Biomass pyrolysis, while a promising technology for sustainable energy and resource recovery, faces several significant challenges that hinder its widespread adoption and efficiency. These challenges include high capital and operating costs, technical difficulties in scaling up the process, emissions of pollutants, variability in feedstock quality, high energy consumption, and the need for further refining of end products. Additionally, the economic viability of pyrolysis products is currently limited by their higher costs compared to fossil fuels, necessitating environmental credits to justify investment. Addressing these issues requires ongoing research, development, and optimization of the process to make it more economically and environmentally sustainable.
Key Points Explained:
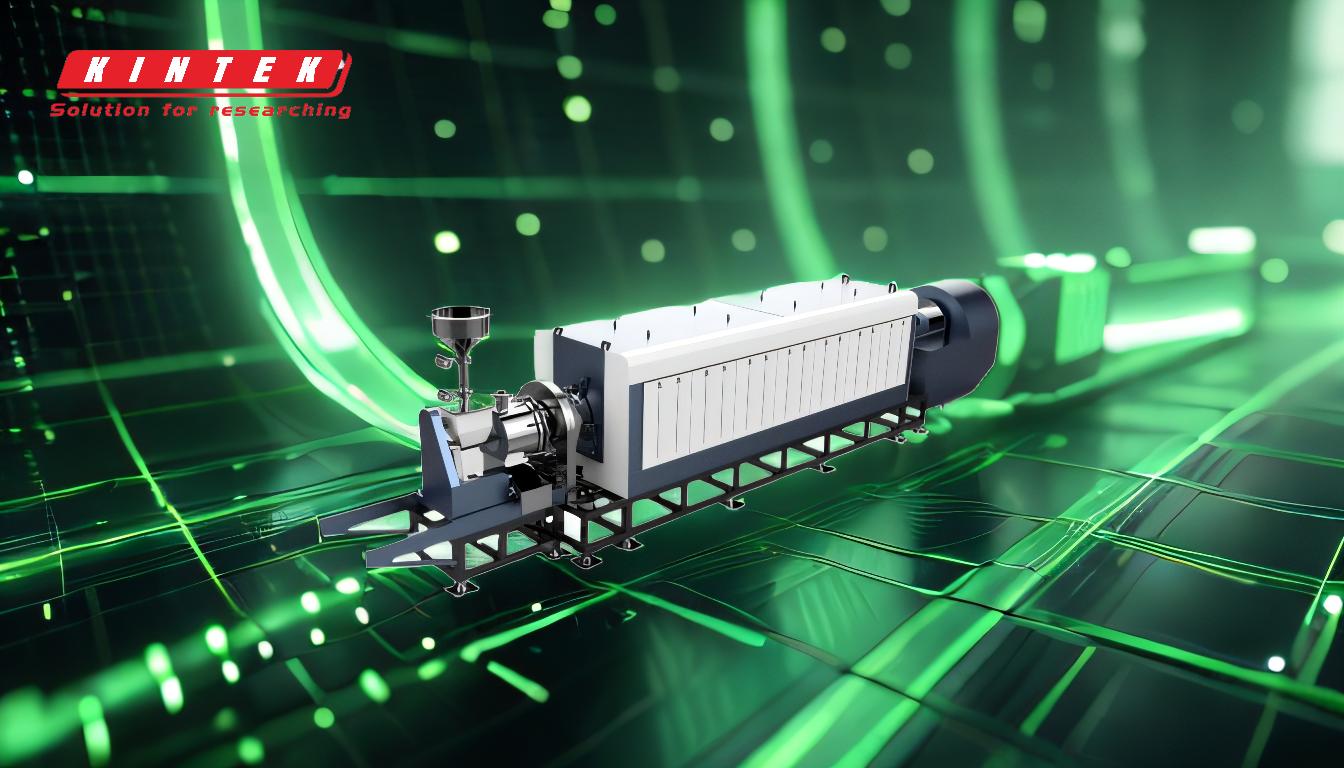
-
High Capital and Operating Costs:
- Biomass pyrolysis requires specialized equipment and machinery, which are expensive to purchase and maintain. The initial investment for setting up a pyrolysis plant is high, and the operational costs, including energy consumption and maintenance, further add to the financial burden.
- The mixed product stream (bio-oil, syngas, and biochar) produced during pyrolysis often requires additional separation and purification processes, which increase the overall cost and complexity of the operation.
-
Technical Challenges in Scaling Up:
- Scaling up biomass pyrolysis from laboratory or pilot-scale to industrial-scale production presents significant technical challenges. These include maintaining consistent process conditions, ensuring uniform feedstock quality, and achieving efficient heat transfer and reaction kinetics at larger scales.
- The scale-up process often encounters unforeseen technical barriers, which can delay commercialization and increase costs.
-
Emissions of Pollutants:
- The pyrolysis process can emit volatile organic compounds (VOCs) and particulate matter, which are harmful to both human health and the environment. Managing these emissions requires additional equipment and controls, further increasing costs.
- Ensuring compliance with environmental regulations adds another layer of complexity and expense to the operation of pyrolysis plants.
-
Variability in Feedstock Quality and Composition:
- Biomass feedstock can vary widely in terms of moisture content, chemical composition, and physical properties. This variability can affect the efficiency and consistency of the pyrolysis process, leading to fluctuations in the quality and yield of the end products.
- Pre-processing of feedstock to achieve uniformity adds to the overall energy consumption and cost.
-
High Energy Consumption:
- Pyrolysis requires high temperatures (typically between 400°C and 700°C) and long residence times to break down the biomass into its constituent products. This results in significant energy consumption, which can offset the environmental benefits of the process.
- The energy-intensive nature of pyrolysis makes it less economically viable, especially for small-scale applications.
-
Variability in the Quality of Final Products:
- The bio-oil produced from pyrolysis often contains high levels of oxygen and water, making it unstable and unsuitable for direct use as a transportation fuel. Refining the bio-oil to improve its quality requires additional processing steps, which increase costs.
- The variability in the quality of bio-oil and other pyrolysis products can limit their marketability and economic value.
-
Economic Viability and Market Competition:
- At current fossil carbon prices, pyrolysis products are significantly more expensive, making it difficult for them to compete in the market. Environmental credits or subsidies may be necessary to make pyrolysis economically viable.
- The higher costs of pyrolysis products can be a barrier to their adoption, especially in regions where fossil fuels are readily available and cheaper.
-
Need for Continuous Research and Development:
- Despite its potential, biomass pyrolysis technology is still in the developmental stage and requires further research to optimize the process, improve product quality, and reduce costs.
- Continuous innovation and technological advancements are needed to address the existing challenges and unlock the full potential of biomass pyrolysis as a sustainable energy solution.
In conclusion, while biomass pyrolysis offers a promising pathway for sustainable energy production and waste management, it is currently hindered by several technical, economic, and environmental challenges. Addressing these issues through ongoing research, technological innovation, and supportive policies will be crucial for the future success and scalability of biomass pyrolysis.
Summary Table:
Challenge | Description |
---|---|
High Capital and Operating Costs | Expensive equipment, maintenance, and additional processing steps increase financial burden. |
Technical Challenges in Scaling Up | Difficulties in maintaining process consistency and efficient heat transfer at industrial scales. |
Emissions of Pollutants | VOCs and particulate matter emissions require costly controls and regulatory compliance. |
Variability in Feedstock Quality | Inconsistent feedstock properties affect process efficiency and product quality. |
High Energy Consumption | Energy-intensive process reduces economic viability, especially for small-scale applications. |
Variability in Final Product Quality | Bio-oil instability and refining needs increase costs and limit marketability. |
Economic Viability and Competition | Higher costs compared to fossil fuels necessitate subsidies or environmental credits for adoption. |
Need for Continuous R&D | Ongoing research is required to optimize processes, improve products, and reduce costs. |
Discover how to overcome biomass pyrolysis challenges and unlock its potential—contact our experts today!