Pyrolysis oil, derived from the thermal decomposition of biomass, is a promising renewable energy source. However, its utilization faces several significant challenges. These include its instability, corrosiveness, low heating value, and the need for further refining and upgrading to meet quality standards for various applications. Additionally, the economic competitiveness of pyrolysis oil is hindered by the costs and complexities of additional processing. Despite these issues, ongoing research and development aim to improve its quality and broaden its commercial applicability.
Key Points Explained:
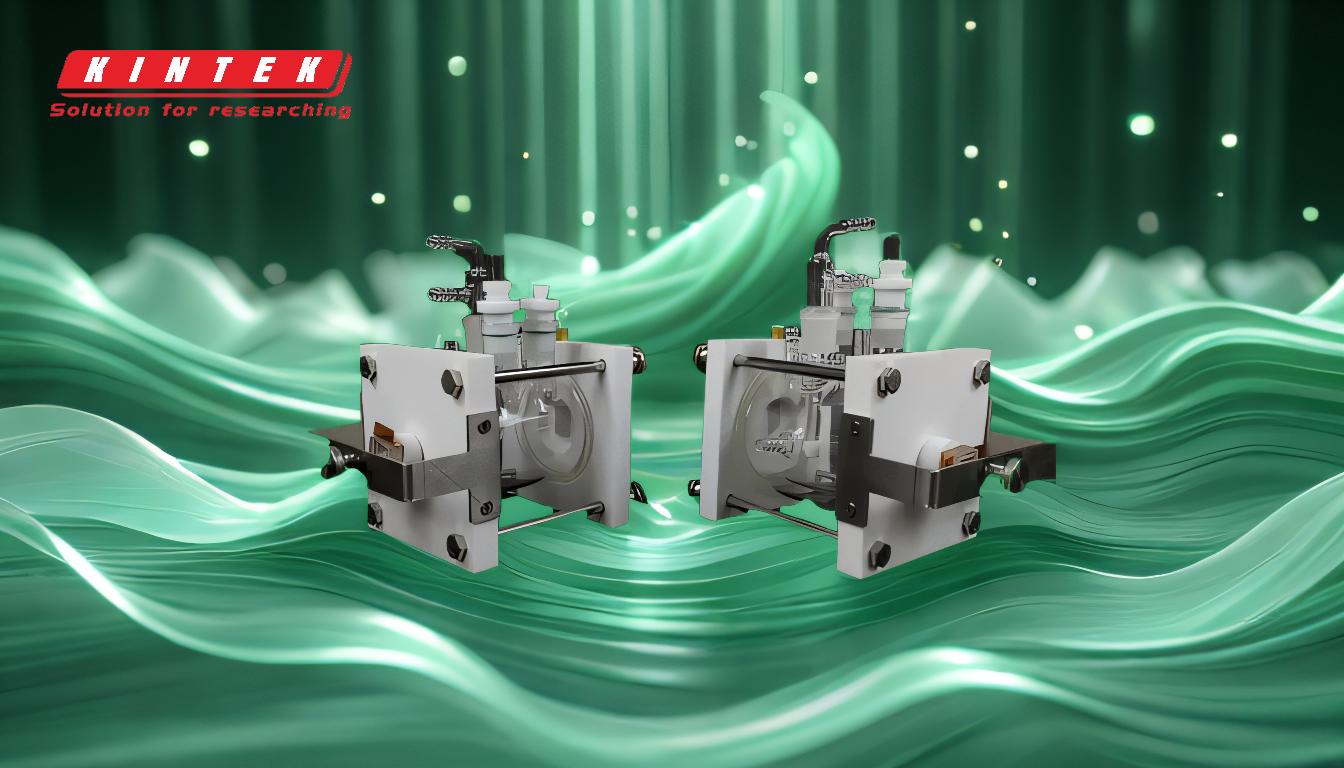
-
Instability of Pyrolysis Oil:
- Explanation: Pyrolysis oil is chemically unstable, particularly when stored or heated. This instability can lead to changes in its composition and properties over time, making it difficult to handle and use reliably.
- Implications: The instability necessitates careful storage conditions and may limit the shelf life of the oil, complicating logistics and increasing costs.
-
Corrosiveness:
- Explanation: Pyrolysis oil is acidic and highly corrosive to metals. This corrosiveness can damage storage tanks, pipelines, and other equipment.
- Implications: Special materials and coatings are required for storage and handling infrastructure, adding to the overall cost and complexity of using pyrolysis oil.
-
Low Heating Value:
- Explanation: The heating value of pyrolysis oil is approximately half that of petroleum-based heating oil by weight. This lower energy density means more oil is required to produce the same amount of energy.
- Implications: The lower heating value reduces the efficiency of pyrolysis oil as a fuel, making it less competitive with conventional fuels.
-
Contaminants and Composition Variability:
- Explanation: Pyrolysis oil can contain various contaminants, and its composition can vary significantly depending on the feedstock and pyrolysis conditions.
- Implications: The presence of contaminants and variability in composition can affect the performance and reliability of the oil, requiring additional processing to ensure consistency and quality.
-
Need for Further Refining and Upgrading:
- Explanation: Pyrolysis oil often requires additional refining and upgrading to be suitable for use as a transportation fuel or other high-value applications. This processing can be complex and costly.
- Implications: The need for additional processing steps increases the overall cost and time required to produce usable fuel from pyrolysis oil, impacting its economic viability.
-
Economic Competitiveness:
- Explanation: Due to its lower quality and the costs associated with refining and upgrading, pyrolysis oil is not currently economically competitive with conventional fossil fuels.
- Implications: The lack of economic competitiveness limits the commercial adoption of pyrolysis oil, despite its potential environmental benefits.
-
Ongoing Research and Development:
- Explanation: Efforts are underway to develop techniques for upgrading pyrolysis oil and improving its quality. These efforts aim to address the current limitations and enhance its commercial applicability.
- Implications: Continued advancements in technology could eventually make pyrolysis oil a more viable and competitive alternative fuel, broadening its use in various applications.
In summary, while pyrolysis oil offers a renewable alternative to fossil fuels, its current challenges in terms of stability, corrosiveness, low heating value, and economic competitiveness need to be addressed. Ongoing research and development are crucial for overcoming these limitations and unlocking the full potential of pyrolysis oil as a sustainable energy source.
Summary Table:
Challenge | Explanation | Implications |
---|---|---|
Instability | Chemically unstable, leading to changes in composition and properties over time | Requires careful storage, limits shelf life, increases costs |
Corrosiveness | Acidic and highly corrosive to metals | Damages infrastructure, necessitates special materials, raises costs |
Low Heating Value | Half the energy density of petroleum-based heating oil | Reduces efficiency, requires more oil for equivalent energy output |
Contaminants & Variability | Contains contaminants; composition varies with feedstock and conditions | Affects performance, requires additional processing for consistency and quality |
Refining & Upgrading | Needs further processing for high-value applications | Increases costs and complexity, impacts economic viability |
Economic Competitiveness | Not cost-competitive with conventional fossil fuels | Limits commercial adoption despite environmental benefits |
Ongoing R&D | Focused on improving quality and commercial applicability | Potential to enhance viability and broaden applications in the future |
Discover how pyrolysis oil can revolutionize renewable energy—contact our experts today to learn more!