RF sputtering is a technique used to deposit thin films, particularly for insulating or non-conductive materials, by utilizing an alternating current (AC) power source at radio frequencies. The process involves alternating the electrical potential between the target material (cathode) and the substrate holder (anode) at a fixed frequency, typically 13.56 MHz. This alternating potential prevents charge buildup on insulating targets, which could otherwise lead to arcing and disrupt the process. During the positive half-cycle, electrons are attracted to the target, creating a negative bias, while in the negative half-cycle, ion bombardment ejects target atoms and gas ions toward the substrate, forming a thin film. RF sputtering is particularly effective for dielectric materials and operates at lower deposition rates compared to DC sputtering, making it suitable for smaller substrates and high-precision applications.
Key Points Explained:
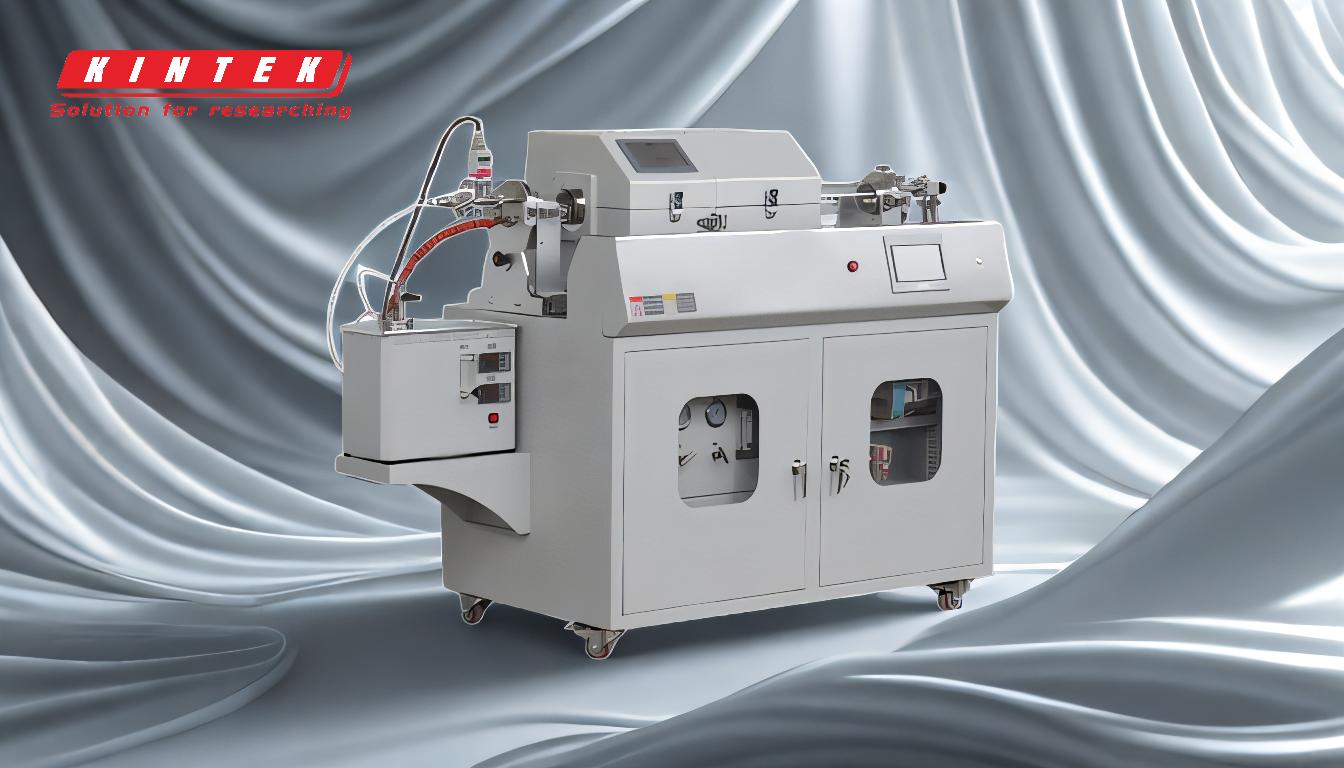
-
Basic Principle of RF Sputtering:
- RF sputtering uses an alternating current (AC) power source, typically at 13.56 MHz, to alternate the electrical potential between the target material and the substrate holder.
- The alternating potential prevents charge buildup on insulating targets, which is a common issue in DC sputtering.
- This process is particularly effective for depositing thin films of non-conductive or dielectric materials.
-
Role of Alternating Current (AC):
- The AC power source alternates the polarity of the target material and substrate holder.
- In the positive half-cycle, the target acts as an anode, attracting electrons and creating a negative bias.
- In the negative half-cycle, the target becomes a cathode, ejecting gas ions and target atoms toward the substrate.
-
Prevention of Charge Buildup:
- Insulating materials tend to accumulate charge during DC sputtering, leading to arcing and process instability.
- RF sputtering alternates the polarity, effectively "cleaning" the target surface of charge buildup during each cycle.
- This ensures a stable sputtering process and high-quality thin film deposition.
-
Ionization and Sputtering Process:
- An inert gas (e.g., argon) is ionized in a vacuum chamber by the RF energy.
- The ionized gas creates a plasma, and high-energy ions bombard the target material.
- Target atoms are ejected and form a fine spray that coats the substrate, creating a thin film.
-
Deposition Rate and Substrate Size:
- RF sputtering typically has a lower deposition rate compared to DC sputtering.
- It is more suitable for smaller substrates due to higher costs and the precision required for insulating materials.
-
Applications of RF Sputtering:
- RF sputtering is widely used in the semiconductor and computer industries for depositing thin films of insulating materials.
- It is also used in the production of optical coatings, solar cells, and other high-precision applications.
-
RF Magnetron Sputtering:
- A variant of RF sputtering, RF magnetron sputtering, uses magnets to trap electrons near the target material.
- This increases the ionization efficiency and allows for faster deposition rates while maintaining the benefits of RF sputtering.
-
Operational Parameters:
- RF sputtering operates at a chamber pressure of 0.5 to 10 mTorr.
- The electron density ranges from 10^9 to 10^11 cm^-3.
- The RF peak-to-peak voltage is typically around 1000 V.
By understanding these principles, one can appreciate the versatility and precision of RF sputtering, particularly for applications involving non-conductive materials and high-quality thin film deposition.
Summary Table:
Key Aspect | Details |
---|---|
Basic Principle | Uses AC power at 13.56 MHz to prevent charge buildup on insulating targets. |
Role of AC | Alternates polarity, enabling stable sputtering for dielectric materials. |
Prevents Charge Buildup | Avoids arcing and ensures high-quality thin film deposition. |
Ionization Process | Inert gas (e.g., argon) ionized to create plasma for target atom ejection. |
Deposition Rate | Lower than DC sputtering, ideal for smaller substrates and precision work. |
Applications | Semiconductors, optical coatings, solar cells, and more. |
Operational Parameters | Chamber pressure: 0.5–10 mTorr; Electron density: 10^9–10^11 cm^-3. |
Discover how RF sputtering can enhance your thin film processes—contact our experts today!