Diamond-like carbon (DLC) is a versatile material with a unique combination of properties that make it highly valuable in various industrial applications. It is an amorphous, often hydrogenated carbon material that can be deposited as thin films using different techniques. DLC is characterized by its high hardness, excellent wear and chemical resistance, low coefficient of friction, and high surface smoothness. These properties are largely determined by the ratio of sp3 (diamond-like) to sp2 (graphite-like) carbon bonds in the material. DLC coatings are widely used to enhance durability, reduce friction, and improve the performance of components in corrosive or high-wear environments.
Key Points Explained:
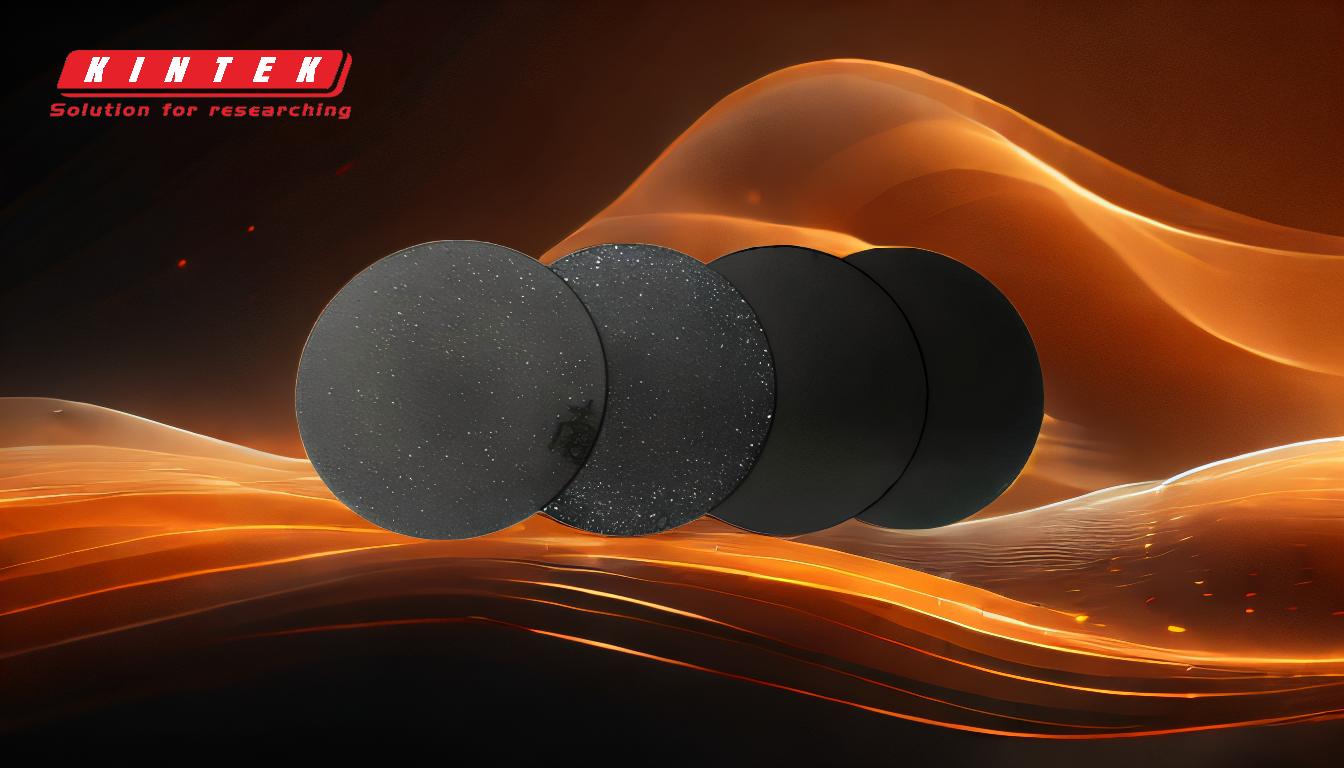
-
Amorphous and Hydrogenated Structure
- DLC is an amorphous material, meaning it lacks a long-range crystalline structure. It often contains hydrogen, which influences its properties.
- The amorphous nature allows for flexibility in tailoring the material's properties based on the deposition method and process parameters.
-
High Hardness
- DLC films exhibit high hardness, comparable to that of diamond, due to the presence of sp3 carbon bonds.
- This hardness makes DLC coatings highly resistant to wear and abrasion, making them ideal for protective applications.
-
Low Coefficient of Friction
- DLC coatings have a low coefficient of friction, which reduces wear and energy loss in sliding or moving components.
- This property is particularly beneficial in applications such as automotive engines, cutting tools, and medical devices.
-
Excellent Wear and Chemical Resistance
- The combination of high hardness and chemical inertness makes DLC highly resistant to wear and corrosion.
- It performs well in harsh environments, including those with exposure to acids, alkalis, and other corrosive substances.
-
Thermal, Electrical, and Optical Properties
- DLC films exhibit good thermal conductivity, electrical insulation, and optical transparency in certain forms.
- These properties make DLC suitable for applications in electronics, optics, and thermal management systems.
-
Dependence on sp3 and sp2 Bonding
- The properties of DLC are determined by the ratio of sp3 (diamond-like) to sp2 (graphite-like) carbon bonds.
- A higher sp3 content increases hardness and wear resistance, while a higher sp2 content enhances electrical conductivity and reduces friction.
-
Surface Smoothness
- DLC coatings are known for their high surface smoothness, which minimizes friction and wear in sliding applications.
- This smoothness also contributes to the aesthetic appeal of coated components.
-
Metastable Nature
- DLC is a metastable material, meaning it is not in its thermodynamic equilibrium state.
- This metastability allows for the creation of unique properties that are not achievable with stable carbon forms like graphite or diamond.
-
Applications in Wear-Protective Coatings
- Due to its high hardness, low friction, and chemical inertness, DLC is widely used in wear-protective coatings for tools, automotive parts, and industrial machinery.
- It is also used in medical devices, such as surgical tools and implants, due to its biocompatibility and wear resistance.
-
Deposition Techniques
- DLC films can be deposited using various techniques, such as chemical vapor deposition (CVD), physical vapor deposition (PVD), and plasma-enhanced chemical vapor deposition (PECVD).
- The choice of deposition method influences the final properties of the DLC coating, allowing for customization based on application requirements.
In summary, diamond-like carbon is a highly versatile material with a unique combination of mechanical, chemical, and physical properties. Its high hardness, low friction, and excellent wear resistance make it a popular choice for protective coatings in a wide range of industries. The ability to tailor its properties through deposition techniques and bonding ratios further enhances its applicability in specialized fields.
Summary Table:
Property | Description |
---|---|
Structure | Amorphous, often hydrogenated, lacks long-range crystalline structure. |
Hardness | High hardness, comparable to diamond due to sp3 carbon bonds. |
Friction | Low coefficient of friction, reduces wear and energy loss. |
Wear & Chemical Resistance | Excellent resistance to wear, abrasion, and corrosion. |
Thermal & Electrical | Good thermal conductivity, electrical insulation, and optical transparency. |
Bonding | Properties depend on sp3 (diamond-like) to sp2 (graphite-like) bond ratios. |
Surface Smoothness | High surface smoothness minimizes friction and wear. |
Applications | Used in wear-protective coatings, automotive parts, medical devices, and more. |
Deposition Techniques | CVD, PVD, and PECVD methods allow for customizable properties. |
Interested in leveraging DLC coatings for your applications? Contact us today to learn more!