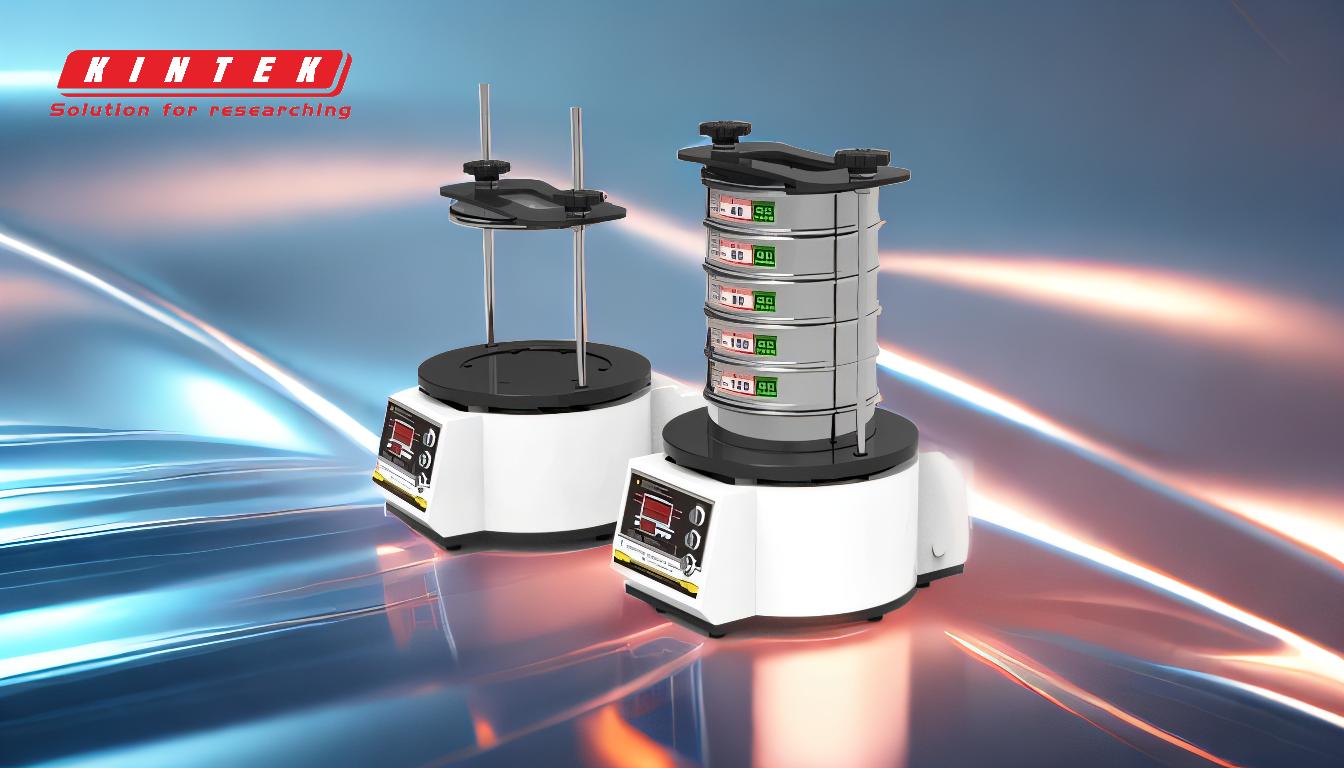
-
Environmental Conditions:
- Relative Humidity: The reaction of the material to ambient conditions, such as relative humidity, can significantly affect the accuracy of sieve analysis. Extremely dry conditions can cause fine powders to adhere to the sieve components and each other due to strong electrostatic charges. This adhesion can lead to inaccurate particle size distribution results.
- Temperature: Variations in temperature can also impact the behavior of particles during sieve analysis. For instance, high temperatures can cause particles to become more fluid, potentially leading to inaccurate sieving.
-
Limitations of Sieve Analysis:
- Number of Size Fractions: Sieve analysis provides a limited number of size fractions, typically up to 8 sieves. This restriction limits the resolution of the particle size distribution, making it difficult to obtain detailed information about the particle sizes within a sample.
- Dry Particles Only: The method is only effective with dry particles. Wet particles can clog the sieve openings, leading to inaccurate results. This limitation necessitates the drying of samples before analysis, which can be time-consuming and may alter the sample's properties.
- Minimum Measurement Limit: Sieve analysis has a minimum measurement limit of 50 µm. Particles smaller than this limit cannot be accurately measured using standard sieves, necessitating the use of alternative methods for fine particle analysis.
- Time-Consuming: The process of sieve analysis can be time-consuming, especially when dealing with large sample sizes or materials that require extended sieving times to achieve accurate results.
-
Sieve Wear and Tear:
- Sieve Damage: Over time, sieves can become damaged or worn, leading to changes in the size of the sieve openings. This wear and tear can result in inaccurate particle size distribution measurements. Regular inspection and maintenance of sieves are essential to ensure consistent and reliable results.
- Clogging: Particles can become lodged in the sieve openings, leading to clogging. This clogging can prevent other particles from passing through the sieve, resulting in an overestimation of the particle size distribution in the larger size fractions.
-
Sample Preparation:
- Sample Size: The size of the sample used in sieve analysis can affect the accuracy of the results. Using too small a sample may not be representative of the entire material, while too large a sample can lead to overloading of the sieves, causing inaccurate results.
- Sample Homogeneity: Ensuring that the sample is homogeneous before analysis is crucial. Non-homogeneous samples can lead to inconsistent results, as different parts of the sample may have varying particle size distributions.
-
Operator Error:
- Inconsistent Sieving: The technique used by the operator during sieving can impact the results. Inconsistent sieving, such as varying the duration or intensity of shaking, can lead to inaccurate particle size distribution measurements.
- Misinterpretation of Results: Errors can also occur during the interpretation of the results. Misreading the weight of the material retained on each sieve or miscalculating the percentage of material in each size fraction can lead to incorrect conclusions about the particle size distribution.
-
Calibration and Standardization:
- Sieve Calibration: Regular calibration of sieves is necessary to ensure that the sieve openings are within the specified tolerances. Failure to calibrate sieves can result in inaccurate particle size measurements.
- Standardization of Procedures: Adhering to standardized procedures for sieve analysis is essential for obtaining consistent and reliable results. Deviations from standardized methods can introduce variability and errors into the analysis.
In conclusion, while sieve analysis is a valuable tool for determining particle size distribution, it is important to be aware of the potential sources of error that can affect the accuracy of the results. By understanding and mitigating these sources of error, it is possible to obtain more reliable and consistent particle size distribution data.
Summary Table:
Factor | Impact on Sieve Analysis |
---|---|
Environmental Conditions | Humidity and temperature variations can cause particle adhesion and inaccurate sieving. |
Limitations | Limited to dry particles, 8 size fractions, and a minimum measurement limit of 50 µm. |
Sieve Wear and Tear | Damaged sieves or clogging can lead to inaccurate particle size distribution measurements. |
Sample Preparation | Sample size and homogeneity are critical for accurate results. |
Operator Error | Inconsistent sieving or misinterpretation of results can introduce errors. |
Calibration | Regular sieve calibration and standardized procedures are essential for consistent results. |
Need help optimizing your sieve analysis process? Contact our experts today for reliable solutions!