Rubber pyrolysis is a thermal decomposition process that breaks down rubber materials in the absence of oxygen, producing valuable by-products. The primary products include pyrolysis oil, carbon black, steel wire, and synthetic gas (syngas). The composition and yield of these products depend on the type of rubber being processed, with tires being a common feedstock. Pyrolysis oil is the most significant output, followed by carbon black, which has applications in various industries. Steel wire, often recovered from tires, can be recycled, while syngas is a mixture of combustible gases used for energy recovery. This process not only helps in waste management but also contributes to resource recovery and sustainability.
Key Points Explained:
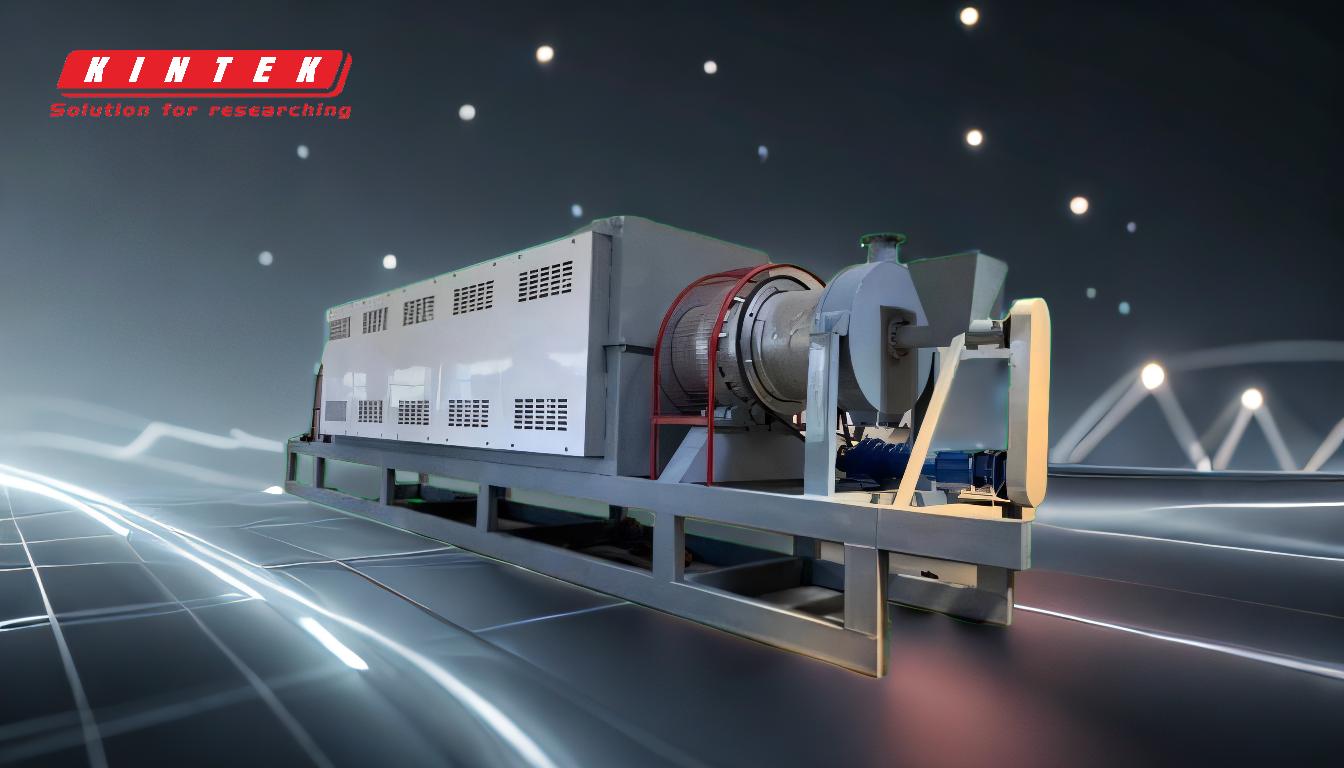
-
Primary Products of Rubber Pyrolysis:
- Pyrolysis Oil: This is the liquid fraction obtained from the condensation of volatile organic compounds (VOCs) released during pyrolysis. It is a complex mixture of hydrocarbons and can be used as a fuel or further refined into chemicals.
- Carbon Black: A solid residue rich in carbon, carbon black is used as a reinforcing agent in rubber products, inks, and coatings. It accounts for 30-35% of the output when processing tires.
- Steel Wire: Recovered from tires, steel wire makes up 8-15% of the output and can be recycled for use in manufacturing.
- Syngas: A mixture of combustible gases such as carbon monoxide, hydrogen, and methane, syngas is used for energy generation within the pyrolysis process or for external applications.
-
Yield Variation Based on Feedstock:
- The yield of pyrolysis products varies depending on the type of rubber being processed. For example, tire pyrolysis typically yields 35-45% oil, 30-35% carbon black, 8-15% steel wire, and 8-15% syngas.
- Other rubber materials or mixed feedstocks may produce different proportions of these products due to variations in their chemical composition.
-
Process and Equipment:
- Rubber pyrolysis involves heating the material in a reactor in the absence of oxygen. The volatile gases produced are then condensed into oil, while non-condensable gases are collected as syngas.
- Key components of a rubber pyrolysis plant include the reactor, condenser, and combustible gas recycling system, all designed to optimize the process and maximize product recovery.
-
Applications of Pyrolysis Products:
- Pyrolysis Oil: Can be used as a substitute for fossil fuels in industrial boilers or further refined into diesel or other chemicals.
- Carbon Black: Widely used in the rubber and plastics industries to enhance material properties.
- Steel Wire: Recycled for use in construction, automotive, and other manufacturing sectors.
- Syngas: Provides a source of renewable energy for heating or electricity generation.
-
Environmental and Economic Benefits:
- Rubber pyrolysis helps reduce waste in landfills and mitigates environmental pollution by converting waste rubber into valuable resources.
- The process supports a circular economy by recovering materials that can be reused in various industries, reducing the need for virgin resources.
By understanding the products and process of rubber pyrolysis, stakeholders can make informed decisions about waste management and resource recovery, contributing to both environmental sustainability and economic efficiency.
Summary Table:
Product | Description | Yield (Tire Pyrolysis) | Applications |
---|---|---|---|
Pyrolysis Oil | Liquid fraction from condensed VOCs; used as fuel or refined into chemicals | 35-45% | Industrial boilers, chemical refining |
Carbon Black | Solid residue rich in carbon; used as a reinforcing agent | 30-35% | Rubber products, inks, coatings |
Steel Wire | Recovered from tires; recyclable for manufacturing | 8-15% | Construction, automotive, manufacturing |
Syngas | Mixture of combustible gases; used for energy recovery | 8-15% | Heating, electricity generation |
Learn how rubber pyrolysis can transform waste into valuable resources—contact us today to explore your options!